Evaluation of open-graded friction course (ogfc) mix design: summary version

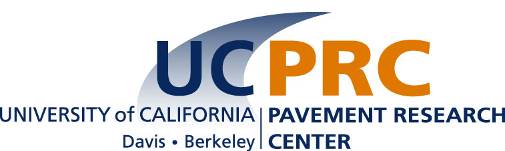
Evaluation of Open-Graded
Friction Course (OGFC)
Mix Design: Summary Version
B.-W. Tsai, J. T. Harvey, and C. L. Monismith
Part of Partnered Pavement Research Program (PPRC) Strategic Plan Element 4.21:
Subtask 2A: Evaluation of Open-Graded Friction Course (OGFC) Mix Design
PREPARED FOR:
PREPARED BY:
California Department of Transportation
University of California
Division of Research, Innovation, and Spatial
Pavement Research Center
UC Davis, UC Berkeley
Office of Roadway Research
DOCUMENT RETRIEVAL PAGE
Summary Report:
Title: Evaluation of Open-Graded Friction Course (OGFC) Mix Design: Summary Version
Authors: Bor-Wen Tsai, J.T. Harvey, and C.L. Monismith
Caltrans Technical Lead and Reviewer: Haiping Zhou
Prepared for:
FHWA No.:
Date Work Submitted:
California Department of
Division of Research,
Innovation, and Spatial Information
Office of Roadway
Strategic Plan No:
Version No:
Stage 6, final version
Abstract: This study evaluates the open-graded friction course (OGFC) mix design proposed by the National Center for Asphalt
Technology (NCAT) in order to suggest revisions to California Test 368, Standard Method for Determining Optimum Binder Content
(OBC) for Open-Graded Asphalt Concrete. Three asphalt types (PG 64-10, PG 64-28 PM, and asphalt rubber [AR]), three aggregate
types (Sacramento, Watsonville, and San Gabriel) and three gradations (coarse, fine, and middle) that comply with Caltrans
specifications of binder and the 1/2 in. OGFC gradation and aggregate quality were used in this study. The NCAT approach includes
selection of optimum gradation, selection of optimum asphalt binder content, and evaluation of moisture susceptibility using a modified
Lottman method in accordance with AASHTO T 283 with one freeze-thaw cycle.
It was found that, regardless of binder and aggregate types, the optimum gradation selected per the NCAT approach—usually a
coarse gradation with fewer fines—did not guarantee the success of an OGFC mix design. None of the mixes with coarse gradation, fabricated using the optimum asphalt binder content, simultaneously met the criteria for percent air-void content, draindown, and Cantabro loss. The resulting test data also show that binder type is the most significant factor affecting both draindown performance and Cantabro performance.
This study proposes a volumetric-based OGFC mix design (1) to provide a better way to determine the initial binder content rather
than basing it on the bulk specific gravity of the aggregate blend as suggested by NCAT; (2) to account for asphalt absorption; and (3) to allow direct selection of trial binder contents to prepare specimens for performance testing.
Accordingly, an OGFC mix design procedure integrated with volumetric design and performance testing is proposed. A moisture
susceptibility test in accordance with AASHTO T 283 is known to have considerable within- and between-variations of test results. Thus, the Hamburg Wheel-Track Device test seems to be a better candidate to evaluate moisture susceptibility. However, further study is required to establish how Hamburg performance results relate to field performance.
Keywords:
OGFC, mix design, performance specification, draindown, Cantabro loss, Hamburg Wheel-Track Device test
Proposals for implementation:
Related document:
Evaluation of Open-Graded Friction Course (OGFC) Mix Design, by B.-W. Tsai, J. T. Harvey, and C. L. Monismith. UCPRC-RR-2012-09. September 2012. (In progress.)
Signatures
First Author
Technical
Principal
Caltrans
Caltrans
Technical Lead
Contract
Manager
UCPRC-SR-2013-02
TABLE OF CONTENTS
List of Figures . v
List of Tables . vi
Disclaimer Statement . vii
Project Objectives . vii
List of Abbreviations . viii
List of Test Methods and Specifications . ix
1 Introduction . 1
2 Materials . 3
Asphalt Binders . 3
3 Phase I: Selection of Optimum Gradation . 7
Preparation of Trial Gradations . 7
Selection of Trial Binder Contents . 7
Determination of Voids in Coarse Aggregate . 9
Selection of Optimum Gradation . 12
4 Phase II: Selection of Optimum Binder Content . 17
Specimen Preparation and Data Analyses . 17
Test Results for Air-Void Content Determinations . 17
Test Results for Binder Draindown . 19
Test Results for Cantabro Test . 20
Determination of Optimum Binder Content . 22
Findings of Phase II . 24
5 Phase III: Supplemental Tests . 25
Findings from Phase I and Phase II . 25
Test Plan of Phase III and Specimen Preparation . 25
Test Results and Analyses . 27
5.3.1 Comparison of Percent Air-Void Content . 27
5.3.2 Draindown Test Results and Analysis . 28
5.3.3 Cantabro Test Results and Analysis of Phase III . 29
UCPRC-SR-2013-02
5.3.4 Cantabro Test Results and Analysis Using Phase I Specimens . 31
5.3.5 HWTD Test Results and Analysis . 32
Surface Area Versus Equivalent Asphalt Film Thickness Versus Cantabro Loss . 36
5.4.1 Calculations of Surface Area and Equivalent Asphalt Film Thickness . 36
5.4.2 Correlation of Cantabro Loss and Mix Properties . 40
Findings of Phase III . 41
6 Development of OGFC Mix Design Chart . 43
Weight-Volume Relationships . 43
Sensitivity Study of Weight-Volume Relationship . 44
Construction of OGFC Mix Design Chart . 46
6.3.1 Calibration of Asphalt Absorption Using Phase I Data. 47
Advantages of the OGFC Mix Design Chart and Issues to be Resolved . 52
Proposed OGFC Mix Design Procedure . 53
6.5.1 Volumetric Design and Performance Testing . 53
6.5.2 Troubleshooting of OGFC Mix Design . 57
7 Conclusions and Recommendations . 59
Conclusions . 59
Recommendations . 61
8 References . 63
Appendix A . 64
UCPRC-SR-2013-02
LIST OF FIGURES
Figure 2.1: The three aggregates graded by size above the No. 8 sieve. 4
Figure 2.2: Proposed one-half inch OGFC trial gradations. 5
Figure 3.1: Wet/dry sieving test results: (a) Sacramento, (b) Watsonville, and (c) San Gabriel. 8
Figure 3.2: Determination of initial binder contents from draindown tests. 9
Figure 3.3: Boxplots of air-void content versus gradation, binder, and aggregate type, respectively. 13
Figure 3.4: Boxplots of air-void content versus aggregate type. 14
Figure 3.5: Boxplots of air-void content versus gradation. 14
Figure 4.1: Boxplot summary of air-void contents for the three aggregates with three binders and three binder
contents for each binder (27 mixes). 18
Figure 4.2: Boxplot summary of the draindown test results. 19
Figure 4.3: Boxplot summary of Cantabro test percent loss results. 21
Figure 5.1: Comparison of air-void contents for the PG64-28PM Watsonville G2 and AR Sacramento G1
mixes (Phase III). 28
Figure 5.2: Comparison of percent draindown between coarse (Phases II) and fine (Phase III) gradations of
PG 64-28 PM mixes containing Watsonville aggregate. 29
Figure 5.3: Boxplot summary of percent Cantabro loss (Phase III). 30
Figure 5.4: Boxplot summary of percent Cantabro loss using Phase I specimens. 31
Figure 5.5: Photographic summary of Cantabro tests using Phase I SGC specimens (50 gyrations). 32
Figure 5.6: HWTD test results for the AR Sacramento G1 mixes. 33
Figure 5.7: HWTD test results for the PG64-28PM Watsonville G2 mixes. 33
Figure 5.8: Cumulative surface area versus sieve size for various gradation types. 37
Figure 6.1: OGFC mix design chart (Sacramento, P
Figure 6.2: OGFC mix design chart (Sacramento, P
= 2.0 percent). 48
Figure 6.3: OGFC mix design chart (Sacramento, P
= 3.0 percent). 49
Figure 6.4: Determination of percent asphalt absorption based on minimum residual sum of squares of percent
air-void content. 50
Figure 6.5: OGFC mix design chart calibrated with P
= 2.69 percent (Sacramento, Phase I). 51
Figure 6.6: OGFC mix design chart calibrated with P
= 2.42 percent (Watsonville, Phase I). 51
Figure 6.7: OGFC mix design chart calibrated with P
= 1.66 percent (San Gabriel, Phase I). 52
Figure 6.8: Proposed OGFC mix design process. 54
Figure 6.9: Proposed OGFC mix design procedure. 56
UCPRC-SR-2013-02
LIST OF TABLES
Table 2.1: Mixing and Compaction Temperatures of Binders . 3
Table 2.2: Proposed One-Half Inch OGFC Trial Gradations . 5
Table 3.1: Minimum Binder Requirements for Aggregates with Varying Bulk Specific Gravity (1) . 7
Table 3.2: Summary of Determination of Voids in Coarse Aggregates (AASHTO T 19 and T 85) . 11
Table 4.1: Summary of Determination of Optimum Binder Content . 23
Table 4.2: Summary of the First- and Second-Level Covariates (Phase II) . 24
Table 5.1: Summary of Test Plan for Phase III . 26
Table 5.2: Summary of HWTD Test Results (Phase III) . 35
Table 5.3: Summary of Asphalt Film Thickness Calculation Based on the Cumulative Surface Areas
Obtained from 1,000 g of Aggregate Blend . 37
Table 5.4: Summary of Calculations of Surface Area and Equivalent Asphalt Film Thickness . 38
Table 5.5: Correlations of Mix Properties and Cantabro Loss . 40
Table 6.1: Summary of the First- and Second-Level Covariates (Sensitivity Study) . 45
Table 6.2: Summary of Test Methods/Specifications Used in OGFC Mix Design Process . 55
Table A.1: Performance-Graded Asphalt Binder Data, PG 64-10, San Joaquin Refinery . 64
Table A.2: Performance-Graded Asphalt Binder Per Caltrans Specification: PG 64-28 PM, San Joaquin
Table A.3: Asphalt-Rubber Binder Testing Results of Asphalt Rubber (AR) (MACTEC) . 66
Table A.4: Aggregate Properties Reported by the Three Suppliers . 67
UCPRC-SR-2013-02
DISCLAIMER STATEMENT
This document is disseminated in the interest of information exchange. The contents of this report reflect the
views of the authors who are responsible for the facts and accuracy of the data presented herein. The contents do
not necessarily reflect the official views or policies of the State of California or the Federal Highway
Administration. This publication does not constitute a standard, specification or regulation. This report does not
constitute an endorsement by the California Department of Transportation (Caltrans) of any product described
For individuals with sensory disabilities, this document is available in braille, large print, audiocassette, or
compact disk. To obtain a copy of this document in one of these alternate formats, please contact: the California
Department of Transportation, Division of Research, Innovation, and Systems Information, MS-83,
P.O. Box 942873, Sacramento, CA 94273-0001.
PROJECT OBJECTIVES
The objective of this study is to evaluate the open-graded friction course (OGFC) mix design procedure
proposed by the National Center for Asphalt Technology (NCAT) and hence to provide a major revision of
California Test 368—Standard Method for Determining Optimum Binder Content (OBC) for Open-Graded
Asphalt Concrete. This was achieved through the following tasks:
Verification of the NCAT procedure—that is, the selection of optimum gradation—based on volumetric
properties (Phase I) criteria.
Evaluation of the NCAT procedure—i.e., the selection of optimum asphalt binder content—according to
draindown and Cantabro (durability) (Phase II) testing performance criteria.
Identification of potential problems in the NCAT OGFC mix design procedure (Phase III). Evaluation of whether it is possible to incorporate the NCAT OGFC mix design procedure into the
CT 368 revision or to develop an appropriate OGFC mix design procedure based on the findings of this
Provide preliminary recommendations for revising CT 368.
UCPRC-SR-2013-02
LIST OF ABBREVIATIONS
American Association of State Highway and Transport Officials
American Society for Testing and Materials
California Department of Transportation
Coefficient of Variation
Compacted Hot-Mix Asphalt
Hamburg Wheel-Track Device
IQR Inter-Quartile
"K factor" of Coarse Aggregate (CT 303)
Moisture Induced Sensitivity Test
National Center for Asphalt Technology
Optimum Binder Content
Open-graded Friction Course
Pressure Aging Vessel
Superpave Gyratory Compaction/Compactor/Compacted
Voids in coarse aggregate for the dry-rodded condition
Voids in coarse aggregate for the compacted mix
UCPRC-SR-2013-02
LIST OF TEST METHODS AND SPECIFICATIONS
Standard Method of Test for Materials Finer Than 75-μm (No. 200) Sieve in Mineral Aggregates by Washing
Standard Method of Test for Bulk Density ("Unit Weight") and Voids in Aggregate
Standard Method of Test for Sieve Analysis of Fine and Coarse Aggregates
Standard Method of Test for Specific Gravity and Absorption of Coarse Aggregate
Standard Method of Test for Bulk Specific Gravity of Compacted Asphalt Mixtures
Standard Method of Test for Theoretical Maximum Specific Gravity and Density of Bituminous Paving Mixtures
Standard Method of Test for Percent Air Voids in Compacted Dense and Open Asphalt Mixtures
Standard Method of Test for Bulk Specific Gravity of Compacted Hot Mix Asphalt (HMA) Using Paraffin-Coated Specimens
Standard Method of Test for Resistance of Compacted Hot Mix Asphalt (HMA) to Moisture-Induced Damage
Standard Method of Test for Determination of Draindown Characteristics in Uncompacted Asphalt Mixtures
Standard Method of Test for Hamburg Wheel-Track Testing of Compacted Hot-Mix Asphalt (HMA)
Standard Method of Test for Bulk Specific Gravity and Density of Compacted Hot Mix Asphalt (HMA) Using Automatic Vacuum Sealing Method
Standard Practice for Open-Graded Friction Course (OGFC) Mix Design; Appendix X2: The Cantabro Abrasion Test
Method of Test for Centrifuge Kerosene Equivalent and Approximate Bitumen Ratio (ABR)
Standard Method for Determining Optimum Bitumen Content for Open Graded Asphalt Concrete
Method of Test for Resistance of Compacted Bituminous Mixture to Moisture Induced Damage
UCPRC-SR-2013-02
UCPRC-SR-2013-02
1 INTRODUCTION
Background
The California Department of Transportation (Caltrans) currently uses California Test 368 (CT 368)
(August 2003) – Standard Method for Determining Optimum Bitumen Content (OBC) for Open Graded Asphalt
Concrete – for Open Graded Friction Course (OGFC) mix design. The OBC determined using this method is
expected to provide a mix with an asphalt film thickness that provides good durability and avoids excessive
asphalt drainage. The K value determined from CT 303 has been used to determine the approximate bitumen
ratio to prepare loose mixes for determining the OBC by using a pre-defined maximum drainage as an
acceptance criterion. Only conventional (unmodified) asphalts were used in CT 368, but in a recent
modification, PG 64-10 asphalt cement replaced AR-4000 material (which was introduced in the 1970s). To
determine the OBC for both the polymer-modified asphalts and asphalt rubber binders introduced more recently,
a factor is now applied to increase the OBC determined for the design mix with the PG 64-10 asphalt cement.
Among several disadvantages associated with the current CT 368 procedure are these: (1) there is no verification
of stone-on-stone contact; (2) there is no determination of volumetric and mechanistic properties of compacted
specimens; and (3) there is no performance testing for aging and moisture damage for the state's different
climate regions.
Recently, staff members of the National Center of Asphalt Technology (NCAT) (1) developed an improved
design procedure for OGFC mixes. This methodology includes (1) materials selection, (2) trial gradations,
(3) selection of an optimum gradation, (4) selection of an optimum binder content, and (5) moisture
susceptibility determination using the modified Lottman method in accordance with AASHTO T 283 with one
freeze-thaw cycle.
The Caltrans Hveem Expert Task Group (ETG) of Caltrans has recommended that CT 368 be revised to
consider incorporation of the elements contained in the NCAT procedure. This summary report presents an
abridged version of the results of a test program—incorporating the recommendation of the Caltrans Hveem
ETG and a proposed OGFC mix design procedure—to replace the current CT 368 method based on these
results. It is a summary version of the more detailed research source report UCPRC-RR-2012-09, Evaluation of
Open-Graded Friction Course (OGFC) Mix Design, September 2012 (2).
UCPRC-SR-2013-02
Objectives
Objectives of this study include the following:
Verify the NCAT procedure – selection of optimum gradation based on volumetric criteria. Evaluate the NCAT procedure – selection of optimum asphalt binder content based on results from the
draindown and Cantabro (durability) tests that satisfy the established NCAT performance criteria.
Identify potential problems in the NCAT OGFC mix design procedure. Evaluate the possibility of incorporating the NCAT OGFC mix design procedure into the revision of
CT 368 or develop an appropriate OGFC mix design procedure based on the findings of this study.
Provide recommendations for the revision of CT 368.
To accomplish these objectives, representative OGFC mixes were used. These mixes were prepared using three
different binders (PG 64-10, PG 64-28 PM, and an asphalt rubber [AR]), three aggregates obtained from
representative sources in California, and three representative gradations within the ½ in. OGFC gradation limits
of Section 39 of the California Standard Specifications (CSS) (3). The following sections contain the abridged
information included in Appendix A.
UCPRC-SR-2013-02
2 MATERIALS
Asphalt Binders
Three binders were used in this study: PG 64-10, PG 64-28 PM, and asphalt rubber (AR). The PG 64-10 and
PG 64-28 PM binders were supplied by the San Joaquin Refinery in Bakersfield, California. Test properties for
these two binders, which met the requirements of Section 92 of the CSS, are summarized in Appendix A,
Table A.1 and Table A.2. The AR binder was supplied by International Surfacing Systems of Modesto,
California. This binder consisted of 18 percent scrap and high natural crumb rubber modifier (CRM); a blend of
75 percent scrap tire CRM and 25 percent high natural CRM; 82 percent PG 64-22; and 2 percent extender oil.
The components for the blend were obtained from the following sources: PG 64-22, VSS Emultech of Redding,
California (G*/sinat°C: 1.12 MPa); extender oil (Raffex 120 ACB), Tricor Refining of Bakersfield,
California; and scrap tire CRM and high natural CRM, Golden By-Products of Ballico, California. Properties of
the AR binder were determined by the MACTEC Engineering and Consulting Laboratory, Phoenix, Arizona,
and are summarized in Appendix A.
Table 2.1 summarizes the mixing and compaction temperatures for the OGFC mixes, based on the suppliers'
recommendations:
Table 2.1: Mixing and Compaction Temperatures of Binders
Binder Type
Mixing Temp.
Compaction Temp.
Aggregates
Three different commercially available aggregate samples with different geological origins (alluvial of mixed
origins [Sacramento] and granite [from a hard rock mine near Watsonville and from an alluvial deposit near San
Gabriel]) were obtained from three different California suppliers.
The Sacramento material was subrounded to subangular compared to the Watsonville and San Gabriel materials,
which were predominantly subangular to angular in shape. The Sacramento aggregate had a relatively smooth
surface texture although the majority of particles contained at least one crushed face with a rough texture. Both
the Watsonville and San Gabriel aggregates consisted of crushed materials with rough surface textures. A
summary of the available aggregate test properties reported by the three suppliers is included in Appendix A,
Table A.4, and photographs of these aggregates graded by size above the No. 8 sieve are shown in Figure 2.1.
UCPRC-SR-2013-02

Figure 2.1: The three aggregates graded by size above the No. 8 sieve.
In this figure, the label on each of the aggregates in the photos represents what was retained by a particular
sieve, i.e., the material passed the adjacent upper sieve and was retained by next smallest sieve, whose size is
indicated. For example, in the photograph showing the No. 8 size, the aggregate represents material that passed
the No. 4 sieve and was retained on the No. 8 sieve.
UCPRC-SR-2013-02
Three trial gradations that fall within the Caltrans one-half inch OGFC limits (3) were selected for this study:
two are near the lower and upper limits of the gradation band, and the third is in the middle. These gradations,
designated G1, G2, and G3 respectively, are listed in Table 2.2 and shown in Figure 2.2.
Table 2.2: Proposed One-Half Inch OGFC Trial Gradations
Target Value
Allowable
Sieve Size
Tolerance
(Coarse)
(Middle)
3/4" 100 ― 100 100 100 1/2"
1/2 – inch OGFC
Sieve Size (mm)
Figure 2.2: Proposed one-half inch OGFC trial gradations.
UCPRC-SR-2013-02
UCPRC-SR-2013-02
3 PHASE I: SELECTION OF OPTIMUM GRADATION
In this phase, initial trial binder contents were determined using the current test methods, CT 368 and
AASHTO T 305. For each combination of the three aggregates, three binders, and three gradations, one loose
mix sample for determining the theoretical maximum specific gravity ( G ) and three Superpave gyratory
compacted (SGC) samples with 50 gyrations were prepared. The optimum gradations were determined from
volumetric criteria based on determinations of the bulk specific gravities of the compacted asphalt mixes (G ),
the air-void contents (V or V ), and the voids in the coarse aggregate of the compacted mixes (VCA
Preparation of Trial Gradations
For the three aggregates to meet the aggregate specifications shown in Table 2.2, a wet/dry sieving process was
followed. Wet sieving, AASHTO T 11, was used to determine the proportion of material passing the No. 200
sieve; particle size distribution of the oven-dried material retained on the No. 200 sieve was then determined
using AASHTO T 27. The results obtained from this process were then used to determine the proper portions of
particle sizes to meet the G1, G2, and G3 gradations. The results are shown in Figure 3.1.
Selection of Trial Binder Contents
According to the NCAT procedure, initial binder content is determined based on the bulk specific gravity (BSG)
of the aggregate, as shown in Table 3.1. Also, higher binder contents should be selected for polymer-modified
and rubberized asphalts, as in the CT 308 method.
Table 3.1: Minimum Binder Requirements for Aggregates with Varying Bulk Specific Gravity (1)
Combined Aggregate
Min. Binder Content
Min. Binder Content
Bulk Specific Gravity
Based on Mass, %
Bulk Specific Gravity
Based on Mass, %
2.40 6.8 2.70 6.1 2.45 6.7 2.75 6.0 2.50 6.6 2.80 5.9 2.55 6.5 2.85 5.8 2.60 6.3 2.90 5.7 2.65 6.2 2.95 5.6
UCPRC-SR-2013-02
Designed Gradations
G1 (Wet/Dry Sieving)
G2 (Wet/Dry Sieving)
G3 (Wet/Dry Sieving)
1/2 – inch OGFC
1/2 – inch OG
Passing by W
Sieve Size (mm)
1/2 – inch OG
ing by W
s 40
San Gabriel
ent Pas 20
Si ve Size (mm)
Figure 3.1: Wet/dry sieving test results: (a) Sacramento, (b) Watsonville, and (c) San Gabriel.
UCPRC-SR-2013-02
Instead of following the NCAT approach for selecting an initial binder content based on the bulk specific
gravity of the combined aggregate, the CT 368 and AASHTO T 305 methods were used to determine the initial
binder contents. Draindown tests were conducted in accordance with AASHTO T 305 except that a No. 8
(2.36 mm) wire mesh basket was used. Loose mix samples were prepared at five binder contents (5.5, 6.0, 6.5,
7.0, and 7.5 percent by weight of aggregate) using a conventional PG 64-10 binder and Watsonville aggregate
with the G3 gradation. At each binder content, two 1,200 gram loose mix samples were prepared for the
draindown tests. Figure 3.2 shows the test results in terms of percent draindown versus binder content with an
upper limit of draindown set at 0.3 percent. A binder content of 6.0 percent was selected as the initial value for
the PG 64-10 mix. An initial binder content of 7.2 percent was determined for the asphalt rubber (AR) by
applying a multiplier of 1.2 to the PG 64-10 mix value of 6.0 percent. An initial binder content of 6.5 percent
was selected for the PG 64-28 PM mix; this value was set between those of the mixes containing the PG 64-10
10 1200 g batchesAC (%): 5.5, 6.0, 6.5, 7.0, 7.5AASHTO Designation: T 305-09
Percent Asphalt Content
Figure 3.2: Determination of initial binder contents from draindown tests.
Determination of Voids in Coarse Aggregate
In the NCAT procedure, the first step in determining the voids in coarse aggregate is to establish the coarse
fraction of the trial aggregate blend. This fraction is the portion of aggregate coarser than the break point sieve,
which is defined as the finest sieve to retain 10 percent or more of the aggregate blend. Accordingly, it can be
seen from Table 2.2 and Figure 2.2 that the No. 8 sieve is the break point sieve for all G1, G2, and G3
gradations. The percent passing the No. 8 sieve for the three gradations are 7 percent for the G1, 18 percent for
the G2, and 12 percent for the G3. The corresponding fines content (< No. 200 sieve) are 1 percent for the G1,
UCPRC-SR-2013-02
3 percent for the G2, and 2 percent for the G3. The purpose of determining the voids in coarse aggregate for the
coarse aggregate fraction (VCA ) is to insure stone-on-stone contact of the aggregate skeleton in the designed
Following AASHTO T 19, Standard Method of Test for Bulk Density ("Unit Weight") and Voids in Aggregate,
a dry-rodded density of the coarse aggregate was determined for the three gradings for each of the three
aggregates. With this value, VCA was calculated for each of the aggregate gradings (total of nine) using the
following equation:
G
where: VCA is the voids in coarse aggregate, dry-rodded condition,
is the unit weight of the coarse aggregate fraction in the dry-rodded condition (kg/m3)
is the unit weight of water (998 kg/m3), and
G is the bulk specific gravity of the coarse aggregate.
The calculated VCA can then be compared with the voids in the coarse aggregate of the compacted mix
) to estimate the existence of stone-on-stone contact; stone-on-stone contact exists only if
. The following equation is used to determine VCA
where: G is the bulk specific gravity of the compacted mix,
P is the percent of coarse aggregate in mix, and
G is the bulk specific gravity of the coarse aggregate.
Table 3.2 provides a summary of the determination of voids in the coarse aggregate (AASHTO T 19 and T 85)
, bulk specific gravity (BSG), and absorption for each aggregate and each gradation. Mean values of
for the three aggregates are: Sacramento, 39.4 percent; Watsonville, 36.9 percent; and San Gabriel,
38.6 percent. The data suggest no strong correlation between VCA and gradation type. The aggregates shown
in the photographs in Figure 2.2 represent the coarse aggregate fractions (break point sieve, No. 8 sieve) for the
three materials.
UCPRC-SR-2013-02
Table 3.2: Summary of Determination of Voids in Coarse Aggregates (AASHTO T 19 and T 85)
Apparent
Aggregate
Specific
Absorption
Gradation
Specific
1. SSD: saturated surface dry. 2. SD: standard deviation.
UCPRC-SR-2013-02
Selection of Optimum Gradation
To select optimum gradations, sample preparation included one loose mix sample to determine the theoretical
maximum specific gravity ( G ) according to the AASHTO T 209 procedure, and three 102 mm diameter SGC
specimens compacted with 50 gyrations to determine the air-void content (V ) and voids in coarse aggregate
V 100 1 mb
where: G is the bulk specific gravity of the compacted mix
G is the theoretical maximum specific gravity of the mix.
Criteria for selecting an optimum gradation for each of the mixes (three aggregates, three gradings, and three
binders) were as follows:
Criteria for Selecting Optimum Gradation
1. Highest V
3. V 18%
The AASHTO T 269 Method, Standard Method of Test for Percent Air Voids in Compacted Dense and Open-
Graded Mixes, was used to determine the air-void content of each compacted mix. In this method, the density of
a specimen is calculated based on its dry mass and volume (measured average height and diameter). N.B., the
SSD (AASHTO T 166A), Parafilm (AASHTO T 275A), and Corelock (AASHTO T 331) procedures are not
applicable for determining G for compacted open-graded asphalt mixes.
Analysis
The full analyses of the test data that are presented in Reference (2) made use of the following: descriptive
statistics including measures of mean, standard deviation (SD), and coefficient of variation (CV); boxplots; tree-
based models; and correlation matrices. In this shortened version of that document, only the analyses presented
in boxplots are included.
UCPRC-SR-2013-02
Figure 3.3 contains a boxplot summary of percent air-void contents by gradation, binder, and aggregate type.
Figure 3.4 and Figure 3.5 illustrate air-void content versus aggregate type and aggregate gradation, respectively.
Asphalt Content:
PG64-10: 6.0%
PG64-28PM: 6.5%
Asphalt Rubber: 7.2%
T: SacramentoW: WatsonvilleS: San Gabriel
G1 (Coarse)
G2 (Fine)
G3 (Middle)
Figure 3.3: Boxplots of air-void content versus gradation, binder, and aggregate type, respectively.
UCPRC-SR-2013-02
San Gabriel
Figure 3.4: Boxplots of air-void content versus aggregate type.
Figure 3.5: Boxplots of air-void content versus gradation.
UCPRC-SR-2013-02
The results of this first phase of the investigation are as follows.
1. Regardless of gradation and binder type, the ranking of air-void content with respect to aggregate type is
Sacramento > San Gabriel > Watsonville, and this reflects the ranking as a function of the VCA
of the aggregates (Sacramento
Gabriel [38.6%] > Watsonville [36.9%]). The two
exceptions are the the AR mixes with G1 gradation and PG 64-28 PM with G2 gradation. If the air-void
contents are categorized by aggregate type, as illustrated in Figure 3.4, then the ranking of air-void
content still follows the same order with means and standard deviations as follows: Sacramento (mean:
22.9%; standard deviation: 3.3%) > San Gabriel (mean: 20.4%; standard deviation: 2.5%) > Watsonville
(mean: 19.2%; standard deviation: 2.5%).
2. From Figure 3.5, regardless of aggregate and binder type, the ranking of air-void content with respect to
gradation is G1 (coarse) > G3 (middle) > G2 (fine). An unexplained anomaly occurs, however, with the
San Gabriel mixes with the PG 64-28 PM and AR binders for the G1 gradation; i.e., the G1 gradation
exhibits the lowest air-void contents of the three types. The overall ranking with respect to gradation
type (as shown in Figure 3.5) is: G1 (mean: 22.3%; standard deviation: 3.8%) > G3 (mean: 21.7;
standard deviation: 1.8%) > G2 (mean: 18.5%; standard deviation: 1.9%).
UCPRC-SR-2013-02
UCPRC-SR-2013-02
4 PHASE II: SELECTION OF OPTIMUM BINDER CONTENT
This section describes the methodology used to select optimum binder contents for the optimum gradations for
the three aggregates, i.e., the three G1 (coarse) gradations selected in the Phase I study described in Chapter 3.
Specimen Preparation and Data Analyses
For each combination of three aggregates (Sacramento, Watsonville, and San Gabriel) and three binder types
(PG 64-10, PG 64-28 PM, and asphalt rubber [AR]), three trial binder contents in increments of 0.7 percent
(target value [TV], TV0.7 percent) were used to determine mix optimum binder contents. The initial TV binder
contents used in this phase were the same target values used for the mixes in Phase I, i.e., PG 64-10
(6.0 percent), PG 64-28 PM (6.5 percent), and asphalt rubber (7.2 percent). The following mixes were prepared
for each binder content: two loose mix samples for the draindown tests, one loose sample for G determination,
and three SGC samples compacted with 50 gyrations to determine air-void contents and for use in Cantabro
Results from the air-void content, draindown, and Cantabro tests were then used to determine optimum binder
contents for each of the mixes (a total of 27). Results of these tests are presented in the form of boxplots. Tree-
based modeling was used to interpret the results included in the boxplots. Detailed test data and analyses are
included in Reference (2).
Test Results for Air-Void Content Determinations
The air-void test data are presented in the form of boxplots in Figure 4.1 for binder type and asphalt content for
the three aggregates. It can be seen from this figure that the majority of the Watsonville test specimens exhibited
the lowest air-void contents. Also, most of these specimens had test results that lie within the specified range of
air-void contents, 18 percent to 22 percent. As might be expected, for the majority of the test specimens, the
higher the binder content, the lower the air-void content.
Based on the analyses:
1. The most important factor affecting percent air-void content is the aggregate. In accordance with the
printed tree structure (2): the Sacramento aggregate exhibited the highest average air-void content,
26.34 percent; the Watsonville aggregate exhibited the lowest, 21.18 percent; and the San Gabriel
aggregate, an intermediate value of 23.65 percent. In Chapter 3 the ranking of VCA values for the
three aggregates was the same, i.e., Sacramento aggregate, 39.4 percent > San Gabriel aggregate,
38.6 percent > Watsonville aggregate, 36.9 percent (Note: only the G1 [coarse)] gradation type was
evaluated in Phase I).
UCPRC-SR-2013-02
2. Regardless of aggregate type and binder type, the smaller the binder content, the larger the percent air-
3. The tree-based modeling (2) suggests that there was some effect of binder type on air-void content for
the San Gabriel aggregate for a binder content greater than 5.9 percent. (The ranking of percent air-void
content was PG 64-28 PM [24.0 percent] > PG 64-10 [23.2 percent] > AR [21.9 percent].)
4. Mixes that satisfied the percent air-void content criterion included those for Watsonville aggregate with
binder contents greater than 6.25 percent (average percent air-void content 20.6 percent) and mixes with
the San Gabriel aggregate AR at binder contents greater than 5.9 percent (average percent air-void
content 21.9 percent).
Normal probability and residual analyses (2) indicate that the tree-based model developed to interpret the
boxplot summary of air-void contents is adequate.
Figure 4.1: Boxplot summary of air-void contents for the three aggregates with three binders and three binder
contents for each binder (27 mixes).
UCPRC-SR-2013-02
Test Results for Binder Draindown
Binder draindown tests were conducted on two loose mix samples for each of the 27 mixes. The tests were
performed at a temperature 15°C ( 27°F) higher than the production temperature, in accordance with
AASHTO T 305. (A No. 8 [2.36 mm] wire mesh was used for the basket in lieu of that called for in the test.)
Results of the draindown tests performed on the 27 loose mixes are summarized in Reference (2), and a
summary of the data are shown as boxplots in Figure 4.2. It should be noted (a) that all of the mixes containing
the AR binder had no draindown (0 percent) and (b) that mixes containing the PG 64-28 PM binder had the
highest draindown values. The majority of mixes with the PG 64-10 and PG 64-28 PM binders did not satisfy
the required maximum limit of 0.3 percent draindown. Figure 4.2 also shows that the higher the binder content,
the larger the percent draindown, regardless of the binder and aggregate types.
Asphalt Content:
PG64-10: 5.3%, 6.0%, 6.7%
PG64-28PM: 5.8%, 6.5%, 7.2%Asphalt Rubber: 6.5%, 7.2%, 7.9%
Oven Temperature:
PG64-10: 161C (322F)
PG64-28PM: 181C (358F)
Asphalt Rubber: 185C (365F)
G1 (Coarse)
Loose Mixes
6.5 7.2 7.9 6.5 7.2 7.9 6.5 7.2 7.9
Figure 4.2: Boxplot summary of the draindown test results.
UCPRC-SR-2013-02
As was done for the percent air-void content analyses discussed in Section 4.2, tree-based modeling was
utilized (2). Results of that analysis suggest the following results:
1. For these three aggregates, type did not appear to be significant enough to be included in the
interpretation of the test data.
2. Binder type was the most important factor that categorized the draindown test results. Regardless of
binder content, the average percent draindown was 1.54 percent for mixes containing PG 64-28 PM,
0.69 percent for mixes with PG 64-10, and no draindown (0 percent) for the mixes with AR. With this
G1 grading, mixes with PG 64-28PM had a higher percent draindown than those for the mixes with
PG 64-10 binder.
3. For mixes with PG 64-10 and PG 64-28 PM binders, the higher the binder content, the larger the percent
4. According to the tree-based modeling, and as illustrated in Figure 4.2, only mixes with AR and mixes
with PG 64-10 and a binder content less than 5.65 percent satisfied the maximum 0.3 percent draindown
Using the same statistical analyses as in Section 4.2, it is concluded that use of the tree-based model to interpret
the boxplot summary of percent draindown is acceptable, although not statistically adequate.
Test Results for Cantabro Test
As noted earlier, the Cantabro Abrasion Test is used to evaluate the durability (abrasion resistance) of OGFC
mixes as part of the mix design process. In general, resistance to abrasion improves with an increase in binder
content and/or the use of a stiffer binder. Using Los Angeles Abrasion test equipment, abrasion loss is
determined after 300 gyrations at a speed of 30 to 33 rpm at a room temperature of 7710°F (255.6°C). Loss in
weight, expressed as a percentage, is calculated according to the following:
where: PL is the percent Cantabro loss,
P is the specimen mass prior to test (grams), and
P is the specimen mass after 300 gyrations (grams).
The average percent loss of three specimens is reported as the Cantabro loss (or Cantabro abrasion loss) for
UCPRC-SR-2013-02
Results of the Cantabro tests performed on the 27 loose mixes are tabulated in Reference (2) and a summary of
the data are shown as boxplots in Figure 4.3. From the Cantabro loss data shown in this figure, it is apparent that
Cantabro loss is dependent on binder type. The PG 64-28 PM mixes performed the best, followed by the AR and
PG 64-10 mixes in that order. In general, an increase in binder content resulted in a decrease in Cantabro loss.
However, for this G1 (coarse) gradation and unit weights obtained using 50 gyrations applied in the gyratory
compactor, only two mixes, those with Watsonville aggregate and the PG 64-28 PM at binder contents of
6.5 percent and 7.2 percent, satisfied the maximum 15 percent Cantabro loss criterion. Also, for the same binder
type and comparable binder contents, mix specimens with the Watsonville aggregate performed better than
those containing the other two aggregates.
PG64-10: 5.3%, 6.0%, 6.7%
PG64-28PM: 5.8%, 6.5%, 7.2%
Asphalt Rubber: 6.5%, 7.2%, 7.9%
50 Gyrations
G1 (Coarse)
15% Cantabro Loss
Figure 4.3: Boxplot summary of Cantabro test percent loss results.
UCPRC-SR-2013-02
Tree-based modeling was included to substantiate the observations of the data shown in Figure 4.3. Results from
that analysis (2) can be summarized as follows:
1. Binder type is far more significant than the other two variables. The average percent Cantabro loss was
86.91 percent for PG 64-10 mixes, 39.54 percent for AR mixes, and 22.11 percent for PG 64-28 PM
mixes (it should be noted again that the test specimens were fabricated with 50 gyrations).
2. Aggregate type affects Cantabro loss. The losses were smaller for mixes containing the Watsonville
aggregate than for the mixes containing the Sacramento and San Gabriel aggregates. However the mixes
with the Watsonville aggregate usually had the lowest air-void contents for a given binder type
3. Only the PG 64-28 PM mix with Watsonville aggregate satisfied the maximum 15 percent Cantabro loss
Determination of Optimum Binder Content
Using the NCAT approach and the proposed Caltrans OGFC mix design procedure, design criteria for selecting
the optimum binder content are as follows:
Criteria for Selecting Optimum Binder Content
18 V
2. Cantabro Abrasion Loss (%), 15% max
3. Draindown at production temperature, 0.30% max.
Table 4.1 summarizes Phase II test results regarding the averages of air-void content, draindown, and Cantabro
loss. Mixes that met the specific criteria for selection of the optimum binder content are shaded in the table.
The table shows that 9 of 27 mixes satisfied the criterion for air-void content, 13 mixes satisfied the draindown
criterion, and only 2 out of 27 mixes met the Cantabro loss criterion. None of the 27 mixes satisfied all three
criteria simultaneously. For this test series, some mixes containing the Watsonville aggregate, with adjustments,
might potentially satisfy all three criteria.
The very high Cantabro losses of the mixes used in Phase II may be attributable to the following causes:
1. The G1 (coarse) gradation contains only 7 percent passing the break point sieve and 1 percent fines
(< No. 200 sieve). Thus, the lack of fines may result in a matrix of binder and fines that does not provide
sufficient cohesion to this coarse aggregate structure.
UCPRC-SR-2013-02
2. The use of only 50 gyrations to compact specimens in the Superpave gyratory compactor may not have
provided a sufficient compactive effort to achieve the desired aggregate interlocking.
3. The selected trial binder contents might not have covered a sufficient range of binder contents to permit
section of the optimum value.
It is also possible that the maximum Cantabro loss criterion of 15 percent established by NCAT (and New
Zealand) may be too severe.
Table 4.1: Summary of Determination of Optimum Binder Content
Aggregate
Draindown
Cantabro Loss
Satisfied?
UCPRC-SR-2013-02
Findings of Phase II
The following provides a summary of the key findings of Phase II: Selection of Optimum Binder Content.
1. Although all the covariates are not included in the tree-based modeling (2), residual analyses of the tree-
based models indicate that the parameters utilized in boxplots to categorize the resulting test data were
sufficient for quantitative interpretation of the test data.
2. Table 4.2 summarizes the first and second levels of the most significant covariates in the tree-based
models that affect air-void content, draindown, and Cantabro loss.
Table 4.2: Summary of the First- and Second-Level Covariates (Phase II)
Parameter
First Level
Second Level
Air-void Content
Aggregate 1
binder ac
binder aggregate
Note: 1. The covariate aggregate is not significant enough to be included in the tree-
based model of percent draindown.
3. Aggregate type is the most important factor that affects percent air-void content. The ranking of the
average air-void content based on tree-based modeling is: Sacramento (26.3 percent) > San Gabriel
(23.7 percent) > Watsonville (21.2 percent). Asphalt content, ac, is the next most important factor; in
general, the smaller the asphalt content, the larger the air-void content—as would be expected.
4. Binder type is the most important factor that categorizes the draindown test results. Based on the tree-
based modeling, the ranking of the average percent draindown is: PG 64-28 PM (1.54 percent) >
PG 64-10 (0.69 percent) > AR (0 percent). Also, as would be expected, the higher the asphalt content,
the larger the percent draindown.
5. Based on the tree-based modeling, binder type is far more significant for Cantabro loss than the other
covariates. The average Cantabro losses were: PG 64-10 mix (86.9 percent), AR mix (39.5 percent), and
PG 64-28 PM mix (22.1 percent). Also, relative to the binders used in this study, Cantabro losses for the
Watsonville aggregate mixes were smaller than those for mixes with the Sacramento and San Gabriel
UCPRC-SR-2013-02
5 PHASE III: SUPPLEMENTAL TESTS
Findings from Phase I and Phase II
Results of the investigations from the first two phases suggest the following:
1. In general, for the mixes tested, the coarser the gradation, the larger the air-void content. Higher air-void
contents are also associated with larger values of VCA
. For the three aggregates investigated,
measured VCA
depends primarily on aggregate type rather than on aggregate gradation.
2. Although the coarse aggregate gradations produce compacted mixes that satisfy the air-void
requirements, this does not guarantee that an OGFC mix will meet the other performance-related test
specifications. A lack of fines (defined by either the percent passing the No. 200 sieve or by the percent
passing the break point sieve) might contribute to this result.
3. Regardless of the three aggregate and three binder types investigated, the high Cantabro loss results
obtained in the Phase II study may be due to the following:
a. Compaction of the test specimens in the SGC using 50 gyrations did not provide a compactive
effort sufficient to retain the integrity of the specimens associated with the aggregate
interlocking that occurs in the field.
b. The G1 (coarse) gradation used in the study accommodates only 7 percent passing the No. 8
break point sieve and 1 percent of fines passing the No. 200 sieve.
c. The selected range of trial binder contents—in increments of 0.7 percent (TV, TV±0.7 percent),
with target values determined from CT 368 and AASHTO T 305—does not necessarily include
the optimum binder content, according to the results obtained in this study.
d. The NCAT mix design procedure's limit of a 15 percent maximum for Cantabro loss may be
too strict (too low) for OGFC mixes.
4. Increasing the binder content helps to reduce Cantabro loss but increases mix draindown. The Cantabro
loss criterion thus establishes the lower bound and the draindown criterion the upper bound for suitable
binder contents.
Test Plan of Phase III and Specimen Preparation
Based on the findings from Phases I and II, supplemental tests were conducted in Phase III using two mixes
selected from the earlier studies. The purpose of this investigation was to provide a preliminary evaluation of the
effects of gyratory compactive effort (number of gyrations), aggregate gradation, and specimen conditioning on
the performance testing and specifications for OGFC mix design. This phase of the study also investigated the
effect of gradation type on Cantabro loss by using a variety of previously untested additional specimens that had
been fabricated for Phase I.
UCPRC-SR-2013-02
These two mixes were selected for Phase III:
1. Mix with PG 64-28 PM binder, Watsonville aggregate ( VCA
= 36.9 percent), and G2 (fine)
gradation; three binder contents (5, 6, and 7 percent): designated PG64-28PM Watsonville G2.
2. Mix with AR binder, Sacramento aggregate (VCA
= 39.4 percent), and G1 (coarse) gradation; three
binder contents (6.5, 7.2, and 7.9 percent): designated AR Sacramento G1.
Since the theoretical maximum density ( G ) values were already available from the Phase II testing, the same
binder contents were used for the G1 mix with Sacramento aggregate and the AR binder. Specimens were
prepared using the SGC compactor at two compactive efforts, 50 and 100 gyrations. Specimens were prepared at
two sizes: 4 in. (102 mm) diameter for volumetric properties and Cantabro tests; and 5.91 in. (150 mm) diameter
for Hamburg Wheel-Track Device testing. They were also prepared for two conditions: dry, as compacted, and
wet, conditioned by Moisture Induced Sensitivity Test (MiST). Table 5.1 summarizes the test plan of Phase III.
All test data are summarized in Reference (2).
Table 5.1: Summary of Test Plan for Phase III
Compaction
Specimen
Test Type
2 gyrations: 50, 100
D3 x 2.5-inch H4 27
Asphalt rubber (AR)
2 conditions: Dry, Wet
4-inch D x 2.5-inch H
2 gyrations: 50, 100
1 condition: Dry
2 gyrations: 50, 100
4-inch D x 2.5-inch H
2 Conditions: Dry,
4-inch D x 2.5-inch H
2 gyrations: 50, 100
5.9-inch D x 2.5-inch H
1 condition: Dry
three aggregates
Watsonville, San
Gabriel), three binders
PG 64-28 PM: 6.5%
4-inch D x 2.5-inch H
1 condition: Dry
PG 64-28 PM, asphalt
rubber [AR]), and
three gradations
1. VCAMIX: voids in coarse aggregate of the compacted mixture; Gmb: bulk specific gravity of the compacted mixture; Gmm: the theoretical
maximum density of the mixture; HWTD: Hamburg Wheel-Tracking Device Test; SGC: Superpave gyratory compaction.
2. The specimens prepared for VCAMIX and Gmb were used for Cantabro tests. 3. Available SGC compaction molds with internal diameters: 4 in. (102 mm) and 150 mm (5.9 inch). 4. The specimen height for the Phase III test plan is 2.5 in. (63.5 mm).
UCPRC-SR-2013-02
Test Results and Analyses
Comparison of Percent Air-Void Content
Figure 5.1 compares the air-void contents for the PG64-28PM Watsonville G2 mixes to the AR Sacramento G1
mixes in a boxplot summary showing the air-void contents of the specimens before they were conditioned by the
MiST machine or subjected to Cantabro testing. Because of a number of unfortunate circumstances, no
specimens were compacted at 50 gyrations for the AR Sacramento G1 mix.
5.1 reveals a large difference (roughly 11.0
percent) between the air-void contents of the
AR Sacramento G1 mix (averaging 23.5 percent) and the PG64-28PM Watsonville G2 mix (averaging
12.5 percent); this difference can be attributed to the fine gradation of the latter mix. (More detailed data are
included in Reference [2]). As noted earlier, the VCA
value is 39.4 percent for the Sacramento aggregate and
36.9 percent for the Watsonville aggregate, and the percent passing the break point sieve is 7 percent for G1
(coarse) gradation and 18 percent for G2 (fine) gradation. From the perspective of volumetric design, a mix with
a larger VCA
value, a smaller percent passing the break point sieve, and lower asphalt content will have
increased air-void content. For these two mixes, the effects of asphalt content and VCA
have only small
differences. By this logic, the 11 percent difference in average air-void content between these two mixes is
primarily the result of the difference in percent passing the break point sieve, i.e., gradation type. This strongly
suggests that the air-void content of an OGFC mix is largely influenced by the selection of the aggregate
UCPRC-SR-2013-02
Asphalt Content:
PG64-28PM: 5.0%, 6.0%, 7.0%
Asphalt Rubber: 6.5%, 7.2%, 7.9%
PG64-28PM Watsonville G2
Asphalt Rubber Sacramento G1
Figure 5.1: Comparison of air-void contents for the PG64-28PM Watsonville G2 and AR Sacramento G1 mixes
(Phase III).
Draindown Test Results and Analysis
Figure 5.2 compares the draindown test results for the PG 64-28 PM mixes with Watsonville aggregate from the
tests in Phase II and Phase III. As the figure shows, aggregate gradation has a significant influence on the
amount of draindown. To prevent draindown during transportation of the mix from the plant to the construction
site, the highest allowable asphalt content for the G2 (fine) gradation was roughly 1.5 percent higher than that of
the G1 (coarse) gradation based on the maximum 0.3 percent draindown criterion. From the viewpoint of
conducting mix durability testing, the greater the asphalt content, the lower the Cantabro loss; in other words,
mix durability certainly benefits from the use of fine gradations.
UCPRC-SR-2013-02
PG 64-28 PM
G1 (Coarse) Phase II
G2 (Fine) Phase III
A phalt Content (%)
Figure 5.2: Comparison of percent draindown between coarse (Phases II) and fine (Phase III) gradations of
PG 64-28 PM mixes containing Watsonville aggregate.
Cantabro Test Results and Analysis of Phase III
In Phase III, the Cantabro test was used to evaluate not only the effects of gradation, binder, and aggregate type,
but also the effect of conditioning on mix durability performance. Before the Cantabro testing, the "wet"
specimens were conditioned using the MiST machine with test parameters set as follows: 3,000 loading cycles,
40 psi (276 kPa) peak pressure, and 50°C (122°F) water temperature. The MiST machine simulates the pore
water pressure built-up due to repeated trafficking during rain.
The Cantabro test data are summarized in Figure 5.3 as boxplots for the AR Sacramento G1 and
PG64-28PM Watsonville G2 mixes. Key findings based on the figure are as follows:
1. All of the AR Sacramento G1 mixes failed to meet the Cantabro test criterion of sustaining a maximum
loss of 15 percent or less, while most of the PG64-28PM Watsonville G2 mixes passed. It seems that the
effect of gradation, i.e., fines content, is a primary factor in passing or failing the Cantabro test.
2. The PG64-28PM Watsonville G2 mixes prepared using 100 gyrations performed slightly better than
those specimens fabricated using 50 gyrations. However, for the AR Sacramento G1 mixes, the 100-
gyration specimens performed worse than 50-gyration specimens. Crushed aggregates were observed
during compaction of the AR Sacramento G1 mix with the 100-gyration compactive effort. Thus, it is
possible that the greater Cantabro loss may be due to disintegration of those aggregates. (This suggests
UCPRC-SR-2013-02
that the 50-gyration compaction effort applied to the G1 mixes in the earlier testing may not have been
the primary reason those mixes did not pass the Cantabro test.)
3. No effect of MiST conditioning was observed on Cantabro loss for the PG64-28PM Watsonville G2 and
AR Sacramento G1 mixes, probably due to the large amount of void spaces in the compacted mix.
Those voids can quickly dissipate built-up pore water pressure and mitigate or prevent damage.
4. For the AR Sacramento G1 mixes, it is apparent that regardless of gyration number and conditioning
method, the common rule of Cantabro testing—the larger the binder content, the smaller the Cantabro
loss—remains unchanged. However, for the PG64-28PM Watsonville G2 mix, the trend was not as
noticeable as it was for the AR Sacramento G1 mix, likely due to the improvement in durability due to
the fine gradation.
PG64-28PM: 5.0%, 6.0%, 7.0%
Asphalt Rubber: 6.5%, 7.2%, 7.9%
15% Cantabro Loss
PG64-28PM Watsonville G2
Asphalt Rubber Sacramento G1
Figure 5.3: Boxplot summary of percent Cantabro loss (Phase III).
UCPRC-SR-2013-02
Cantabro Test Results and Analysis Using Phase I Specimens
Figure 5.4 provides a summary of Cantabro test results for the mixes used for the Phase I study. The detailed test
results are summarized in Reference (2). Overall, the ranking of Cantabro loss (from low to high) in terms of
binder type is PG 64-28 PM < AR < PG 64-10. Within each binder type, the G2 (fine) gradation generally had
the lowest percent Cantabro loss. The figure also shows the effect of aggregate type on Cantabro performance
with respect to gradation. For instance, the Watsonville aggregate had the lowest percent Cantabro loss in G1
(coarse) and G2 (fine), whereas San Gabriel performed the best in G3 (middle). In this test series, the mixes with
the Sacramento aggregate exhibited the highest Cantabro losses with one exception, the mix with the fine
gradation (G2) and PG 64-28 PM binder.
Asphalt Rubber: 7.2%
15% Cantabro Loss
Figure 5.4: Boxplot summary of percent Cantabro loss using Phase I specimens.
Photographs of the test specimens at end of the Cantabro tests are shown in in Figure 5.5 categorized by binder
type, aggregate source, and gradation type. Overall, mixes with Watsonville and San Gabriel aggregates had
smaller Cantabro losses compared to the mixes with Sacramento aggregate. Mixes with Watsonville aggregate
performed slightly better in some instances than mixes with San Gabriel aggregate. Mixes with PG 64-10 binder
had higher Cantabro losses than mixes with either PG 64-28 PM or AR binder; some specimens with PG-64-10
binder had losses as high as 100 percent.
UCPRC-SR-2013-02





Figure 5.5: Photographic summary of Cantabro tests using Phase I SGC specimens (50 gyrations).
HWTD Test Results and Analysis
Hamburg Wheel-Track Device (HWTD) testing conducted in this study followed AASHTO T 324, Standard
Method of Test for Hamburg Wheel-Track Testing of Compacted Hot Mix Asphalt (HMA). The test plan for
HWTD is in Table 5.1. One set of HWTD tests was conducted for each mix type and gyration number. Each set
included two runs (left and right) of HWTD tests. Each run was conducted with two 5.91 in. (150 mm) diameter
gyratory-compacted specimens. The evolution of rutting in the HWTD tests over time (number of passes) and
space (profile position) domains were developed using rutting evolution image-and-contour plots. Hence, two
rut evolution curves were developed per mix type per gyration number. The development of these curves is
described in detail in Reference (2). The resulting data are shown in Figure 5.6 and Figure 5.7 for the two mixes.
UCPRC-SR-2013-02
50 Gyrations (Lt.)
50 Gyrations (Rt.)
100 Gyrations (Lt.)
100 Gyrations (Rt.)
Rut Depth (m -14
Number of Passes
Figure 5.6: HWTD test results for the AR Sacramento G1 mixes.
PG 64-28 PM
50 Gyrations (Lt.)
Rut Depth (mm) -14
50 Gyrations (Rt.)
100 Gyrations (Lt.)
100 Gyrations (Rt.)
Number of Passes
Figure 5.7: HWTD test results for the PG64-28PM Watsonville G2 mixes.
UCPRC-SR-2013-02
Average rut depths at 10,000 passes and 20,000 passes are used as the performance parameters in the following
analyses. In addition, the rut index defined by the following equation provides another performance parameter.
Rut _ Index
20 000 rut @
where, rut @
stands for the absolute value of the average rut depth (mm) at 20,000 passes.
The rut index represents the average loading passes required to reach a 1 mm rut depth during the loading period
from 10,000 to 20,000 passes. The higher the value of the rut index, the better the rutting-resistance capacity of
the mix in the presence of water.
Table 5.2 summarizes the HWTD test results for Phase III including the specimen air-void contents, average rut
depths at 10,000 and 20,000 passes, rut index, and the number of passes to failure (n ). The number of passes to
failure is determined by a three-stage Weibull approach and described in Reference (2). Based on the data
summarized in Figure 5.6 and Figure 5.7, key findings are as follows:
1. The PG64-28PM Watsonville G2 mix performed better than the AR Sacramento G1 mix at the densities
resulting from both the 50- and 100-gyration compactive efforts.
2. The HWTD test results for mix AR Sacramento G1 are consistent in the 50-gyration tests but quite
different for the 100-gyration tests. However, during preparation of the 100-gyration specimens, crushed
aggregates were observed and their disintegration may have caused more rutting. Conversely, the test
results for PG 64-28PM Watsonville G2 mixes are similar for the 100-gyration tests but rather different
for the 50-gyration tests. This may suggest that for mix PG 64-28PM Watsonville G2, the compactive
effort of 100 gyrations provided more aggregate interlocking than 50 gyrations.
3. Preliminary HWTD test results for the same mix show that the 100-gyration specimens performed much
better than the 50-gyration specimens. Thus, the gyrations applied in Superpave gyratory compaction
have an apparent effect on HWTD rutting regardless of mix type. This raises an immediate question:
What gyration number should be specified in an OGFC mix design to appropriately judge the mix
performance through various performance tests?
UCPRC-SR-2013-02
Table 5.2: Summary of HWTD Test Results (Phase III)
Average Rut Depth
Number of
Specimen
Diameter
Rut Index
Passes to
Location
2A-P3-PM-WG2-50-C2 59.93 149.63 14.5
2A-P3-PM-WG2-50-C4 58.16 149.36 11.7
2A-P3-PM-WG2-50-C1 59.17 149.56 13.3
2A-P3-PM-WG2-50-C3 59.23 149.32 13.3
2A-P3-PM-WG2-100-C2 57.84 149.46 11.5
2A-P3-PM-WG2-100-C3 57.86 149.58 11.5
2A-P3-PM-WG2-100-C1 57.67 149.50 11.1
2A-P3-PM-WG2-100-C4 60.02 149.78 14.9
2A-P3-AR-TG1-50-C2 67.68 150.50 26.0
2A-P3-AR-TG1-50-C4 67.67 150.49 26.2
2A-P3-AR-TG1-50-C1 67.70 151.13 27.0
2A-P3-AR-TG1-50-C3 67.60 151.23 26.7
2A-P3-AR-TG1-100-C2 66.11 150.23 24.3
2A-P3-AR-TG1-100-C3 66.49 150.09 24.1
2A-P3-AR-TG1-100-C1 66.43 150.57 24.8
2A-P3-AR-TG1-100-C4 66.88 150.18 24.8
UCPRC-SR-2013-02
Surface Area Versus Equivalent Asphalt Film Thickness Versus Cantabro Loss
Calculations of Surface Area and Equivalent Asphalt Film Thickness
In the Caltrans mix design procedure, estimates of surface area for aggregate gradations are used to determine
the percent of asphalt (aggregate basis) for a starting point in mix design. The percentage of asphalt, P , is
P SA t
SA is the surface area ( mm2 / g ),
t is the equivalent asphalt film thickness ( mm ), and
is the unit weight of asphalt (
g / mm ).
The surface area is significant because it affects the amount of asphalt needed to coat the aggregate. One of the
reasons to estimate the surface area for any given asphalt content is to determine the equivalent asphalt film
thickness that can provide a measure of the durability of a mix. Although the equivalent asphalt film thickness is
an estimated value, it allows systematic comparisons to be made for mixes with various gradations.
For this study, surface area was calculated using a simulation program developed that included two assumptions:
1. That the aggregate is converted to a spherical equivalent with the same weight. The spherical
aggregates retained between two adjacent sieves are generated based on a uniform distribution under the
assumption that the total weight of simulated aggregates is equivalent to the retained weight of an
aggregate batching. Thus, the surface area per kilogram of aggregate blend can then be determined for
each sieve size.
2. That the fines that pass the No. 200 sieve together with asphalt will form an asphalt mastic that will coat
the aggregates larger than those that pass the No. 200 sieve. Accordingly, the asphalt film thickness is
defined as the division of the volume of mastic, which is the sum of the volume of fines (< No. 200
sieve) and volume of asphalt, by the cumulative surface area for aggregates retained above the No. 200
The detailed surface area simulations of gradations G1, G2, and G3 are included in Reference (2). Table 5.3
provides a summary of the asphalt film thickness calculation based on the cumulative surface areas obtained
from 1,000 g of aggregate blend. The ranking of the calculated film thicknesses is G1 (coarse) (127 μm) >
G3 (middle) (91 μm) > G2 (fine) (60 μm), whereas the ranking of cumulative surface area is reversed as
G1 (0.5 m2/kg) < G3 (0.7 m2/kg) < G2 (1.2 m2/kg).
Figure 5.8 plots cumulative surface area versus sieve size for gradations G1 (coarse), G2 (fine), and G3 (middle)
in a logarithm-logarithm scale. It is interesting to note that the curves deviate starting at the No. 30 sieve and the
cumulative surface area rapidly diverges thereafter. As expected, the ranking of the surface area accumulation
rate is G2 (fine) > G3 (middle) > G1 (coarse).
UCPRC-SR-2013-02
Table 5.3: Summary of Asphalt Film Thickness Calculation Based on the Cumulative Surface Areas
Obtained from 1,000 g of Aggregate Blend
Equivalent
Cumulative
Volume of
% Passing
Volume of
Surface Area
No.200/AC
Aggregate
(above No. 200)
(< No. 200)
Thickness
(mm2/kg)
6 0.500000 11,111.110 60,000 71,111.110 1,177,713
ace Area (
rf
lative Su
Cum 1E+03
Sieve Size (mm)
Figure 5.8: Cumulative surface area versus sieve size for various gradation types.
The same calculation procedures for surface area and equivalent asphalt film thickness were applied to the
specimens prepared for all three phases (included in Reference [2]). Bulk specific gravities used in the surface
area calculation for both the coarse and fine aggregates are 2.66 for Sacramento and Watsonville, and 2.60 for
the San Gabriel aggregates. The bulk specific gravities used for the binders are 1.03 for the PG 64-10, and 1.01
for both the PG 64-28 PM and AR. Gradations for the simulations are those listed in Table 2.1. A 1,000 gram
aggregate blend was used to conduct the simulations. Table 5.4 summarizes the simulation results for the mixes
used in Phase I, Phase II, and Phase III; additionally, this table also shows the average Cantabro losses for
specimens prepared using 50 gyrations.
UCPRC-SR-2013-02
Table 5.4: Summary of Calculations of Surface Area and Equivalent Asphalt Film Thickness
Cumulative
Equivalent
Cantabro
Volume of
Surface Area
Aggregate
Volume of
No. 200/AC
Aggregate
(< No. 200)
Thickness
Gyrations
(mm2/kg)
3,759.4 58,252.4
62,011.8 509,953 0.122 100.00
3,759.4 58,252.4 62,011.8 508,000 0.122 94.4
11,278.8 58,252.4
69,530.6 1,194,123 0.058 74.3
11,278.8 58,252.4 69,530.6 1,193,732 0.058 43.8
7,518.8 58,252.4
65,771.2 754,972 0.087 99.7
7,518.8 58,252.4 65,771.2 755,509 0.087 89.3
3,759.4 64,356.4
68,115.8 508,984 0.134 68.2
3,759.4 64,356.4 68,115.8 509,183 0.134 23.6
11,278.2 64,356.4
75,634.6 1,193,381 0.063 11.4
11,278.2 64,356.4 75,634.6 1,193,672 0.063 20.5
7,518.8 64,356.4
71,875.2 755,283 0.095 50.4
7,518.8 64,356.4 71,875.2 754,872 0.095 34.4
3,759.4 71,287.1
75,046.5 510,891 0.147 71.3
3,759.4 71,287.1 75,046.5 509,753 0.147 35.0
11,278.2 71,287.1
82,565.3 1,194,504 0.069 44.7
11,278.2 71,287.1 82,565.3 1,192,033 0.069 25.2
7,518.8 71,287.1
78,805.9 756,434 0.104 62.7
7,518.8 71,287.1 78,805.9 755,517 0.104 63.2
UCPRC-SR-2013-02
Table 5.4 Summary of Calculations of Surface Area and Equivalent Asphalt Film Thickness (cont.)
Cumulative
Equivalent
Cantabro
Volume of
Surface Area
Volume of
Aggregate
No. 200/AC
Aggregate
(< No. 200)
Thickness
Gyrations
(mm2/kg)
3,759.4 51,456.3
55,215.7 508,903 0.1090 100.00
Sacramento G1 6.0 1
3,759.4 58,252.4
62,011.8 510,286
3,759.4 65,048.5
68,807.9 510,769
3,759.4 51,456.3
55,215.7 509,510
Watsonville G1 6.0 1
3,759.4 58,252.4
62,011.8 509,669
3,759.4 65,048.5
68,807.9 511,415
3,846.2 51,456.3
55,302.5 521,177
3,846.2 58,252.4
62,098.6 525,060
3,846.2 65,048.5
68,894.7 520,934
3,759.4 57,425.7
61,185.1 511,506
Sacramento G1 6.5 1
3,759.4 64,356.4
68,115.8 511,021
3,759.4 71,287.1
75,046.5 508,228
3,759.4 57,425.7
61,185.1 510,172
Watsonville G1 6.5 1
3,759.4 64,356.4
68,115.8 508,519
3,759.4 71,287.1
75,046.5 509,496
3,846.2 57,425.7
61,271.9 521,593
3,846.2 64,356.4
68,202.6 522,811
3,846.2 71,287.1
75,133.3 521,989
3,759.4 64,356.46
68,115.8 509,924
Sacramento G1 7.2 1
3,759.4 71,287.7
75,046.5 511,048
3,759.4 78,217.8
81,977.2 510,398
3,759.4 64,356.4
68,115.8 510,805
Watsonville G1 7.2 1
3,759.4 71,287.7
75,046.5 510,555
3,759.4 78,217.8
81,977.2 507,130
3,846.2 64,356.4
68,202.6 521,088
3,846.2 71,287.1
75,133.3 522,715
3,846.2 78,217.8
82,064.0 518,304
3,759.4 64,356.4
68,115.8 510,349
Sacramento G1 7.2 1
3,759.4 71,287.1
75,046.5 509,798
3,759.4 78,217.8
81,977.2 510,398
11,278.2 49,505.0
60,783.1 1,192,725 0.051
11,278.2 59,405.9
70,684.1 1,192,993 0.059
11,278.2 69,306.9
80,585.1 1,193,310 0.068
UCPRC-SR-2013-02
Correlation of Cantabro Loss and Mix Properties
The purpose of the calculations of surface area and equivalent asphalt film thickness was to find the correlations
between Cantabro loss and mix properties, especially for the properties of fine aggregates. The average
Cantabro test data used for the analysis together with the surface area calculation data are included in Table 5.4.
The parameters considered in the correlation analysis are as follows:
Binder: PG 64-10, AR, and PG 64-28 PM
Grading: G1 (coarse), G2 (fine), and G3 (middle)
Pfg: percent passing break point sieve, G1 (7 percent), G2 (18 percent), and G3 (12 percent)
Aggregate: Sacramento, Watsonville, and San Gabriel
No. 200/AC: the ratio of percent passing at the No. 200 sieve to percent asphalt content (by weight of
Mastic: the mastic volume (mm3) under the assumption that the fines passing the No. 200 sieve together
with asphalt form the asphalt mastic that coats the aggregates larger than the No. 200 sieve
SA: cumulative surface area (mm2/kg) for aggregates retained above the No. 200 sieve
EAFT: an acronym of Equivalent Asphalt Film Thickness (mm), which is defined as the division of
Mastic by SA
CL50: percent Cantabro loss for specimens fabricated with 50 gyrations of SGC compaction.
Note that the parameter of average Cantabro loss for specimens prepared using 100 gyrations has been excluded
because (1) there were not enough data to provide valid conclusions, and (2) crushed aggregates were observed
in the AR Sacramento G1 mix during specimen preparation with 100 gyrations, which might induce higher
Cantabro loss than in the specimens prepared using 50 gyrations. Table 5.5 summarizes the correlations matrix
among parameters.
Table 5.5: Correlations of Mix Properties and Cantabro Loss
Aggregate
No. 200/AC
0.114 0.999 1.000
Aggregate
0.073 0.112 0.114 1.000
No. 200/AC
0.073 0.977 0.977 0.128
0.313 0.321 0.320 -0.006
0.116 0.992 0.996 0.097
0.012 -0.923 -0.921 -0.084
-0.831 -0.213 -0.222 -0.152
-0.238 0.004 1.000
UCPRC-SR-2013-02
It should be noted that Binder, Grading, and Aggregate are category covariates that have to be converted to
numbers before correlations can be calculated. These conversions have been labeled numerically starting with
the number "1" as follows:
Category Covariates
Conversion Number
(When Calculating the
Binder Grading
Aggregate
For example, the correlation, -0.831, between Binder and CL50 indicates: (1) Binder is negatively correlated to
CL50 with a high absolute value of correlation; (2) the higher the conversion number, the lower the Cantabro
loss, or in other words, the PG 64-28 PM has the best Cantabro-loss–resistant capacity among binder types.
The following key findings are taken from the correlation matrix in Table 5.5:
1. By inspecting the parameters associated with the CL50, it was found that the Binder is negatively
correlated to the CL50 with a high correlation of -0.831. This indicates that the selection of binder type
is extremely important for Cantabro performance in OGFC mix design. The Mastic is the next most
important parameter that negatively correlates to CL50 with a correlation of -0.490, implying that the
higher the mastic volume, the lower the Cantabro loss. In other words, the Cantabro performance can be
improved by increasing mastic volume, i.e., using either more asphalt binder or more fines (< No. 200
sieve), or both. As shown earlier in Table 5.4, a fine gradation generally provides larger mastic volume
and surface area.
2. The Aggregate, Grading, and Pfg have very low correlation with CL50 and other parameters.
3. The No. 200/AC is positively correlated to SA with a correlation of 0.971 and negatively correlated to
EAFT with a correlation of -0.957. The higher the ratio of No. 200/AC, the larger the SA; however, the
correlation (-0.159) between No. 200/AC and CL50 is fairly small.
Findings of Phase III
Key findings from the Phase III test results include the following:
1. The percent air-void content of an OGFC mix is highly dominated by the selection of gradation, as
shown conclusively in Figure 5.1.
2. Gradation has a notable effect on draindown performance, as Figure 5.2 shows. The figure also shows
that the highest allowable asphalt content for the fine gradation (G2) is higher than that for the coarse
gradation (G1). From the viewpoint of conducting the Cantabro test for mix durability, the higher the
asphalt content, the lower the Cantabro loss; in other words, mix durability benefits from the use of the
UCPRC-SR-2013-02
3. The boxplot summary (Figure 5.4) and correlation analysis (Table 5.5) agree that binder type is far more
significant than the other factors that affect Cantabro performance. Also, from the correlation analysis,
the Mastic, which is defined as the volume of fines passing the No. 200 sieve together with asphalt, has
a moderate correlation (-0.490) with CL50, which indicates that the higher the mastic volume, the lower
the Cantabro loss. In other words, the Cantabro performance can be improved by increasing mastic
volume, i.e., using either more asphalt binder or more fines (< No. 200 sieve), or both.
4. Increasing the gyration number from 50 to 100 gyrations results in a decrease of measured percent
air-void content, a decrease of Cantabro loss (provided that there are no crushed aggregates during
specimen preparation), and better rutting-resistance capacity in HWTD tests.
UCPRC-SR-2013-02
6 DEVELOPMENT OF OGFC MIX DESIGN CHART
Weight-Volume Relationships
The development of the weight-volume relationships for a compacted asphalt mixture, with consideration of
asphalt absorption by the coarse aggregate and any fibers included in the mix, that are used in this chapter are
contained in Reference (2) and they are based primarily on those contained in Asphalt Paving Mixtures (4) and
The Asphalt Handbook (5). It should be noted, however, that some of the notations and definitions used here and
in (2) are slightly different from those other sources.
The break point sieve size defined in an OGFC gradation separates the aggregate into fractions of fine and
coarse aggregates, as noted earlier. The total weight of an asphalt mixture is the sum of the weights of the
asphalt, fiber, fine aggregate, and coarse aggregate. The total volume is the sum of the volumes of the fiber, the
aggregate, and the asphalt not absorbed by the aggregate, plus the air voids. If the total volume is set as "Unit
Volume," i.e., 1.0, then the total weight is the unit weight of the compacted asphalt mixture. For an OGFC mix,
, voids in coarse aggregate in dry-rodded condition, is equivalent to the total volume minus the
volume of the coarse aggregate. Thus in the OGFC, the VCADRC is filled with the fine aggregate, fiber, and asphalt not absorbed by the aggregate, plus air voids. That is,
V V V V
From the volumetric relationships of asphalt, absorbed asphalt, fiber, and fine aggregate, the VCA
(Equation 6.1) is then expressed as (See Reference [2] for details):
V 1 V
air
cg cg fg
UCPRC-SR-2013-02
V : percent air voids (in decimal form),
P : percent passing the break point sieve (in decimal form),
: percent asphalt content by weight of aggregate (in decimal form),
: voids in coarse aggregate in dry-rodded condition (in decimal form),
: percent absorbed asphalt content by weight of coarse aggregate (in decimal form),
P : percent fiber content by weight of aggregate (in decimal form),
: bulk specific gravity of coarse aggregate,
: bulk specific gravity of fine aggregate,
: specific gravity of asphalt, and
: specific gravity of fiber.
Without fiber, Equation 6.2 becomes
air
P P P
cg cg fg
Sensitivity Study of Weight-Volume Relationship
Equation 6.3 includes three design parameters, V , P , and P , and five material parameters, VCA
, G , and G . Note that P is not included as a design parameter since P P 1.0 . The three design
parameters are the major considerations in OGFC mix design for ensuring that requirements for drainage,
permeability, and durability are satisfied. For a set of given material parameters and any two of the design
parameters, the remaining design parameter can be mathematically determined using Equation 6.3. To evaluate
how a design parameter is affected by the other two design parameters and the material parameters, design plots
and tree-based modeling were developed from the results of 10,000 statistical simulations. The details of tree-
based modeling are summarized in Reference (2). Each simulation used a set of parameter values that were
randomly generated following a uniform distribution in the parameter ranges shown as follows, with the
parameter ranges based on available data and experience:
UCPRC-SR-2013-02
Three design parameters:
V : 10 – 30%
P : 2 – 23%
P : 5 –10% (by weight of aggregate)
Five material parameters:
P : 0 – 5% (by weight of coarse aggregate)
G : 2.50 – 2.95
G : 2.40 – 2.75
G : 1.00 – 1.03
For instance, if V is selected as the response variable, then its value will be determined by two other design
parameters and five material parameters according to Equation 6.3. A total of 10,000 sets of parameter values
were then constructed according to the parameter ranges shown above. Design plots and tree-based modeling
summarized the simulation to determine how the response variables were affected by the design and material
parameters. These results are included in Reference (2).
Conclusions from the sensitivity analysis can be summarized as follows:
1. Table 6.1 summarizes the first and second levels of the most significant covariates that affect the three
design parameters, P , P , and V . The tree-based models indicated these three design parameters—
, P , and V —are mutually and significantly affected by each other.
Table 6.1: Summary of the First- and Second-Level Covariates (Sensitivity Study)
Parameter
pfg, vair
pfg, vair
paasp, vcadrc
vair vair
pasp paasp,
paasp, vcadrc
pasp paasp,
paasp, vcadrc
UCPRC-SR-2013-02
, an aggregate-dependent material parameter, has a moderate effect on the response variables.
3. The effect of asphalt absorbed by coarse aggregate ( P
) on air-void content (V ) cannot be ignored.
4. The bulk specific gravities, G , G , and G , have very minor effects on the response variables.
Construction of OGFC Mix Design Chart
According to Equation 6.3 without consideration of fiber addition,
air
P P P
cg cg fg
the P in this nonlinear equation can be resolved if the values of other parameters are given. Hence, using the
design parameter P as the x-axis and the design parameter V as the y-axis, the calculated P values can
form a family of contour lines. Figure 6.1 illustrates the OGFC mix design chart for the Sacramento aggregate
= 1.0 percent that is mapped with the theoretical and measured data from Phase I. In the figure,
theoretical data is shown with solid diamond shapes for PG 64-10, solid squares for PG 64-28 PM, and solid
circles for AR. The measured data is shown by the empty shapes that correspond to those used for the theoretical
data. The figure also shows the air-void content and gradation criteria. As can be seen, under the assumption of
= 1.0 percent, the measured air voids are roughly 2 to 4 percent higher than the theoretical values. For the
fine gradation, the difference is even more serious. The interval between the two adjacent asphalt contour lines
decreases slightly as the percent asphalt content increases. The difference between the measured and theoretical
values shown points to the need to calibrate the mix design chart.
UCPRC-SR-2013-02
PG 64-10 (AC = 6.0%)
PG 64-28 PM (AC = 6.5%)Asphalt Rubber (AC = 7.2%)
G1 (Coarse)
G3 (Middle)
G2 (Fine)
% Passing Break Point Sieve
Figure 6.1: OGFC mix design chart (Sacramento, P
Calibration of Asphalt Absorption Using Phase I Data
As pointed out in the sensitivity study, the effect of P
on the three design parameters cannot be ignored.
Unfortunately, in this study the tests to determine the asphalt absorption of coarse aggregate (ASTM D4469)
were not conducted because it was not expected that the effect would be as significant as it appears to be. To
inspect the effect of P
on V , an alternative used in this study was to minimize the residual sum of squares
of air-void contents (Equation 6.4) under the assumption that asphalt absorption is a constant function rather
than a function of gradation, since it is assumed to only occur in the coarse aggregate. The results of Phase I
tests were used to calibrate the effect of asphalt absorption.
3 AV AV
i, j ,k
i, j
i1 j1 k 1
where: i is the asphalt type including PG 64-10, PG 64-28 PM, and AR,
j is the gradation type including G1 (coarse), G2 (fine), and G3 (middle),
k is the test replicates,
is the kth measured percent air-void content for the ith asphalt type and the jth gradation
AV is the theoretical percent air-void content for the ith asphalt type and the jth specified
i, j
UCPRC-SR-2013-02
Figure 6.2 and Figure 6.3 illustrate the design charts under the assumptions of P
= 2.0 percent and
= 3.0 percent for the Sacramento aggregate. As can be seen from these figures, the whole family of asphalt
contour lines moves upward due to the increase of P
. In other words, increase of P
results in an increase
of P for the given values of V and P . It should be noted that the locations of the measured air-void
contents remain unchanged, whereas the locations of the theoretical air-void contents will change due to the
change of P
. Therefore, the residual sums of squares of percent air-void content can be determined for the
given values of P
PG 64-10 (AC = 6.0%)
PG 64-28 PM (AC = 6.5%)Asphalt Rubber (AC = 7.2%)
G1 (Coarse)
G3 (Middle)
G2 (Fine)
% Passing Break Point Sieve
Figure 6.2: OGFC mix design chart (Sacramento, P
= 2.0 percent).
UCPRC-SR-2013-02
PG 64-10 (AC = 6.0%)
PG 64-28 PM (AC = 6.5%)Asphalt Rubber (AC = 7.2%)
G1 (Coarse)
G3 (Middle)
G2 (Fine)
% Passing Break Point Sieve
Figure 6.3: OGFC mix design chart (Sacramento, P
= 3.0 percent).
Figure 6.4 plots the residual sum of squares versus P
for different aggregate types, which can be perfectly
represented by a polynomial function with degree two. The nadir of the polynomial curve defines the minimum
residual sum of squares. The most likely percentage asphalt absorption obtained is 2.69 percent for Sacramento,
2.42 percent for Watsonville, and 1.66 percent for San Gabriel. As noted earlier, the percentage asphalt
absorption is by weight of coarse aggregate. Thus, the sensitivity study indicates that the high sensitivity
(1.559) (2) of asphalt absorption to air-void content must be considered in developing the OGFC mix design
chart. Instead of using the criterion of minimum residual sum of squares of air-void content, the asphalt
absorption needs to be measured. The methodology to determine percent asphalt absorption will be included
with the work for a following project, Strategic Plan Element 3.25, titled Improved Methodology for Mix Design
of Open-Graded Friction Courses.
UCPRC-SR-2013-02
y = 67.74x2 - 364.43x + 560.62
y = 73.335x2 - 354.82x + 707.37
Sum of Squares
l Sum of Sq
a 100
Paasp (%)
Paasp (%)
San Gabriel
Squares of Ai
of
y = 66.384x2 - 220.03x + 828.87
Paasp (%)
Figure 6.4: Determination of percent asphalt absorption based on minimum residual sum of squares of percent
air-void content.
Figure 6.5, Figure 6.6, and Figure 6.7 represent the OGFC mix design charts calibrated with P
Sacramento, Watsonville, and San Gabriel aggregates. These figures also illustrate how the VCA
family of asphalt contour lines: an increase in the value of VCA
results in upward movement of the whole
family of asphalt contour lines, that is, increase of VCA
results in the increase of P for the given values of
V and P . Viewed from these figures, for G2 (fine) gradation it seems that all the measured air-void contents
are above the theoretical air-void contents, whereas for the G1 (coarse) gradation all the measured air-void
contents are below the theoretical air-void contents. This suggests that the asphalt absorption of coarse aggregate
may be a function of the percentage passing the break point sieve rather than just a constant; whether or not this
is the case requires further verification. It is unclear why the measured air-void contents of Watsonville and San
Gabriel are so scattered. From the viewpoint of volumetric OGFC mix design, it is extremely important to have
the measured air-void contents as accurate, consistent, and repeatable as possible. The measured air-void
contents of Superpave gyratory specimens prepared using gyration number control seem to vary quite a bit.
Control by height may provide a better method.
UCPRC-SR-2013-02
PG 64-10 (AC = 6.0%)
PG 64-28 PM (AC = 6.5%)Asphalt Rubber (AC = 7.2%)
G1 (Coarse)
G3 (Middle)
G2 (Fine)
% Passing Break Point Sieve
Figure 6.5: OGFC mix design chart calibrated with P
= 2.69 percent (Sacramento, Phase I).
PG 64-10 (AC = 6.0%)
PG 64-28 PM (AC = 6.5%)Asphalt Rubber (AC = 7.2%)
G1 (Coarse)
G3 (Middle)
G2 (Fine)
% Passing Break Point Sieve
Figure 6.6: OGFC mix design chart calibrated with P
= 2.42 percent (Watsonville, Phase I).
UCPRC-SR-2013-02
San Gabriel
PG 64-10 (AC = 6.0%)
PG 64-28 PM (AC = 6.5%)Asphalt Rubber (AC = 7.2%)
G1 (Coarse)
G3 (Middle)
G2 (Fine)
% Passing Break Point Sieve
Figure 6.7: OGFC mix design chart calibrated with P
= 1.66 percent (San Gabriel, Phase I).
Advantages of the OGFC Mix Design Chart and Issues to be Resolved
The proposed OGFC mix design chart has the following advantages over the NCAT approach:
1. In contrast to the NCAT approach, which is based on the bulk specific gravity of the aggregate blend,
the proposed method provides a more rational volumetric approach for determining the initial binder
content required to determine the optimum gradation.
2. The proposed mix design chart takes into consideration the percent asphalt absorption of coarse
aggregate, which is not specified in the NCAT approach.
3. The proposed version provides a more rational selection of three trial binder contents, which also
comply with requirements for percent air-void content, to prepare specimens for performance testing.
Although the benefits of using this OGFC mix design chart were demonstrated, there are still many
improvements that can be made to it. Volumetrically based OGFC mix design cannot identify differences among
various binder types, especially polymer-modified and rubberized asphalts which have to be verified through
performance tests. However, both CT 368 and the NCAT approach suggest that higher binder content should be
used for polymer-modified and rubberized asphalts.
The extent of stone-on-stone contact in a coarse aggregate structure determines how well an OGFC mix design
will succeed. The role of fine aggregate in an OGFC mix design is to maintain the stability of the coarse
aggregate structure. However, it seems that the use of break point sieve size alone to categorize the aggregate
UCPRC-SR-2013-02
blend into a coarse portion ( P ) and a fine portion ( P ) cannot truly reflect the importance of gradation in
OGFC mix performance, especially the fines content (< No. 200 sieve). Test results conducted in Phase III
indicate that the fines content significantly affects the performance test results.
Based on these facts, the following steps would need to be taken to make practical use of this OGFC mix design
First, it must first be better calibrated. Second, the performance test results have to be incorporated into the design chart to determine the
optimum binder content, particularly for polymer-modified and rubberized asphalt binders.
Third, and most important, performance specifications must be established in such a way that in-situ
performance conforms to expectations based on laboratory testing.
Proposed OGFC Mix Design Procedure
Volumetric Design and Performance Testing
Advancing the proposed OGFC mix design procedure would include two primary steps:
1. Initiate volumetric design: This includes deciding on material volumetric properties, constructing the
OGFC mix design chart, and determining the gradation and the trial binder contents.
2. Conduct performance testing: Primary tests include Cantabro, draindown, and Hamburg Wheel-Track
Device (HWTD) testing for three selected binder contents.
Figure 6.8 schematically illustrates the proposed OGFC mix design procedure with the use of a hypothetically
calibrated OGFC mix design chart. The steps required to achieve the OGFC mix design are shown in detail as
Volumetric Design:
Step 1: Determine the volumetric properties that are used in constructing the OGFC mix design chart.
According to Equation 6.3, the volumetric properties required are VCA
, G , G , and G .
The relationship of P
as a function of P has to be determined before the OGFC mix design chart is
Step 2: Construct the OGFC mix design chart based on the volumetric properties obtained from Step 1. Step 3: Select the design gradation so as to meet the air voids requirements. Step 4: Select the three trial binder contents with consideration of binder type, especially polymer-
modified and rubberized asphalts, unless it has been determined that a particular binder should be used.
It is suggested that the trial binder range be expanded as much as possible, e.g., target value (TV),
UCPRC-SR-2013-02
Performance Testing:
Step 5: Conduct Cantabro tests to determine the allowable minimum binder content. Step 6: Conduct draindown tests to discover the allowable maximum binder content. Step 7: Conduct HWTD tests to decide the allowable range of binder content based on the rutting
performance specification.
Step 8: Determine the allowable optimum binder content (OBC).
Step 1: Determ ine Vol
e 4: Select Trial
Step 8 Dete
% Air Void
7: Conduct HWTD
% Air Void
% Passing Break Point Siev
Passing Break Point Siev
Figure 6.8: Proposed OGFC mix design process.
(Note: Arrows indicate maximum, minimum, and allowable binder ranges.)
It should be noted that development of an Excel macro to generate the OGFC mix design chart (steps 1 and 2)
based on input design and material parameters is underway, and it will be delivered with the work for a
subsequent project, Strategic Plan Element 3.25.
This Excel macro has been developed for the selection of three trial binder contents to prepare specimens for
performance testing in the OGFC mix design process. For predetermined material properties of the selected
aggregate and binder types, the macro provides an improved method for evaluating whether a selected gradation
UCPRC-SR-2013-02
meets the requisite properties. The macro also determines whether volumetric requirements are met with binder
sufficient to provide the mix with an asphalt film thickness that will result in adequate durability and rutting
resistance without excessive draindown and moisture damage. The proposed mix design chart takes into
consideration the percent asphalt absorption of the aggregate blend in addition to the VCA
. The design chart
does not differentiate among (1) various binder types, especially polymer-modified and rubberized asphalts,
(2) various fines contents, and (3) various gradations with different nominal maximum aggregate sizes (NMAS)
that form distinct aggregate structures, which have to be verified through performance tests. The Excel macro
also provides a convenient way to summarize test results and to determine the optimum binder range (OBR).
Table 6.2 summarizes the test methods/specifications used in the proposed OGFC mix design process. To
explore the relationship of HWTD performance as a function of binder content, four HWTD tests are suggested
for each binder content, i.e., a total of twenty-four 150 mm diameter cylindrical specimens are required. The
proposed OGFC mix design procedure is also illustrated in Figure 6.9.
Table 6.2: Summary of Test Methods/Specifications Used in OGFC Mix Design Process
Caltrans Test
AASHTO Specifications
AASHTO T 27 AASHTO T 19
Asphalt absorption, P
ASTM D4469 – 11
Volumetric Design
RICE ( G )
ASTM D7064-04 APPENDIX X2
Hamburg Wheel-Track Device
UCPRC-SR-2013-02
(Binder, Aggregat
Change Aggregat
Change Binder Type
OGFC Desi
C Des gn Chart
e tion of Three Tri
Hamburg Wheel Trac
Figure 6.9: Proposed OGFC mix design procedure.
UCPRC-SR-2013-02
Troubleshooting of OGFC Mix Design
If an OGFC mix design cannot produce a mixture with a given set of materials that meets all requirements in
accordance with a calibrated OGFC mix design chart, the following suggestions and remedial actions may
improve mixture properties:
Air Voids. The amount of air voids can be adjusted in several ways by changing (1) the aggregate type,
(2) the percent passing break point sieve ( P ), and (3) asphalt content ( P ). This study indicates that
the aggregate type used in OGFC mix design affects not only the value of VCA
but also the value of
, which demonstrates moderately high sensitivity to air-void content, V . Changes to these two
material parameters cause the whole family of asphalt contour lines to shift; as a consequence, the
theoretical air-void contents are changed for the given values of P and P . Decreasing P will
generally increase the air-void content for a given asphalt content. Finally, for a given P , decreasing
the asphalt content results in an increase of air-void content; however, this is not recommended because
a reduction of asphalt content normally results in higher Cantabro loss.
Cantabro Loss. To reduce Cantabro loss, use higher asphalt content, increase fines content, or select a
stiffer binder type.
. If the VCA
is smaller than the VCA
(for example, as with the PG 64-28 PM mixes with
G2 (fine) gradation and the San Gabriel and Watsonville aggregates in the Phase I test results [2]), then
modify the mix gradation by decreasing the percent passing break point sieve ( P ).
Draindown. A draindown problem can be easily remedied by changing binder type, selecting and
adding a fiber, increasing the dosage of fiber, or using warm mix. Fiber is known to be very effective in
reducing draindown.
Moisture Susceptibility. Lime or liquid anti-strip additives are two regular treatments for mixes that fail
to meet moisture susceptibility requirements.
UCPRC-SR-2013-02
UCPRC-SR-2013-02
7 CONCLUSIONS AND RECOMMENDATIONS
Conclusions
This investigation of OGFC mix design used three aggregate types, three binder types, and three trial gradations
to prepare specimens using Superpave gyratory compactors for volumetric, draindown, Cantabro, and other
performance tests. Based on the analyses of the resulting test data, the following conclusions are offered.
1. NCAT Approach. The NCAT approach to OGFC mix design includes a sequential selection process of
OGFC materials, trial gradations, optimum gradation, and optimum asphalt binder content, and evaluation
of moisture susceptibility using the modified Lottman method in accordance with AASHTO T 283 with one
freeze-thaw cycle. In general terms, the NCAT approach can be considered a reasonable OGFC mix design
process that can be improved by incorporating the following considerations:
The criteria for selecting optimum gradation based on the materials and procedures used in
the investigation resulted in the selection of a coarse gradation that did not guarantee a
successful OGFC mix design because most of the time the high air-void contents resulting
from that choice were accompanied by a lack of the fine aggregates that are believed to
improve mix durability.
The 50 gyrations used to compact specimens for testing may not provide enough
compaction effort to produce aggregate interlocking, which appears to result in particularly
high material losses in the Cantabro test for mechanical durability, which is related to
The moisture susceptibility testing in accordance with AASHTO T 283 has been shown to
produce highly variable test results (7); the Hamburg Wheel-Track Device (HWTD) test
would appear to be a better candidate for evaluating moisture susceptibility based on this
2. OGFC Mix Design Chart. Equation 6.3 and the sensitivity study indicate that the three design parameters,
, P , and V , are significantly affected by one another. Hence, the OGFC mix design chart is
constructed as a family of asphalt contour lines plotted for given values of P and V . The two most
important material parameters that affect the OGFC mix design chart are VCA
move the whole family of asphalt contour lines upward; in other words, an increase of
results in an increase of P for the given values of V and P . With a fully calibrated
OGFC mix design chart, the design chart provides a more rational volumetric approach to determining the
initial binder content; the fully calibrated chart takes into consideration the P
and allows for direct
selection of three trial binder contents to prepare specimens for performance tests.
UCPRC-SR-2013-02
3. Balanced OGFC Mix Design. It can be seen in the OGFC mix design chart that selection of a coarse
gradation (i.e., a small percentage passing the break point sieve) will allow more asphalt to be used in the
OGFC mix design. This may indicate a decrease of Cantabro loss and an increased risk that draindown and
premature rutting might occur. Conversely, when a fine gradation (i.e., large percentage passing the break
point sieve) is chosen, the OGFC mix requires less asphalt to meet the air-void criteria. As a consequence,
the draindown performance of the OGFC mix is most likely to benefit from the decrease of asphalt.
However, decreasing the asphalt content is not beneficial to mix performance with respect to durability and
possible rutting. From the test results of Phase III, the use of aggregate gradations with higher fines content
tends to reduce Cantabro loss. From this investigation, the primary weakness of the NCAT approach appears
to be the selection of optimum gradation. With the materials used in this study, regardless of aggregate and
binder types, the selection process always led to selection of a coarse gradation, which does not necessarily
guarantee the success of an OGFC mix design. In short, a balanced OGFC mix design has to consider all
these elements to meet not only the requirements of mix volumetric properties but also the criteria of mix
4. Air-Void Content. In the study of asphalt absorption using Phase I data, the ranking of residual sum of
squares at optimum percentage asphalt absorption was Sacramento (70.48) < Watsonville (278.18)
< San Gabriel (646.50), which corresponds to the ranking of sample standard deviation of air-void contents,
Sacramento (1.65 percent) < Watsonville (3.27 percent) < San Gabriel (4.99 percent). It seems that variation
in air-void content between specimens is aggregate-dependent. The specification of specimen compaction in
terms of number of gyrations likely contributed to the considerable variation in air-void content among
different aggregate types. (Recommendations are presented in Section 7.2.)
5. Asphalt Absorption. The sensitivity study indicated a high sensitivity of V versus P
asphalt absorption only occurs in the coarse aggregate fraction and absorbed asphalt is a constant regardless
of percent passing the break point sieve. The development of the OGFC mix design chart calibrated with
computed asphalt absorptions using Phase I data indicated that asphalt absorption appears to be a function of
the percentage passing the break point sieve ( P ), and that the higher the P , the larger the P
6. Draindown and Cantabro Tests: NCAT identified the reduction of mix temperature during construction to
prevent draindown problems as the primary cause of the development of raveling and delamination when
OGFC mixes with unmodified asphalt binders were used in the 1970s and 1980s. However, this current
study indicates that a mix that satisfies a draindown requirement might not necessarily meet a Cantabro
requirement. Today, it is easier to solve a draindown problem by changing the asphalt type (to a polymer-
modified, rubberized, or stiffer PG grade) or by using fibers or warm-mix additives. The durability property
characterized by the Cantabro test plays a more critical role in OGFC mix design than does the draindown
UCPRC-SR-2013-02
test because it is easier to fix a draindown problem by adding fiber rather than by changing the mix design
when a mix fails the Cantabro test. Hence, as illustrated in Figure 6.9, a higher priority should be given to
the Cantabro test in a hierarchy structure of OGFC mix design.
Based on the results of this study, the following preliminary recommendations are provided for consideration in
future efforts to develop a rational OGFC mix design:
1. Superpave Gyratory Compaction. The use of 50 gyrations with the Superpave Gyratory Compactor (SGC),
recommended by NCAT and utilized in this study for specimen preparation, does not seem to provide
enough compactive effort to achieve the aggregate interlock that is normally achieved in the field. The test
results of Phase III indicate that an increase of the number of gyrations generally benefits OGFC
performance, with less Cantabro loss and greater rutting life, as shown in the HWTD test. However, the
crushed aggregates that were observed during gyratory specimen preparation of the AR Sacramento G1
mixes with 100 gyrations may have contributed to greater Cantabro loss due to the disintegration of
aggregates. Hence, a gyration number between 50 and 100, on the order of 70, is recommended. In a
previous study of the compaction of stabilometer specimens using the SGC (6), considerable between- and
within-variations were found in the gyration numbers required to compact specimens to the height of
63.5 mm (2.5 in.) for various HMA mixes. Therefore, it is suggested that OGFC compaction be controlled
by specimen height rather than by number of gyrations.
2. Air Void Specification. Open-graded friction course mixes are primarily designed to have a large number of
void spaces in the compacted mix without any sacrifices to durability over their design life. The open void
structure helps drain water and preserve surface friction, reducing skid and hydroplaning-related accidents,
and thus increasing roadway safety during wet weather. From this perspective, it is not necessary to specify
the upper limit of the air-void content if a compacted mix can meet the performance specifications for
permeability, Cantabro (measure of durability performance), and Hamburg Wheel Tracking Device testing
(HWTD, measure of rutting and moisture sensitivity).
3. Selection of Binder Type. The tree-based modeling and correlation analyses completed in this study
indicated that binder type is the most significant factor affecting the Cantabro performance of an OGFC
mix, and that PG 64-28 PM binder demonstrated superiority over the other two binder types, PG 64-10
and AR. These results are limited to the three binders used in this study but strongly indicate that binder
type and/or grade selection is extremely important to balance draindown and durability.
4. Maximum Cantabro Loss Specification. The Cantabro test results obtained in this study indicate that it will
be difficult for many mixes meet the specification of 15 percent maximum Cantabro loss recommended by
the NCAT approach. It is suggested that the specification of 15 percent maximum Cantabro loss be re-
UCPRC-SR-2013-02
evaluated and coupled with the specification for the value of the dust-to-asphalt ratio (percent passing the
No. 200 [0.075 mm] sieve) and/or fines content (percent passing the No. 200 sieve) to ensure that the
performance specification calibrated with the in-situ data can satisfy the requirements for OGFC design life.
5. Further Study—Calibration of Mix Design Chart. The OGFC mix design chart should be calibrated based
on further laboratory testing ensure that it delivers the desired air-void content while also producing mixes
that meet the desired properties for the three performance-related tests: draindown, Cantabro (measure of
durability performance), and HWTD testing (measure of rutting and moisture sensitivity). The calibration
should be done by performing laboratory testing to determine the effects of the percent passing the No. 200
sieve, the dust-to-asphalt ratio, fibers, binder grade, nominal maximum aggregate size (NMAS), percent
absorbed asphalt in the aggregate, and percent passing the break point sieve size on air-void content, and on
the performance-related test results. Furthermore, an approach should be developed to include the results of
performance-related tests in the design chart to determine the allowable range of binder contents that will
meet all design requirements.
6. Further Study—HWTD Performance Specification. Further study is also required to evaluate the HWTD test
as a performance test for OGFC mix design. There are two questions to be answered in this regard. First,
will the HWTD testing rank the OGFC mixes correctly and consistently both in the laboratory and in the
field, regardless of aggregate type, aggregate size, asphalt type (conventional, polymer-modified, and
rubberized), air-void content, and test temperature? Second, how will the laboratory HWTD test
performance specification relate to field performance? The work to answer the first question should involve
determination of the best Superpave gyratory compaction details, evaluation of the effects of specimen
height and wheel size on HWTD performance, and identification of the best performance parameters to be
obtained from HWTD tests. As for the second question, calibration of the laboratory HWTD test
performance specification to field performance can be achieved using two data sets: field monitoring of
initial implementation projects that include field sampling and laboratory testing and analysis, and available
Heavy Vehicle Simulator and laboratory HWTD test results to develop a correction factor to relate HWTD
rutting to full-scale rutting.
UCPRC-SR-2013-02
8 REFERENCES
1. Mallick, R.B., P.S. Kandhal, L.A. Cooley, and D.E. Watson. Design, Construction, and Performance of
New-Generation Open-Graded Friction Courses, NCAT Report 00-01, National Center for Asphalt
Technology, Auburn, Alabama, April 2000.
2. Tsai, B.-W., J.T. Harvey, and C.L. Monismith. Evaluation of Open-Graded Friction Courses (OGFC) Mix
Design. Research source report UCPRC-RR-2012-09, September 2012.
3. Standard Specifications. State of California, Business, Transportation and Housing Agency, Department of
Transportation, 2010.
4. Monismith, C.L. Asphalt Paving Mixtures: Properties, Design, and Performance. Prepared for the Short
Course in Asphalt Paving Technology, 1961–1962.
5. The Asphalt Institute. The Asphalt Handbook MS-4. 7th edition, 2007.
6. Tsai, B.-W., J.T. Harvey, and C.L. Monismith. Comparison of Gyratory and Kneading Compaction
Methods: Specimen Preparation, Stabilometer Test and Other Performance Tests. Technical Memorandum.
University of California Pavement Research Center, 2012 (in review).
7. Tsai, B.-W., M. Khan, J.T. Harvey, and C.L. Monismith. Evaluation of CT 371 Field Data. Technical
Memorandum UCPRC-TM-2011-03. University of California Pavement Research Center, 49 pp.
UCPRC-SR-2013-02
APPENDIX A
Table A.1: Performance-Graded Asphalt Binder Data, PG 64-10, San Joaquin Refinery
Property
Test Result
Test Method
Original Binder
Flash Point, Minimum °C
Solubility, Minimum %
Viscosity at 135°C, Maximum, Pa·s
Test Temp. at 10 rad/s, °C
Minimum G*/sin(delta), kPa
RTFO Test Aged Binder
RTFO Test: Mass Loss, Maximum, %
Test Temp. at 10 rad/s, °C
Minimum G*/sin(delta), kPa
Ductility at 25°C, Minimum, cm
PAV Aging, Temperature, °C
RTFO Test and PAV Aged Binder
Test Temp. at 10 rad/s, °C
Maximum G*sin(delta), kPa
Test Temperature, °C
Maximum S-value, MPa
Specific Gravity @ 60°F
UCPRC-SR-2013-02
Table A.2: Performance-Graded Asphalt Binder Per Caltrans Specification: PG 64-28 PM,
San Joaquin Refinery
Property
Test Result
Test Method
Original Binder
Flash Point, Minimum °C
Solubility, Minimum %
Viscosity at 135°C, Maximum, Pa·s
Test Temp. at 10 rad/s, °C
Minimum G*/sinδ, kPa
RTFO Test Aged Binder
RTFO Test: Mass Loss, Maximum, %
Test Temp. at 10 rad/s, °C
Minimum G*/sinδ, kPa
Elastic Recovery at 25°C, Minimum Recovery, %
PAV Aging, Temperature, °C
RTFO Test and PAV Aged Binder
Test Temp. at 10 rad/s, °C
Maximum G*sinδ, kPa
Test Temperature, °C
Maximum S-value, MPa
Specific Gravity @ 60°F
UCPRC-SR-2013-02
Table A.3: Asphalt-Rubber Binder Testing Results of Asphalt Rubber (AR) (MACTEC)
UCPRC-SR-2013-02
Table A.4: Aggregate Properties Reported by the Three Suppliers
Test Results
Quality Characteristic/Property
Sacramento
Watsonville
San Gabriel
Crushed particles, coarse aggregate
One fractured face (%) Crushed particles, coarse aggregate
Two fractured faces (%) Crushed particles, fine aggregate (#4x#8)
One fractured face (%) LA Rattler, loss at 100 rev. (%)
LA Rattler, loss at 500 rev. (%)
Sand equivalent (avg.)
Fine aggregate angularity (%)
Flat and elongated particles % by mass @ 3:1
Flat and elongated particles % by mass @ 5:1
Plasticity index
Fine aggregate durability index
Coarse aggregate durability index
c factor (not mandatory until further notice)
Kf factor (not mandatory until further notice)
Bulk specific gravity (oven dry), coarse aggregate
Absorption, coarse aggregate
Bulk specific Gravity (SSD) of fine aggregate
Bulk specific Gravity (oven dry) of fine aggregate
Absorption of fine aggregate
Apparent specific gravity of supplemental fines
Bulk specific gravity of aggregate blend
Specific gravity of fines apparent
UCPRC-SR-2013-02
Source: http://www.ucprc.ucdavis.edu/PDF/UCPRC-SR-2013-02.pdf
R.M. of Baildon No. 131 Zoning Bylaw Rural Municipality of Baildon No. 131 R.M. of Baildon No. 131 Zoning Bylaw R.M. of Baildon No. 131 Zoning Bylaw The Rural Municipality of Baildon No. 131 Bylaw No. A Bylaw of the Rural Municipality of Baildon No. 131 to adopt a Zoning Bylaw. The Council of the Rural Municipality of Baildon, in the Province of Saskatchewan, in open meeting assembled enacts as follows: (1)
REGULATORY LIABILITY OF DIRECTORS AND OFFICERS By Peter Wardle, Helen Daley and Simon Bieber In the current environment, officers and directors of public companies must not only be aware of their potential civil liability, including claims under the Class Proceedings Act, but also that their actions will be scrutinized by securities regulators. The Ontario Securities Commission's