2pk.ir
J Sol-Gel Sci Technol
Mixed matrix vanadium oxide catalytic nanocomposite membranefor styrene oxidation
A. L. Ahmad • B. Koohestani • S. Bhatia •B. S. Ooi
Received: 25 November 2011 / Accepted: 23 March 2012Ó Springer Science+Business Media New York 2013
Mesoporous nanocomposite membranes with
vanadium oxide–carbon nanotubes (VxOy-CNTs) embed-ded in c-Al2O3 were successfully synthesized using the dip
Catalytic membranes were first suggested by Sun in 1987
coating method. The membranes were evaluated for sty-
Thereafter, Burggraaf [] indicated that c-alumina
rene oxidation to determine the optimum styrene conver-
membranes could be modified to become catalytic mem-
sion and benzaldehyde selectivity. Several factors that
branes. Ceramic membranes are technically important for
influence the preparation of defect-free coatings, such as
filtration and separation. They are also important for cat-
the type of binder, the binder addition time and surface
alytic reactions with other types of membranes because
support treatments, were investigated. The physico-chem-
they have unique characteristics, such as chemical stability,
ical permeation properties of the membranes were char-
long lifetimes, good defouling properties and higher
acterized using scanning electron microscope, transmission
operating temperatures in chemical and petrochemical
electron microscope (TEM), X-ray Diffraction XRD,
applications, compared to polymeric membranes
Nitrogen adsorption (BET) and Thermogravimetric TGA.
Inorganic catalytic membranes are manufactured mainly
Response surface methodology (RSM) was used to inves-
from Al2O3, TiO2, ZrO2, SiO2 or mixtures of these com-
tigate the effects of oxidant (H2O2) concentration, tem-
pounds; of these materials, Al2O3 has received the most
perature, contact time and catalyst loading on styrene
research attention [–]. Furthermore, c-Al2O3 has been
conversion and the selectivity of benzaldehyde. Based on
widely studied for the preparation and modification of
the RSM analysis, the optimal oxidation conditions inclu-
catalytic membranes using the Sol–gel method because
ded a reaction temperature of 45 °C, a differential pressure
these types of membranes can be used for oxidation reac-
of 1.5 bars, a molar ratio of H2O2: styrene of 1.5:1 and a
tion purposes , ]. c-Al2O3 membranes are typically
catalyst loading of 30 %. These conditions resulted in the
supported on macro porous a-Al2O3 tubes or disks in the
maximal styrene conversion of 25.6 and 84.9 % benzal-
sol–gel method; they are dip or spin coated with a boehmite
dehyde selectivity.
(AlOOH) precursor to improve conversion or selectivity].
Catalytic membrane Nanocomposite
However, when AlOOH is applied, the surface onto
membrane Vanadium oxide nanocomposite Alumina
which c-Al2O3 is catalytically embedded must be free of
cracks following calcination. Therefore, choosing a suit-able binder that can be burned off in the calcination stepwithout negative side effects on the catalyst or membraneis important. Although catalytic membranes with differentshapes, catalyst loadings and binders have been prepared
A. L. Ahmad (&) B. Koohestani S. Bhatia B. S. Ooi
and tested in commercial ceramic support structures
School of Chemical Engineering, Engineering Campus,
–no studies have investigated the use of vanadium
Universiti Sains Malaysia, Seri Ampangan, Nibong Tebal,
S.P.S., 14300 Penang, Malaysia
xOy) supported on multi-walled carbon nanotubes
(MWCNTs) for styrene oxidation in catalytic membranes.
J Sol-Gel Sci Technol
Due to their large surface area and outstanding thermal,
(PEG) and polyvinyl alcohol (PVA) were obtained from
chemical and mechanical stabilities, carbon nanotubes
Merck Co., Germany, and a-alumina (AA-04) was pur-
(CNTs) are promising for the development of advanced
chased from Sumitomo Chemical Co., Japan.
composite materials that undergo catalytic oxidation reac-tions. As a result of their amazing properties, CNTs havebeen introduced into many host materials, including poly-
2.2 Catalyst and membrane preparation
mers, metals and ceramics, to improve the overall proper-ties of CNT composite systems [
2.2.1 Pretreatment of MWCNTs
The growth of metal oxides on the walls of carbon
nanotubes (CNTs) is a common technique for preparing
Because MWCNTs prepared using the CVD method usu-
composite materials [The use of vanadium oxide nano-
ally contain carbonaceous or metallic impurities, an acid
structures as metal oxide catalysts is of particular impor-
treatment was employed to remove amorphous carbon and
tance because vanadium oxides can be used for the partial
metal-oxide impurities introduced during the process [
oxidation or dehydrogenation of alkanes to olefins [–
Approximately 4 g of raw MWCNTs were pretreated and
Therefore, blends of vanadium oxides and CNTs are
oxidized with 400 ml of a 12 M HNO3 solution in a round
expected to produce novel composite materials with
bottom flask at a reflux temperature of 95 °C for 10 h. Prior
enhanced chemical and physical properties.
to the oxidation process, the flask was placed in an ultra-
Embedding carbon nanotubes and vanadium oxides into
sonic water bath with a frequency of 37 kHz, a power of
150 watt and a temperature of 80 °C for 30 min to modify
2O3 poses several critical challenges that must be
overcome to capture the full potential of CNT composites.
the oxygen-containing groups on the surface of the carbon
The uniform dispersion of CNTs in the host matrix material
nanotubes. The acid-treated MWCNTs were washed with
is essential. As a result of van der Waals forces, CNTs are
deionized water and ethanol to obtain a final solution pH of
likely to form agglomerates or bundles instead of individ-
6-7 and then dried at 130 °C for 24 h.
ual tubes, and this can produce defects in compositemembranes. The second main challenge is associated withstrengthening the interaction between CNTs and the host
2.2.2 Preparation of CNTs-VxOy catalysts
matrix to produce stable composite materials.
The oxidation of olefin compounds to equivalent epox-
The multi-walled carbon nanotubes impregnated with
ides or oxides is an important step in the manufacturing of
vanadium oxide (CNTs-VxOy) catalysts were prepared
large volumes of fine- and pharmaceutical-grade chemicals
using an incipient wetness technique ]. In this tech-
[For example, the oxidation of terminal alkenes, such
nique, a saturated NH4VO3 aqueous solution (100 ml) was
as styrene, is difficult and necessitates longer reaction times
refluxed for 24 h to obtain an orange hydrolysis product.
[Styrene oxide (SO) and benzaldehyde are typically
The suitable amount of HNO3-treated MWCNTs was
manufactured by oxidizing styrene, with stoichiometric
floated in the hydrolysis solution, stirred and refluxed at
amounts of peracid as the oxidizing agent ]. Styrene
100 °C for 12 h. The suspension was then filtered, washed
oxidation in the presence of H
several times with deionized water and ethanol, and dried
2O2 is widely used in the
production of two significant products, SO and benzalde-
at 130 °C overnight. It was then calcified in an N2 atmo-
hyde []. To the best of the authors' knowledge, no
sphere at a heating rate of 3 °C/min for 5 h until a tem-
studies have investigated benzaldehyde production with
perature of 500 °C had been reached. This was followed by
air heating at 250 °C for 3 h.
xOy-CNT as the catalyst and Al2O3-VxOy-CNT as the
catalytic membrane.
2.2.3 Preparation of AlOOH sol (Boehmite sol)
2 Materials and methods
Aluminum tri-sec-butoxide (Al(C3H7O)8) was hydrolyzedin an excess amount of deionized water (H2O:Al3? molar
ratio of 113:1) at 85 °C; the solution was vigorously stirredfor 1 h in an open container until most of the alcohol
MWCNTs, with a purity of C 98 wt%, an average outer
evaporated. This was followed by peptization with dilute
diameter of 60–100 nm and a length of 5–15 lm, were
HNO3 (0.2:1 H?/Al3? mol) to form a stable colloidal sol.
purchased from Shenzhen Nanotech Port Co., China. Nitric
The sol was maintained at 80 °C for 24 h under reflux
acid (HNO3), aluminum tri-sec-butoxide Al(C3H7O)8,
conditions. A boehmite sol, with a pH value of 3.43, was
ammonium metavanadate (NH4VO3), polyethylene glycol
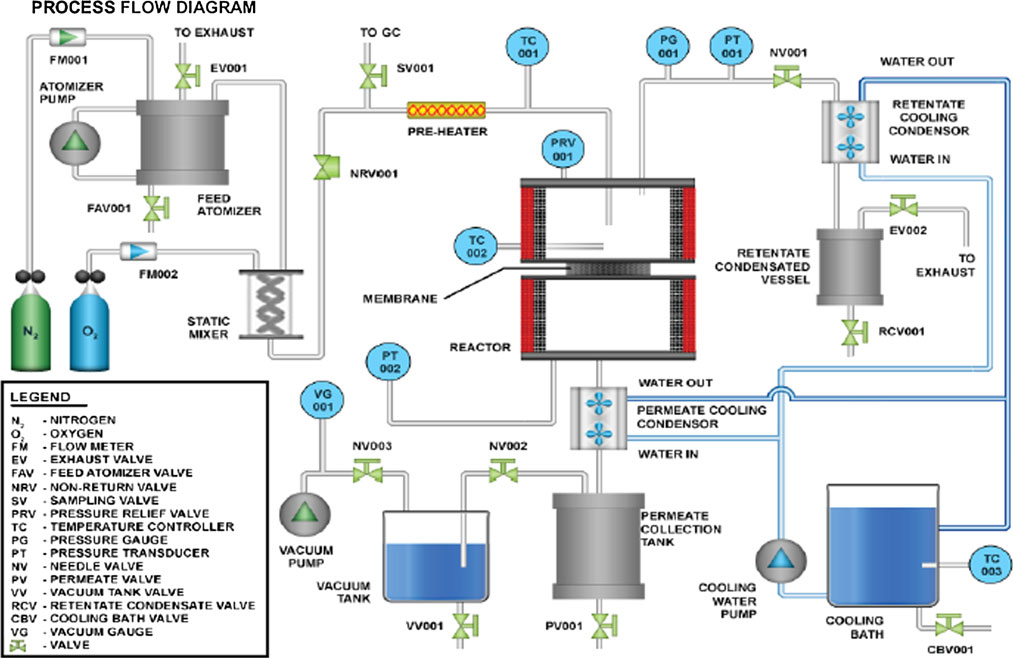
J Sol-Gel Sci Technol
Fig. 1 Schematic diagram of liquid permeation membrane test rig
2.2.4 Preparation of AlOOH sol with CNTs-VxOy catalysts
Table 1 Independent variables and their coded and actual values
by addition of PVA following peptization
used in the response surface study
To prepare a suspension of c-Al2O3 sol embedded with
CNTs-VxOy catalysts, 20 ml of boehmite sol was dilutedwith deionized water and then mixed with 0.04 g of CNTs-
VxOy and 40 cc of a solution of 0.8 g of PVA and 100 g
water. The prepared sol contained 10 % CNTs-VxOy. The
Temperature (°C)
mixture was then placed in an ultrasonic water bath with a
frequency of 37 kHz, a power of 150 watt and a temper-ature of 85 °C for 30 min to disperse the catalyst bundles
procedure described in Sect. to form a boehmite sol.
and agglomerates in the sol solution. After sonification, the
A boehmite sol, with a pH value of 3.32, was obtained. To
solution was stirred for 24 h.
prepare the suspension of c-Al2O3 sol with CNTs-VxOy
The binders applied to prepare the sol solution with the
catalysts, 22 cc of boehmite sol was diluted with deionized
catalyst were polyethylene glycol (PEG) and polyvinyl
water and mixed with 0.04 g of CNTs-VxOy.
alcohol (PVA) with average molecular weights of 10,000
To prepare a sol using a binder mixture, 4 g of equal
and 30,000–70,000, respectively.
wt% PVA and PEG was mixed with deionized water fol-lowing the procedure described in this section.
2.2.5 Preparation of AlOOH sol with CNTs-VxOy catalysts
by addition of PVA/PEG prior to peptization
2.2.6 Preparation and pre-treatment of a-alumina support
for coating the catalytic membrane
Enough PVA binder to prepare a final solution with 2 wt%PVA was stirred with deionized water at 90 °C for 10 h.
Homemade alumina support pellets were prepared from
Alumium tri-sec-butoxide was then added following the
alumina powder with a particle size of less than 250 lm.
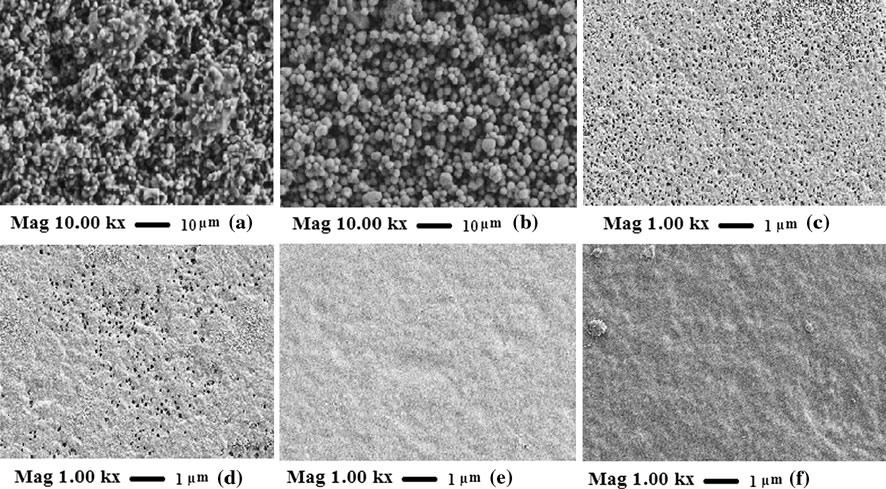
J Sol-Gel Sci Technol
The alumina pellets, which had diameters of 20 mm and
containing 0.1 g/l of particles. If particles have a low Zeta
thicknesses of 2 mm, were dried and calcinated at 1,000 °C
potential value, then there is no force to prevent particle
for 3.5 h. The a-alumina disk was then cleaned with
aggregation, and there is dispersion instability. The divid-
deionized water in an ultrasonic bath to remove unbounded
ing line between stable and unstable aqueous dispersions is
particles. This was repeated several times until the deion-
generally considered to be ?30 or -30 mV. For Al(OH)3,
ized water had changed from its initial milky white color to
the isoelectric point, the point at which the Zeta potential is
a clear solution. Next, the a-alumina disk was cleaned in a
zero, occurs at a pH of 7.5 [
mixture of 2-propanol, ethanol, and deionized water in avolumetric ratio of 1:2:2 in an ultrasonic bath with the
2.4 Styrene oxidation: experimental set-up and analysis
same conditions. This
was repeated several
The modified support was then dried at 130 °C for 5 h. The
Styrene oxidation and liquid permeation were conducted
introduced functional group (-OH) on the surface of the
using the experimental set-up shown in the schematics
membrane helped to achieve a better coating of CNT-VxOy
diagram (Fig. ). The membrane disks were sealed with
embedded in c-Al2O3 under acidic conditions.
silicon O-rings in a custom stainless steel permeation cell,
A thin layer of CNTs-VxOy-alumina was deposited onto
which was placed inside a jacketed heater. The liquid
the support using the dip coating technique. The support
permeation test rig consisted of four sections: (a) a feed
was dipped in the sol for 12 s and then dried at ambient
atomizer; (b) a preheater; (c) a reaction chamber; and (e) a
temperature for 12 h to obtain a dry gel layer. The dried gel
product collector. Prior to the start of an experiment, the
layer was calcinated at 550 °C for 3 h to produce a sup-
membrane was pretreated at 150 °C under a nitrogen flow
ported CNTs-VxOy-alumina membrane.
of 100 ml/min for 1 h to remove all moisture and impuri-ties. Nitrogen gas was used as the carrier gas. N2 gas car-
2.3 Zeta potential and particle size of Al2O3
ried the atomized liquid mixture, which consisted ofstyrene, acetone and hydrogen peroxide, at different tem-
To prepare stable colloids, the Zeta potential of the Al2O3
peratures and pressures. To provide pressure differences,
sol was evaluated using the laser Doppler velocimetry
the support side was drained using a vacuum pump.
technique at different pH values. The pH of the samples
The flow rate of the carrier gas streams was measured
was controlled using HNO3. The Zeta potential and particle
with a mass flow meter GFM (Model FM17, AALBORG,
size measurements were performed in dilute suspensions
USA). The feed side pressure, which was typically in the
Fig. 2 Effect of ultrasonic treatment on coating of membrane a surface
d coating with AlOOH ? PVA ? PEG without any treatment on
of support before treatment, b surface of support after treatment,
support, e coating with AlOOH ? PVA after support treatment,
c coating with AlOOH ? PVA without any support treatment,
f coating with AlOOH ? PVA ? PEG after support treatment
J Sol-Gel Sci Technol
Table 2 Zeta potential and mean particle size sol Al2O3
varied between the high level (?1) and the low level (-1),with the center points coded at level 25 and the two outer
points corresponding to an a value of 2. The design con-
sisted of 6 center points, 8 axial points and 16 fact points,rendering a total of 30 runs, which were used to analyze the
experimental data. These data were then used to optimize
PVA added to Al2O3 sol after
the operating conditions. The measured responses were
styrene conversion and benzaldehyde selectivity. The
PVA added to sol before
mathematical model chosen from the CCD had the highest
PVA ? PEG added to sol
polynomial order in which the insignificant conditions
before peptization
were aliased. The design factors and levels involved in theexperiment are shown in Table
To improve efficiency, the responses can be related to
selected factors by linear or quadratic models. A quadratic
range of 100–400 cm3 min-1, was adjusted by regulating
model, which includes the linear model, has been reported
the carrier gas flow through the atomizer. The vacuum
pressure on the permeate side was maintained at 35 mm
Hg, and the temperature was maintained at 4 °C using
cooling water to condense the solvent. A GC (Agilent
technologies, Model 7890A GC system), equipped with
where g is the predicted response; X
long 9 0.32 mm ID 9 0.25 lm film thickness) and an FID
i and Xj are the vari-
detector, was used to analyze the feed and permeate
0 is the constant coefficient; bj, bjj and bij are the
interaction coefficients of the linear, quadratic and second-
streams. After the system reached steady-state, permeate
order terms, respectively; and e
quality was calculated based on peaks, as determined by
i is the error (Eq.
the gas chromatograph (GC).
2.6 Physical characterization
2.5 Design of experiment (DOE)
The prepared catalysts and membranes were analyzed
DOE was used to study the effects of four factors, tem-
using a transmission electron microscope (TEM) (Philips
perature, differential pressure, catalyst concentration, and
CM12 machine equipped with DOCU version 3.2 image
ratio of styrene to oxidant, on styrene conversion and
analysis systems) at an accelerating voltage of 80 kV and a
benzaldehyde selectivity. The range of the study was
scanning electron microscope (SEM) (SUPRA TM 35vp
chosen based on preliminary studies and a literature review
Zeiss instrument equipped with a W-Tungsten filament) to
[The central composite design (CCD), with a full
investigate the morphology and microstructure of the
factorial, was selected using the Design Expert software
samples. Nitrogen adsorption (Micromeretics ASAP 2020)
(Version 6.0.6, Stat-Ease Inc., MN, USA). Each factor was
was used to measure the BET surface area, pore volumeand pore size of the catalyst. The thermal stabilities of thecatalyst and the unsupported membrane were studied by
Table 3 The surface area and pore volume of raw materials and
thermal gravimetric analysis (PERKIN ELMER TGA7) in
air at a heating rate of 10 °C/min from room temperature to
Pore volume (cm3/g)
a final temperature of 800 °C. A Malvern zetasizer nano
between 17.00 and
series analyzer (Nano-zs) was used to study the dielectric
properties and sizes of the alumina sol.
MWCNTs acid treated
3 Result and discussion
PVA added to sol Al2O3 after
Figure b show the surface area of the membrane support
PVA added to sol Al2O3 before
before and after modification with solvent under ultrasonic
conditions (described in Sect. , respectively. As shown
PVA ? PEG added to sol Al2O3
in these figures, the surface after treatment had more uniform
before peptization step
particles than with untreated one because of removing
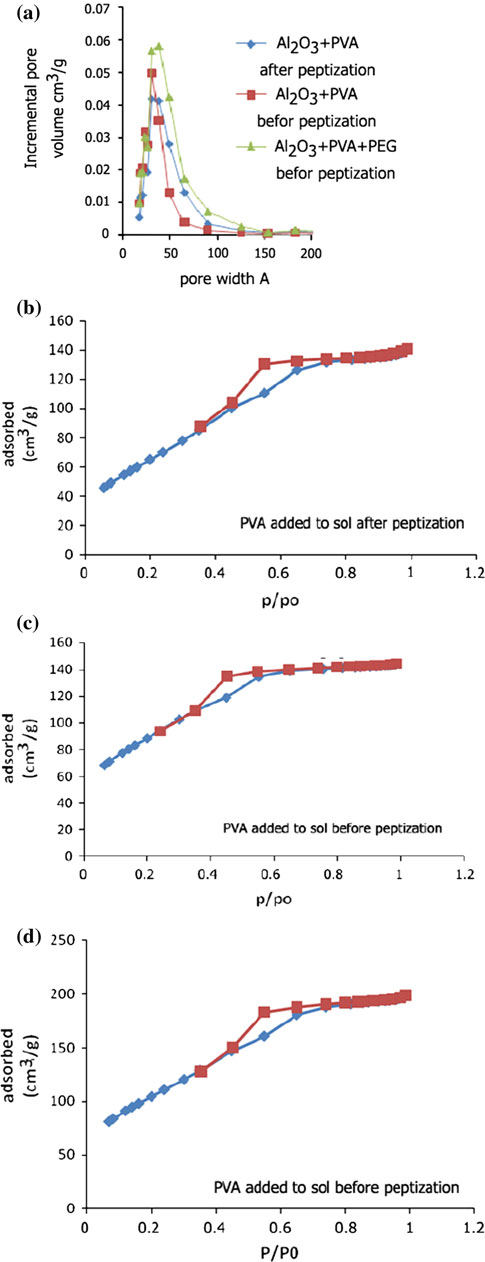
J Sol-Gel Sci Technol
unbounded particle in an ultrasonic condition. As seen and isdefinable from the figures, it is clearly understood that thesurface treated with solvent under ultrasonic condition has farbetter and uniformed particles, it shows no unbounded parti-cles, as a result it proves the unique action of the solvent in anultrasonic treatment environment rather and comparing withthe untreated ones due to the removal of the unbounded par-ticles which is the result of the action of the solvent treatedwith homogeneous coated solution, now and therefore anexcellent adsorption site for the acidic solution was adopted,where for and on the supported surface without any treatmentno such result was observed. Figure c, d show the mem-branes coated with sol (AlOOH ? PVA) and (AlOOH ?PVA ? PEG), respectively, on the support surface withoutany treatment. In both samples, binder was added to the solprior to peptization. As shown in the SEM images, the coatingwas not homogenous and had many holes on the surface.
However, for the solvent-treated support, the solution coatingwas homogenous and smooth, as shown in Fig. e, f. Theresults show that the functional group introduced onto themembrane surface after solvent treatment provided excellentadsorption sites for the acidic sol.
Table shows the Zeta potential and mean particle size
of the sol Al2O3 with and without binder under different pHconditions. Based on the results, the sol alumina withoutany binder was stable, but when PVA was added afterpeptization, the stability of the sol decreased, as shown bythe reduced Zeta potential of 15.2 mV. However, whenbinder was added to the sol prior to peptization, a morestable sol was obtained as a result of steric repulsion of thesol by the adsorbing polymers. Conversely, the higherpolymer contents contributed by the binder caused mem-brane defects related to shrinkage during the calcinationprocess required to produce an optimum membrane.
The specific surface area and pore volume of the catalyst
and the unsupported membrane were analyzed usingnitrogen adsorption at -197°C. The physical characteris-tics of the raw MWCNTs, the acid-treated MWCNTs, theCNTs-VxOy, and three different types of unsupportedmembranes are listed in Table . Based on this analysis, weconcluded that the catalyst and all unsupported membraneshad meso-pores because the pores were larger than 2 nm.
The significant increase in the surface area of acid-treatedMWCNTs can be explained by the opening of pores by theMWCNTs, which makes the internal surface more acces-sible. However, after impregnation, the surface area of theprepared catalysts dropped drastically. This decrease insurface area and pore volume clearly indicates that theVxOy complexes were impregnated inside the MWCNTs.
Conversely, mixing the CNTs-VxOy with alumina sols
prepared with different membrane support coating methods
b–d adsorption isotherms of unsupported sample
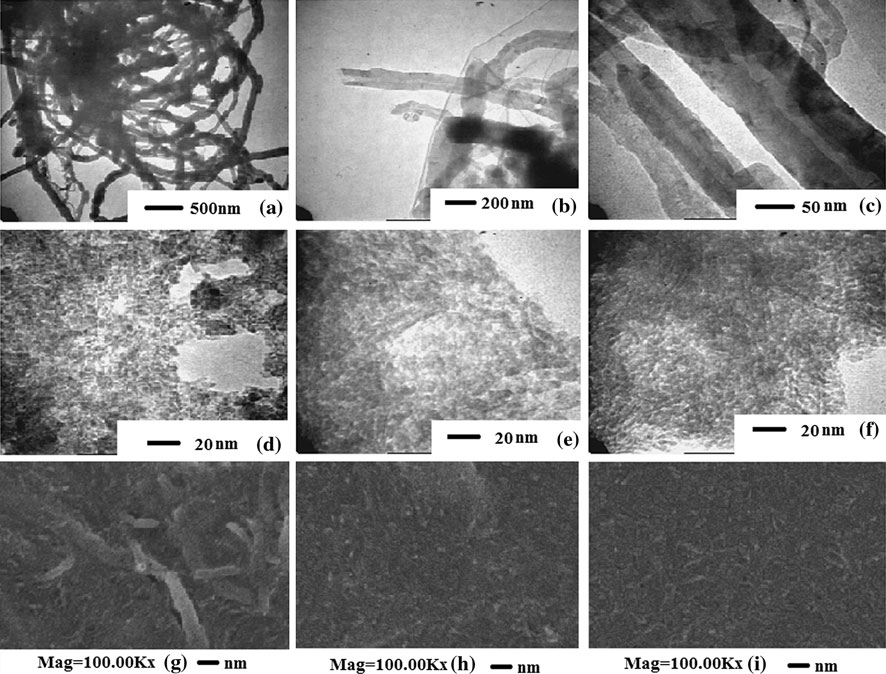
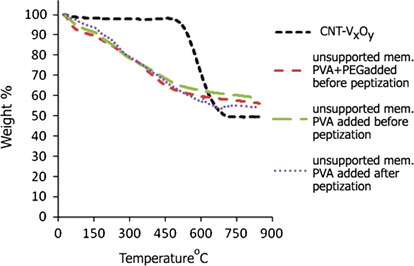
J Sol-Gel Sci Technol
Fig. 4 SEM images of CNT-VxOy catalytic membrane TEM image
membrane PVA ? PEG add to sol before peptization SEM images of
of a MWCNTs, b acid-treated MWCNTs, c the CNTs-VxOy,
g membrane, PVA add to sol after peptization h membrane, PVA add
d unsupported membrane PVA add to sol after peptization, e unsup-
to sol before peptization i membrane, PVA ? PEG add to sol before
ported membrane PVA add to sol before peptization, f unsupported
the PVA, PEG and boehmite particles occurred duringpeptization. The dispersion of binder inside the solprovided a homogenous surface area. However, whenPVA was added to the sol after peptization, particles couldnot disperse uniformly, increasing the porosity of themembrane.
As shown in Fig. the pore size distribution of the
unsupported membrane prepared by adding PVA or PEG atdifferent times could be narrowly controlled. The mem-brane pore size distribution of the membrane prepared byadding PVA prior to peptization was narrower than that of
Fig. 5 Weight loss curve for catalyst and unsupported membrane
the membrane prepared by adding PVA to the sol afterpeptization. The pore size distribution of this membrane
increased the specific surface area because Al2O3 possesses
was narrow compared to that of the membrane prepared by
a greater surface area and a more porous structure than
adding the PVA and PEG mixture as a binder during
VxOy. The addition of PVA and PEG prior to peptization
peptization. The addition of binder molecules to the alu-
resulted in a higher surface area for the unsupported
mina sol prior to peptization resulted in a uniformly dis-
membrane. Using a mixture of PVA and PEG as a binder
tributed sol. Conversely, the addition of PEG increased the
produced larger pore volumes than the use of PVA alone.
pore volume, pore diameter and BET surface area. As
This result indicates that more hydrogen bonding among
shown in the adsorption isotherms of Fig. d, monolayer
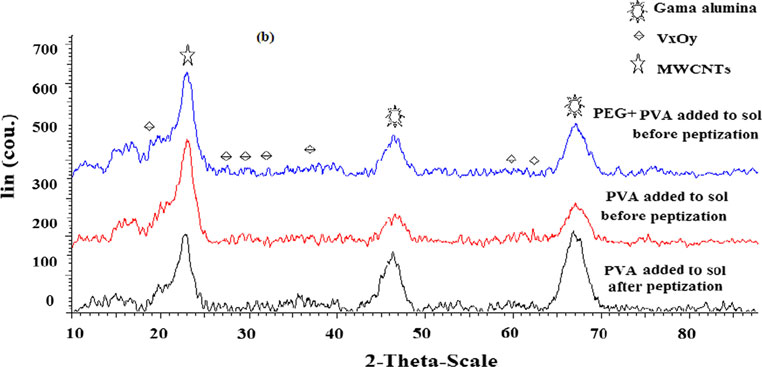
J Sol-Gel Sci Technol
Fig. 6 XRD patterns ofunsupported membrane withdifferent condition ofpreparation
formation was usually complete when the relative pressure
the CNTs-VxOy catalyst inside the membrane was random.
reached 0.3 because the radius available for condensation
However, the distribution of catalyst inside the membrane
was decreased by the thickness of the monolayer or by
prepared by adding PVA (Fig. or a mixture of PVA and
approximately two molecular diameters. Based on the
PEG (Fig. i) after peptization was much better than that
results, the samples with relative pressures above 0.3 had
inside the membrane prepared by adding PVA after pep-
type IV hysteresis according to the IUPAC classification,
indicating the presence of mesoporous materials related to
The thermogravimetric weight loss curves for the CNT-
cylindrical pores open at both ends ].
VxOy and unsupported membranes are shown in Fig.
The TEM images (Fig. show that the acid-treated
The thermal gravity curve in air for the CNT-VxOy catalyst
MWCNTs had an open-ended structure and some defects
shows that a major weight loss occurred at temperatures
following acid treatment. The pentagonal defects and the
greater than 500 °C, corresponding to the decomposition of
curved dimensional area are important because they can
the CNT template and indicating that 49 wt% was a result
increase reactivity as a result of the tubes' structural
of VxOy loading []. As shown, the higher weigh
instability []. Figure c demonstrates that VxOy was
ts associated with the residue were a result of the VxOy and
successfully distributed on the surface and within the
c-Al2O3 on the surface of the support.
CNTs. It can be noticed from the image that the VxOy
For all the unsupported membranes, the initial losses of
impregnated inside MWCNTs. The walls of MWCNTs are
physically bound water and volatile materials were similar
presented with randomly margins of dark and bright
and occurred at temperatures below 150 °C. The weight
regions. The bright margins represent CNTs, while dark
losses at temperatures between 250 and 280 °C coincided
margins (few nm) represent the vanadium oxide nanopar-
with the evolution of H2O, CO2, and ethylene oxides, based
ticles, which are intercalated between the CNTs layers.
on the decomposition of PVA or PEG, and weight losses at
Figure d–f show the unsupported membranes prepared
temperatures between 400 and 450 °C were due to the
with different binders under different conditions. Figure d
phase change of boehmite to c-Al2O3. This occurred at
shows the membrane for which PVA was applied as a
temperatures near 400 °C, and the losses of water were a
binder after peptization of the Al2O3 sol. Figure f show
result of reactions with the small amount of carbon residues
the membranes for which PVA and a mixture of PVA and
from the binder ,
PEG, respectively, were added to the sol Al2O3 prior to
2A1OOH ! c - A12O3 þ H2O:
peptization. The distribution and homogeneity of particlesin the unsupported membrane prepared by adding PVA or a
Figure shows the XRD patterns of the unsupported
mixture of PVA and PEG to the sol Al2O3 prior to pepti-
membrane prepared with the sol Al2O3 and different
zation were much better than those of the membrane pre-
binders in the presence of CNTs-VxOy. It was calcinated in
pared by adding PVA after peptization. As shown in
air at a heating rate of 3 °C/min and remained at 550 °C for
Fig. large holes were present in the unsupported
3 h. The XRD patterns confirm that the composites were a
membrane when PVA was added after peptization.
hybrid of c-Al2O3, VxOy and MWCNTs. The XRD results
Scanning electronic microscope (SEM) images of the
indicate that the mixed composition of the products
CNTs-VxOy membrane supported on a-alumina are shown
matched the patterns of different types of V2O5.H2O and
in Fig. As shown in these figures, the orientation of
6VO2.5H2O. The peaks at 2h = 26.2° and 2h = 50.6°
J Sol-Gel Sci Technol
Table 4 The experimental data
for the oxidation of styrene
Amount of styrene of each
experiment is 2 mol
Amount of solvent 1,000 ml
Table 5 ANOVA table for styrene oxidation
Styrene conversion
Benzaldehyde selectivity
DF degree of freedom, CV coefficient of variation, std. Dev. standard deviation
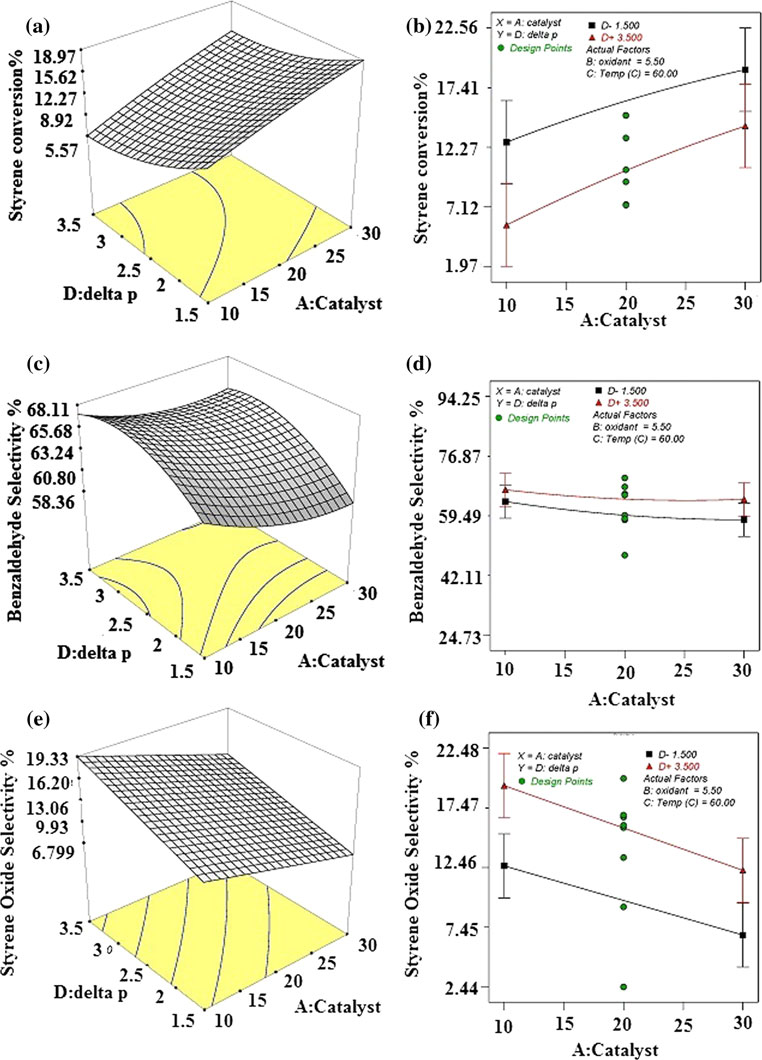
J Sol-Gel Sci Technol
Fig. 7 Response surface plotshowing the effect of catalystpercentage and differentialpressure, and their mutual effecton the conversion of styrene(a, b) and on benzaldehydeselectivity (c, d) and styreneoxide selectivity (e, f)
correspond to the (110) and (020) diffraction planes of
presence of c-Al2O3, VxOy and MWCNTs in the composite
V2O5, respectively [].
membranes and indicate that the choice of binder did not
The peaks at 2h = 23.5 and 2h = 26.3° correspond to
affect the membrane properties.
MWCNTs. The peaks overlap with the V2O5 peak (110),corresponding to the reflection peak (002) associated withthe inner layer spacing of nanotubes (d002 = 0.338 nm).
4 Model fitting and analysis of variance (ANOVA)
Most peaks also had low intensities, indicating that theV2O5–MWCNTs nanocomposite had a microcrystal struc-
The experimental data related to the oxidation of styrene to
ture ]. The XRD patterns at 2h = 46.2° and 67° cor-
benzaldehyde using supported membranes and an appli-
respond to c-Al2O3 ]. For all the preparation methods,
cation of PVA ? PEG prior to peptization are given in
similar XRD patterns were found. These results confirm the
Table The ANOVA results show that the reaction of
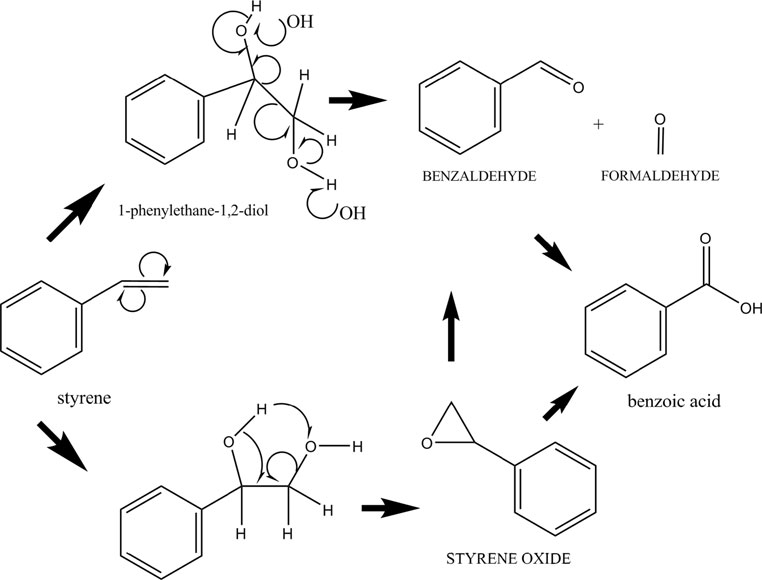
J Sol-Gel Sci Technol
Fig. 8 Scheme styreneoxidation
styrene with H2O2 is best described by a quadratic poly-
result of data variation in the fitted model [The lack-
nomial model. The quadratic models for styrene conversion
of-fit F-values of 3.14 for styrene conversion and 2.59 for
(Eq. ) and benzaldehyde selectivity (Eq. ) are given
benzaldehyde selectivity are within the acceptable error
Figure displays the effect of catalyst loading on con-
Styrene ðconversion %Þ ¼ 11:68 þ 3:70A 7:25B
version and product selectivity during oxidation in the
þ 3:05C 3:00D 0:43A2
catalytic membrane. As expected, increasing catalyst
þ 1:49B2 þ 2:36C2 þ 1:60D2
loading (i.e., the amount of catalyst by wt% on the surface
6:33AB þ 3:54AC þ 0:57AD
of membrane) from 10 to 30 % resulted in higher styrene
3:93BC þ 0:59BD þ 1:17CD
conversion because there was more contact between the
precursor and the catalyst. Conversely, benzaldehydeselectivity and styrene oxidation decreased at higher cata-
Benzaldehyde ðselectivity %Þ ¼ 64:47 2:02A 2:63B
lyst loadings. This occurred because the product could be
converted to by-products, according to the mechanism
þ 1:33A2 3:04B2
proposed in Fig. , at longer contact times between the
þ 0:027C2 2:45D2
benzaldehyde or styrene oxide and the catalyst. Figure
þ 1:67AB 9:82AC
shows the scheme formation mechanism of the six
þ 0:63AD þ 13:89BC
observed products. As shown in Fig. benzaldehyde was
þ 2:16BD 5:18CD
produced through direct oxidative cleavage of the styrene
double bond or through nucleophilic attack of the styrene
Table shows that both the styrene conversion and
oxide [catalytic reaction was solely caused by
benzaldehyde selectivity terms were less than 0.05 of the
VxOy, as the alumina particles, acid wash MWCNTs, alu-
probability of the F values, indicating significance of the
mina membrane and mix matrix alumina membrane
model results. The integrity of the model fit was quantified
include MWCNTs had no effect on styrene conversion. No
using the determination coefficient (R2) [In this case,
sign of reaction was detected for the membrane and par-
the R2 values for styrene conversion (0.9014) and benz-
ticles in the presence of H2O2, demonstrating that the
aldhyde selectivity (0.9032) show that only 9.86 % of
reaction is merely catalyzed by VxOy and MWCNTs can
styrene oxidation and 9.68 % of benzaldehyde selectivity
provide channel for shorter contact time of reactant with
were not explained by the model. This discrepancy was the
J Sol-Gel Sci Technol
Fig. 9 Response surface plotshowing the effect of oxidantand differential temperature,and their mutual effect on theconversion of styrene(a, b) andon benzaldehyde selectivity(c, d) and styrene oxideselectivity (e, f)
Styrene conversion and product selectivity at various
The effects of H2O2 concentration on the conversion of
differential pressures (i.e., the pressure between the catalyst
styrene and product selectivity are presented in Fig.
and the permeate) are presented in Fig. At higher dif-
When the H2O2: styrene ratio was increased from 1.5:1 to
ferential pressures, styrene conversion rates were relatively
4:1, the styrene conversion obviously decreased. This could
lower with improved benzaldehyde and styrene oxide
have been a result of the H2O2 shielding effect caused by
selectivity. This result also shows that extended reaction
the formation of styrene in the H2O2 emulsion. When the
times between the product and the catalyst produced
amount of H2O2 was increased, the shielded styrene
by-products such as benzoic acid and benzene, which
molecules were prevented from contacting the catalyst
decreased the selectivity of both benzaldehyde and styrene
surface, therefore reducing the reaction rate. This effect
was more pronounced at low temperatures because at low
J Sol-Gel Sci Technol
Fig. 10 FTIR spectra of polystyrene
Table 6 Limitations adjusted to reach the optimal value for styrene
membrane surface, as shown by the FTIR results in
oxidation to benzaldehyde
Table shows the optimum differential pressure (delta
p), temperature, catalyst and oxidant concentration condi-tions for styrene oxidation and benzaldehyde selectivity.
To validate the model, a series of experiments was con-
ducted under the following predetermined conditions: a
reaction temperature of 45 °C, a differential pressure of
1.5 bar; an H2O2: styrene molar ratio of 1.5:1 and a catalyst
concentration of 30 %. An optimum styrene conversion of
25.6 % and a benzaldehyde selectivity of 84.9 % were
temperatures, the emulsion was relatively more stable. At
high H2O2 concentrations and low temperatures, the stableH2O2 emulsion on the catalyst surface prevented the further
Nanocomposite membranes were successfully prepared by
reaction of styrene oxides; as a result, benzaldehyde
embedding VxOy and CNTs into a c-Al2O3 matrix using
selectivity was low. Because of the instability of the
the dip coating method. The structure and morphology of
emulsion and the further reaction of styrene oxides with the
the catalytic membranes synthesized on the alumina sup-
catalyst to produce benzaldehydes at high temperatures,
port were extremely sensitive to the pretreatment method.
benzaldehyde selectivity increased.
Methods such as ultrasonic cleaning, modifying surface
The styrene conversion rates and product selectivity at
functional groups and adding a binder could be employed
different reaction temperatures are shown in Fig. As
to prepare uniform membranes. The coated membranes had
expected for low temperatures, the benzaldehyde and sty-
a smooth, homogeneous surface layer, and no cracking or
rene oxide selectivity were higher, and the styrene con-
delaminating phenomena were observed between the
version rates were lower. In the range of 45–65 °C, styrene
underlying membrane and the coating layer. The catalytic
conversion increased as the temperature increased. This
contactor membrane oxidized styrene to benzaldehyde at a
occurred because the increased temperatures caused more
styrene conversion rate of 25 % and a benzaldehyde
styrene oxide and benzaldehyde molecules to decompose
selectivity of 85 % under optimum conditions, which
to other by-products. Further increasing the temperature
included a temperature of 45 °C, an H2O2:styrene molar
([65 °C) caused a sudden flux reduction. This was due to
ratio of 1.5:1, a differential pressure of 1.5 bar and a cat-
the polymerization of styrene to polystyrene ] on the
alyst loading of 30 %.
J Sol-Gel Sci Technol
The authors gratefully acknowledge the Minis-
21. Xu JF et al (2002) Nonlinear optical transmission in VOx nano-
try of Science, Technology and Innovation (Malaysia) for providing
tubes and VOx nanotube composites. Appl Phys Lett 81(9):1711–
financial support (2008 science fund 03-01-05-SF0401) for this study.
22. Weckhuysen BM, Keller DE (2003) Chemistry, spectroscopy and
the role of supported vanadium oxides in heterogeneous catalysis.
Catalysis Today 78(1–4 SPEC.):25–46
23. Lutz JT, Grayson M, Eckroth D, Bushey GJ, Eastman CI,
Klingsberg A, Spiro L (eds) (1980) Kirk–Othmer Encyclopedia
1. Sun YM, Khang SJ (2002) A catalytic membrane reactor: its
of Chemical Technology, vol 9, 3rd edn.Wiley, NewYork,
performance in comparison with other types of reactors. Ind Eng
Chem Res 29(2):232–238
24. Coperet C, Adolfsson H, Sharpless KB (1997) A simple and
2. Uhlhorn RJR, Huits In't Veld MHBJ, Keizer K, Burggraaf AJ
efficient method for epoxidation of terminalalkenes. Chem
(1989) First international conference on inorganic membranes.
Montpellier, France, pp 323–328.
25. Swern D (1971) OrganicPeroxides, vol 2. Wiley Interscience,
3. Saracco G (1998) Structured catalysts and reactors. Marcel
Dekker, New York, pp 463–500
26. Wang L et al (2005) Direct synthesis, characterization of
4. Fain DE (1994) Inorganic membranes: the new industrial revo-
Cu-SBA-15 and its high catalytic activity in hydroxylation of
lution, ICIM394, July 10–14, 1994
phenol by H2O2. J Mol Catal A: Chem 230(1–2):143–150
5. Han SH et al (2008) Control of pore characteristics in carbon
27. Selvaraj M, Song SW, Kawi S (2008) Epoxidation of styrene over
molecular sieve membranes (CMSM) using organic/inorganic
mesoporous Zr-Mn-MCM-41. Microporous Mesoporous Mater
hybrid materials. Desalination 233(1–3):88–95
6. Rahman MA et al (2011) Development of a catalytic hollow fibre
28. Al-Ajlouni AM et al (2008) Kinetic studies on phenylpho-
membrane micro-reactor for high purity H2 production. J Membr
sphopolyperoxotungstates catalyzed epoxidation of olefins with
Sci 368:116–123
hydrogen peroxide. J Mol Catal A: Chem 287(1–2):159–164
7. Tsuru T (2008) Nano/subnano-tuning of porous ceramic membranes
29. Hulea V, Dumitriu E (2004) Styrene oxidation withH2O2 over
for molecular separation. J Sol-Gel Sci Technol 46(3):349–361
Ti-containing molecular sieves with MFI, BEA and MCM-41
8. Julbe A, Farrusseng D, Guizard C (2001) Porous ceramic mem-
topologies. Appl Catal A 277(1–2):99–106
branes for catalytic reactors—overview and new ideas. J Member
30. Datsyuk V et al (2008) Chemical oxidation of multiwalled carbon
Sci 181(1):3–20
nanotubes. Carbon 46(6):833–840
9. Dong J et al (2008) Microporous inorganic membranes for high
31. Chen X et al. (2007) Carbon nanotube-induced preparation of
temperature hydrogen purification. J Appl Phys 104(12):
vanadium oxide nanorods: application as a catalyst for the partial
oxidation of n-butane. Mater Res Bull 42:354–361
10. Bottino A et al (2005) Vapour phase oxidation of toluene in
32. Du X et al (2009) Influences of pH value on the microstructure
V/Al2O3-TiO2 catalytic reactors. Catal Today 99(1–2):171–177
and phase transformation of aluminum hydroxide. Powder
11. Alfonso MJ, Mene´ndez M, Santamarı´a J (2000) Vanadium-based
Technol 192(1):40–46
catalytic membrane reactors for the oxidative dehydrogenation of
33. El-Masry MH, Sadek OM, Mekhemer WK (2004) Purification of
propane. Catal Today 56(1–3):247–252
raw surface water using electro-coagulation method. Water Air
12. Xia C et al (1996) Boehmite sol properties and preparation of
Soil Pollut 158(1):373–385
two-layer alumina membrane by a sol-gel process. J Membr Sci
34. Guin D, Baruwati B, Manorama SV (2005) A simple chemical
synthesis of nanocrystalline AFe2O4 (A = Fe, Ni, Zn): An effi-
13. Alfonso MJ, Mene´ndez M, Santamarı´a J (2002) Oxidative
cient catalyst for selective oxidation of styrene. J Mol Catal A:
dehydrogenation of butane on V/MgO catalytic membranes.
Chem 242(1–2):26–31
Chem Eng J 90(1–2):131–138
35. Box G (1987) Statistics for experiments. An introduction to
14. Alfonso MJ et al (1999) Oxidative dehydrogenation of propane on
design, data analysis and model building. Wiley, New York
V/Al2O3 catalytic membranes. Effect of the type of membrane and
36. Donohue MD, Aranovich GL (1999) A new classification of
reactant feed configuration. Chem Eng Sci 54(9):1265–1272
isotherms for Gibbs adsorption of gases on solids. Fluid Phase
15. Teixeira M et al (2011) Improving propyne removal from pro-
pylene streams using a catalytic membrane reactor-a theoretical
37. Wildgoose GG, Banks CE, Compton RG (2006) Metal nano-
study. J Membr Sci 375(1–2):124–133
particles and related materials supported on Carbon nanotubes:
16. Deshayes AL, Miro´ EE, Horowitz GI (2006) Xylene isomeriza-
methods and applications. Small 2(2):182–193
tion in a membrane reactor: part II. Simulation of an industrial
38. Iijima S (1991) Helical microtubules of graphitic carbon. Nature
reactor. Chem Eng J 122(3):149–157
17. Thostenson ET, Ren Z, Chou T-W (2001) Advances in the sci-
39. Serp P, Corrias M, Kalck P (2003) Carbon nanotubes and
ence and technology of carbon nanotubes and their composites: a
nanofibers in catalysis. Appl Catal A 253(2):337–358
review. Compos Sci Technol 61(13):1899–1912
40. Ahmad A et al. (2010) Synthesis of vanadium oxide nanotubes
18. Sharma A, Tripathi B, Vijay YK (2010) Dramatic improvement
via an ultrasonic method. J Sol-Gel Sci Technol 56(3):1–6
in properties of magnetically aligned CNT/polymer nanocom-
41. Mishra R, Rao KJ (2000) Thermal and morphological studies of
posites. J Membr Sci 361(1–2):89–95
binary and ternary composites of poly(vinylalcohol) with alumina
19. Neri G et al. (2010) In: Malcovati P et al. (eds) A novel approach
and zirconia. Ceram Int 26(4):371–378
for the preparation of metal oxide/CNTs composites for sensing
42. Van Gestel T et al (2002) Alumina and titania multilayer mem-
applications, in sensors and microsystems, Springer Netherlands,
branes for nanofiltration: preparation, characterization and
chemical stability. J Membr Sci 207(1):73–89
20. Ledoux MJ et al (2001) High-yield butane to maleic anhydride direct
43. Wu G-M et al (2008) Investigation on properties of V2O5–
oxidation on vanadyl pyrophosphate supported on heat-conductive
MWCNTs composites as cathode materials. J Sol-Gel Sci
materials: b-SiC, Si3N4, and BN. J Catal 203(2):495–508
Technol 46(1):79–85
J Sol-Gel Sci Technol
44. Han Y-F et al (2007) Effects of different types of c-Al2O3 on the
47. Hulea V, Dumitriu E (2004) Styrene oxidation with H2O2 over
activity of gold nanoparticles for CO oxidation at low-tempera-
Ti-containing molecular sieves with MFI, BEA and MCM-41
tures. J Phys Chem C 111(7):3163–3170
topologies. Appl Catal A 277(1–2):99–106
45. Kshirsagar AC, Singhal RS (2007) Optimization of starch oleate
48. Jang BN, Wilkie CA (2005) The thermal degradation of poly-
derivatives from native corn and hydrolyzed corn starch by
styrene nanocomposite. Polymer 46(9):2933–2942
response surface methodology. Carbohydr Polym 69(3):455–461
46. Gao YL et al (2007) Investigation of the effects of food con-
stituents on Bacillus subtilis reduction during high pressure andmoderate temperature. Food Control 18(10):1250–1257
Source: http://www.2pk.ir/pedex/upload/article/1406010336.pdf
Diagnosis,Therapy and Prophylaxis of Fungal Diseases Guideline vulvovaginal candidosis (2010) of the german society forgynecology and obstetrics, the working group for infections andinfectimmunology in gynecology and obstetrics, the german societyof dermatology, the board of german dermatologists and the germanspeaking mycological society W. Mendling and J. Brasch Prof. Dr. med. Werner Mendling, Vivantes – Klinikum im Friedrichshain and Am Urban, Clinics for Obstetrics and Gynecology (2011 retired), 10249 Berlin,Landsberger Allee 49Prof. Dr. med. Jochen Brasch, University Hospitals of Schleswig – Holstein, Campus Kiel, Department of Dermatology, Venerology and Allergology,Schittenhelmstrasse 7, 24105 Kiel, Germany
3 – 7 September 2007 Hobart, Tasmania AUSTRALIA THE ORGANISERS OF THE 6th INTERNATIONAL PENGUIN CONFERENCE GRATEFULLY ACKNOWLEDGE THE FOLLOWING SPONSORS AND SUPPORTERS OF THE CONFERENCE. Sponsors Supporters 3 – 7 September 2007 Hobart, Tasmania AUSTRALIA