Pnas201210072 17360.17365

Flexible graphene-based lithium ion batteries withultrafast charge and discharge ratesNa Lia,b,1, Zongping Chena,1, Wencai Rena, Feng Lia, and Hui-Ming Chenga,2
aShenyang National Laboratory for Materials Science, Institute of Metal Research, Chinese Academy of Sciences, Shenyang 110016, China; and bDepartmentof Materials Science & Engineering, School of Chemistry and Materials Science, University of Science and Technology of China, Hefei 230026, China
Edited* by Mildred S. Dresselhaus, Massachusetts Institute of Technology, Cambridge, MA 02139 and approved September 17, 2012 (received for review June13, 2012)
There is growing interest in thin, lightweight, and flexible energy
nanomaterials (16–18). Based on these strategies, electrodes
storage devices to meet the special needs for next-generation,
with a highly conductive pathway for electrons, a short ion dif-
high-performance, flexible electronics. Here we report a thin,
fusion length, and a fast transport channel for the ion flux can be
lightweight, and flexible lithium ion battery made from graphene
fabricated for fast charge and discharge. A series of electro-
foam, a three-dimensional, flexible, and conductive interconnected
chemical active materials (4, 15–18) and three-dimensional (3D)
network, as a current collector, loaded with Li4Ti5O12 and LiFePO4,
hybrid electrodes (5, 14) have been recently fabricated to as-
for use as anode and cathode, respectively. No metal current col-
semble rechargeable batteries with high charge and discharge
lectors, conducting additives, or binders are used. The excellent
rates. For example, Braun et al. (5) recently fabricated a mac-
electrical conductivity and pore structure of the hybrid electrodes
roporous nickel network for battery electrodes with ultrafast
enable rapid electron and ion transport. For example, the Li4Ti5O12/
charge and discharge rates, and 76% of the specific capacity was
graphene foam electrode shows a high rate up to 200 C, equivalent
retained when discharged at 185 C. However, these batteries are
to a full discharge in 18 s. Using them, we demonstrate a thin,
based on a complicated electrode package and rigid electrode
lightweight, and flexible full lithium ion battery with a high-rate
structures with metals as current collectors, which makes the
performance and energy density that can be repeatedly bent to
devices less flexible, and they also have a low energy density.
a radius of 5 mm without structural failure and performance loss.
Recently, we have fabricated a unique 3D graphene macro-
scopic structure: graphene foam (GF) (19). A GF consisting of
flexible device full battery
a 3D interconnected network of high-quality chemical vapordeposition-grown graphene can be used as the fast transport
The development of next-generation flexible electronics (1), channel of charge carriers. The electrical conductivity of the
such as soft, portable electronic products, roll-up displays,
GF is estimated as high as ∼1,000 S/m, and the solid conductivity
wearable devices, implantable biomedical devices, and conform-
of the few-layer graphene itself within the GF is evaluated to be
able health-monitoring electronic skin, requires power sources that
∼1.36 × 106 S/m . Moreover, the GF is extremely
are flexible (2, 3). Similar to conventional energy storage devices,
light (∼0.1 mg/cm2 with a thickness of ∼100 μm) and flexible. It
flexible power sources with high capacity and rate performance
possesses a high porosity of ∼99.7% and a very high specific
that enable electronic devices to be continuously used for a long
surface area and can be bent to arbitrary shapes without
time and fully charged in a very short time are very important for
breaking. In addition, the high quality and carbonaceous nature
applications of high-performance flexible electronics (4–7). Lith-
of graphene building blocks give the GF network excellent stability
ium ion batteries (LIBs) have a high capacity but usually suffer
in electrochemical environments. These features give the GF great
from a low charge/discharge rate compared with another important
potential for use in next-generation flexible electronics. Using theGF network as both a highly conductive pathway for electrons and
electrochemical storage device, supercapacitors. Therefore, it is
ions and a 3D interconnected current collector, we have de-
highly desired to fabricate a flexible electrochemical energy storage
veloped thin, lightweight, and flexible LiFePO
system with a supercapacitor-like fast charge/discharge rate and
battery-like high capacity. However, the fabrication of such an
4Ti5O12 (LTO)/GF electrodes that can simultaneously obtain
high charge and discharge rates up to 200 C (where a 1-C rate
energy storage device remains a great challenge owing to the lack
represents a 1-h complete charge or discharge). Using these
of reliable materials that combine superior electron and ion con-
flexible bulk electrodes, we further assembled a thin, lightweight,
ductivity, robust mechanical flexibility, and excellent corrosion re-
and flexible full LIB (Fig. 1) that shows high capacity and high-rate
sistance in electrochemical environments.
performance and is capable of repeated bending to a radius of
Using nano-sized materials to prepare electrodes is one of the
<5 mm without structural failure and loss of performance.
most promising routes toward flexible batteries. Metal oxidenanowires (8, 9) and carbon nanomaterials such as carbon
Results and Discussion
nanotubes (6, 10–12) and graphene paper (13) have been re-
Synthesis and Characterization of Free-Standing Flexible LTO/GF and
cently demonstrated for use in flexible LIBs. However, electron
LFP/GF. LTO and LFP have been considered as promising anode
transport in these electrodes is slow because of the relatively low
and cathode materials for commercial applications in LIBs be-
quality of nanomaterials (such as chemically derived graphene)
cause of their safety, environmental friendliness, and high
and/or high junction contact resistance between them. As aconsequence, only a moderate charge/discharge rate has beenobtained in these flexible batteries. It is generally believed that
Author contributions: N.L., Z.C., W.R., F.L., and H.-M.C. designed research; N.L. and Z.C.
the charge/discharge rate of a LIB depends critically on the
performed research; N.L., Z.C., W.R., F.L., and H.-M.C. analyzed data; and N.L., Z.C., W.R.,
migration rate of lithium ions and electrons through the elec-
F.L., and H.-M.C. wrote the paper.
trolyte and bulk electrodes into active electrode materials.
The authors declare no conflict of interest.
Strategies to increase ion and electron transport kinetics in bat-
*This Direct Submission article had a prearranged editor.
teries have mainly focused on seeking new electrode materials
1N.L. and Z.C. contributed equally to this work.
and designing conductive electrode structures with high ion and
2To whom correspondence should be addressed. E-mail:
electron transport rates (4, 5, 14, 15), or reducing the path length
This article contains supporting information online at
over which electrons and lithium ions have to move by using
17360–17365 PNAS October 23, 2012 vol. 109 no. 43

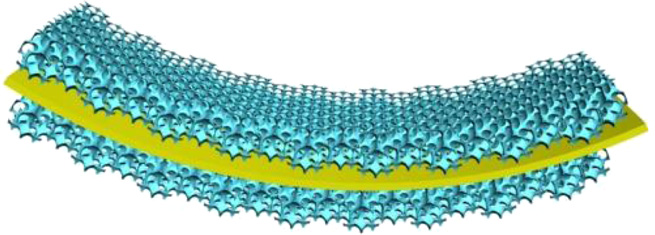

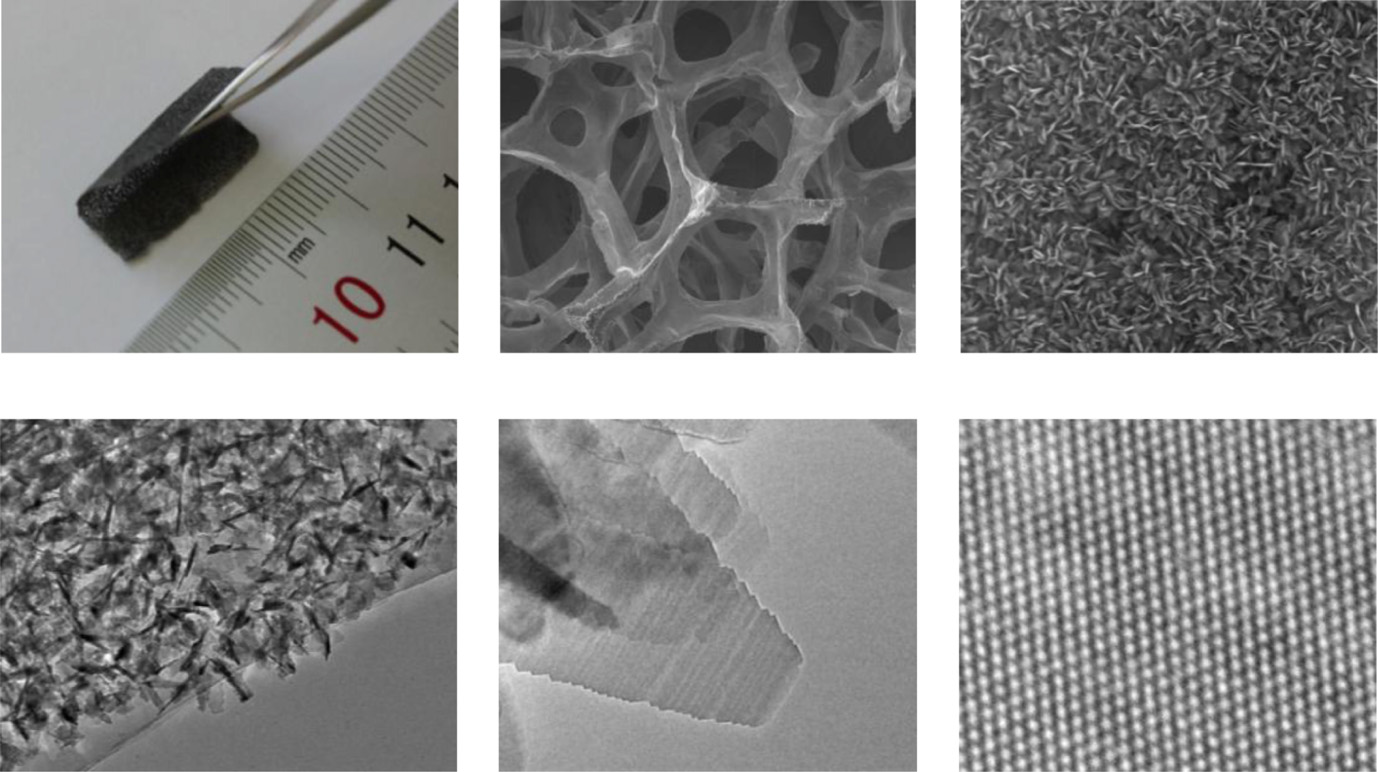
Schematic of a flexible battery containing a cathode and an anode made from 3D interconnected GF.
performance. To build a flexible LIB with a high capacity and
perpendicular to the surface of the GF, which not only provides
fast charge and discharge rates, we integrated highly conductive,
a large interfacial area for fast lithium insertion/extraction but
porous, and flexible GF with LTO and LFP as anode and cath-
also ensures a short solid-state diffusion length (Fig. 2 C and D
ode, respectively (Fig. 1). It is worth noting that the 3D porous
and The LTO sheet growth is nucleated at
GF network was directly used as a highly conductive pathway for
wrinkles on the GF because of their higher chemical reactivity
electrons/lithium ions and current collectors for the LIB, without
). The direct growth of LTO on the GF enables
the use of conventional metal current collectors, carbon black
good contact and strong binding between LTO and GF, with no
additive and binder. The LTO/GF and LFP/GF hybrid materials
need to add any binder. As a result, no LTO nanosheets were
were fabricated by in situ hydrothermal deposition of active
peeled off even after repeated bending (
materials on GF followed by heating in an argon atmosphere
The transmission electron microscope (TEM) image (Fig. 2E)
(details in Methods and ). Notably, similar to GF,
shows that the LTO nanosheets are several hundred nanometers
these hybrid materials are very flexible (Fig. 2A), can be bent into
in width and a few nanometers in thickness. The high-resolution
arbitrary shapes without breaking, and completely preserve the
TEM image in Fig. 2F indicates the high crystallinity of the
3D interconnected network structure of the GF (Fig. 2B).
nanosheets with a lattice fringe spacing of 4.8 Å, corresponding
The LTO in the hybrid material has a sheet structure a few
to the most stable and frequently observed (111) facet of spinel
nanometers in thickness, and high-density LTO sheets stand
LTO (), which is consistent with the X-ray
Characterization of a free-standing flexible LTO/GF. (A) Photograph of a free-standing flexible LTO/GF being bent (2 × 2 cm2). (B and C) SEM images of
the LTO/GF. (D) TEM image of the LTO/GF. (E) TEM image of the LTO nanosheets in LTO/GF. (F) High-resolution TEM image of a LTO nanosheet showing latticefringes with a spacing of 0.48 nm.
PNAS October 23, 2012 vol. 109 no. 43 17361

electrons, a short ion diffusion length, and a fast transport channel
for a high Li+ flux, which provide the electrodes with a great po-
tential for fast charge and discharge.
Electrochemical Behavior of the LTO/GF Anode. We investigated thelithium insertion/extraction properties of the LTO/GF material
by galvanostatic charge–discharge measurements (Fig. 3) and
Li4Ti5O12 and Li7Ti5O12
found that this LTO/GF hybrid material shows extremely high
charge/discharge rates. At a charge/discharge rate of 0.1 C,
the LTO/GF and LTO have similar specific charge/dischargecapacities. However, at charge/discharge rates of 1 C and 30 C,
the LTO/GF shows a specific capacity of about 170 and 160
mAh/g, respectively, and even at a charge and discharge rate of
200 C (corresponding to an 18-s full discharge), it still retains
fic capacity of 135 mAh/g, corresponding to ∼80% of the
specific capacity at the 1-C rate. In contrast, the reference LTO,
which was prepared using the same process but without the
presence of GF, shows a capacity of almost zero at 200 C, al-though it also has a 2D sheet structure ().
Moreover, the rate performance of this LTO/GF material is
much better than those reported in the literature for all kinds of
conventional LTO electrodes integrated with metal foil current
collectors, carbon black additive and binder, including nano-
crystalline LTO, carbon-coated LTO, and LTO/multiwalled car-
bon nanotube and LTO/graphene composites (
To further determine the stability of the electrode structure,
we studied the change in morphology of the LTO/GF electrode
after 100 charge/discharge cycles at 0.5 C and found that the LTO/
GF electrode is capable of long-term lithiation and delithiation at
low rates without structural failure ).
More strikingly, the discharge curve of the LTO/GF anode at
high rates (up to 200 C) shows a long,
flat potential plateau,
which ensures a constant power output, and therefore is very
important for the commercial use of LIBs (20). The flat plateausegment is a characteristic of two-phase equilibrium (21), a
room-temperature miscibility gap, as shown in Fig. 3A. In con-
trast, although many nanostructured materials have been devel-
oped to show high-rate performance (4, 5, 22–24), most of them
exhibit a nonflat plateau with a capacitor-like charge–discharge
curve at high rates. The profile change of voltage curves from flatto slope at high rates may be attributed to polarization related to
the poor electrical conductivity of electrode materials, or may
occur because electrode materials obey a pseudocapacitive (in-
terfacial) storage mechanism instead of a bulk intercalation
storage mechanism (25). The high-rate performance with a long,
flat plateau in the potential profile of the LTO/GF electrode
suggests excellent ion and electron transport kinetics of the
LTO/GF hybrid structure. As shown in Fig. 3C, the specific ca-
pacity of the flat plateau segment of the LTO/GF at 200 C is 86
Discharge rate and cyclic performance of the LTO/GF electrode. (A)
mAh/g, whereas the value of the reference LTO is almost zero.
Two-phase equilibrium region of the LTO/GF with different charge/discharge
Fig. 3D shows the cyclic stability of the LTO/GF at 30 C and 100
rates; C /n denotes the rate at which a full charge or discharge takes n hours.
C. Note that the capacity decreases less than 4% of the initial
(B) Discharging voltage curves of the LTO/GF with different charge/discharge
value after 500 cycles, demonstrating the excellent electro-
rates. (C) Specific capacities of the LTO/GF and reference LTO at various
chemical stability of this free-standing flexible electrode.
charge/discharge rates within a flat plateau segment shown in B. (D)
In general, in a commercial LIB, metal current collectors
Capacities of the LTO/GF charged/discharged at constant 30-C and 100-C
(mainly copper, ∼10 mg/cm2 and aluminum, ∼5 mg/cm2, with
rates for 500 cycles.
a thickness of ∼10–30 μm), conducting additives, and bindingagents are indispensable, and these account for 30–50% of the
diffraction measurements (JCPDS 49–0207;
electrode weight. Bulk electrodes constructed of either metal (5,
In addition, similar to the pristine GF (19), the Raman
14) or pyrolytic carbon (26) have recently been developed forfast charge and discharge, but metal current collectors are still
spectra of a free-standing LTO/GF material shows a strongly
needed for facilitating electron transport from the electrode to
suppressed defect-related D band (), in-
the cell. These metal and carbonaceous components of bulk
dicating the overall high quality of graphene in LTO/GF. This
electrodes make a battery cell heavy and nonflexible. In contrast,
also suggests that no defects were introduced in GF during the
in our electrode, the 3D flexible and conductive interconnected
LTO synthesis process, guaranteeing a very high electrical con-
GF network acts not only as a highly conductive pathway for
ductivity of the GF. The above features of this 3D porous LTO/
electrons/lithium ions but also as an ultralight current collector
GF hybrid electrode produce a highly conductive pathway for
(down to ∼0.1 mg/cm2) (without

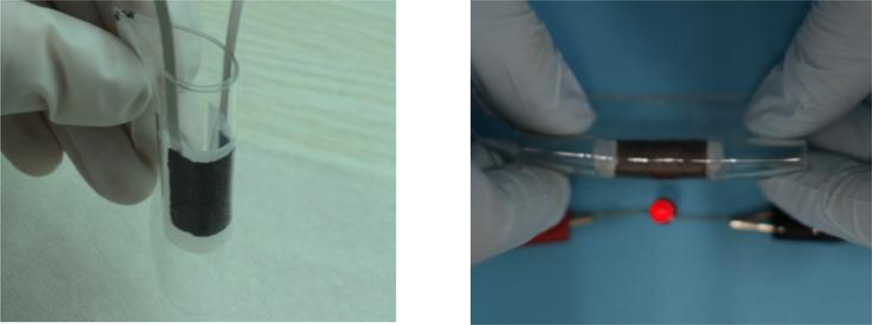
the use of conductive additives, binding agents, and metal cur-
than those of LFP/chemically derived graphene hybrid electro-
rent collectors. Impedance spectroscopy was used to characterize
des integrated with aluminum foil current collectors, carbon
the contact and charge-transfer resistance of the free-standing
black additive, and binder (27, 28). This high-rate performance is
LTO/GF electrode (The values of the
much better than that of a flexible LFP/multiwalled carbon
contact resistance Rs and charge-transfer resistance Rct of the
nanotube-yarn electrode, which only retained a capacity of ∼50
LTO/GF electrode were 6.6 and 67.1 Ω, respectively, which are
mAh/g at a 10-C rate (12). Furthermore, at a 10-C charge/dis-
significantly lower than those of the reference LTO coated on an
charge rate, 98% capacity retention was obtained after 500 cycles
aluminum current collector (11.7 and 112.1 Ω)
for the LFP/GF electrode (It should be
). These results confirm that the GF could not only
pointed out that Huang and coworkers (29) recently used a gra-
preserve the high conductivity of the overall electrode, but also
phene network to improve the rate performance of a LFP cathode.
largely improve the electrochemical activity of LTO during the
Different from our preparation process, their LFP/graphene net-
work material was prepared by simply mixing a graphene networkwith a suspension of LFP powder by stirring. Moreover, a poly
Electrochemical Behavior of the LFP/GF Cathode. To assemble a fullLIB, we also fabricated a LFP/GF cathode, using a similar pro-
(vinyl difluoride) binder and acetylene black were used in the
cess for LTO/GF fabrication, to match the LTO/GF anode (
fabrication of the LFP/graphene network electrode by magnetic
Similar to the LTO/GF anode, this
stirring. This LFP/graphene electrode showed a moderate-rate
LFP/GF cathode is very flexible and shows excellent cyclic sta-
performance similar to LFP/chemically derived graphene electro-
bility at both a low rate of 0.5 C and a high rate of 10 C (
des (27, 28), possibly because the graphene conductive network
), which further proves the impor-
may be broken during the stirring process, resulting in damage to
tance of the 3D conductive interconnected GF network, as well
the unique structure and degradation in the properties of the GFs.
as the good contact and strong binding between LFP and the GF.
It is worth pointing out that the charge/discharge curve of the
The specific capacity of the LFP/GF electrode at a 50-C dis-
pristine GF () shows a long, flat potential
charge rate is 98 mAh/g which is higher
plateau at about 0.2 V, which means that lithium ions can
V vs.
l (
ia 1.5
Capacity (mAh/g)
Coulombic Efficiency
Characterization of a thin, lightweight, and flexible LTO/GF//LFP/GF full battery. (A) Photograph of a bent battery encapsulated by PDMS, showing its
good flexibility. (B) Lighting a red LED device under bending. (C) Galvanostatic charging/discharging curves of the battery. Red and blue lines represent the as-fabricated flat battery and the bent battery after repeatedly bending to a radius of 5 mm 20 times, respectively. (D) Cyclic performance of the battery under
flat and bent states.
PNAS October 23, 2012 vol. 109 no. 43 17363
V vs. Li( 1.5
Capacity (mAh/g)
Capacity (mAh/g)
Rate and cyclic performance of a flexible LTO/GF//LFP/GF full battery. (A) Charging/discharging voltage curves of the battery with different current
rates. (B) Capacity of the battery charged/discharged at a constant 10-C rate for 100 cycles.
intercalate into GF below 0.2 V. However, the voltage windows
battery being bent decreased less than 1% compared with that of
used for the LTO/GF and LFP/GF in this work are 0.8–2.5 V and
the original flat battery (Fig. 4C). Moreover, the flexible battery
2.5–4.2 V, respectively. Therefore, these high-voltage windows
showed an excellent cyclic stability both under flat and bent
prevent lithium intercalation in GF.
states. For example, with respect to the original capacity, the
flexible battery showed a capacity retention of ∼97% after the
Assembling and Electrochemical Behavior of a Flexible Full Battery.
first 15 cycles under a flat state, and ∼95% after another 15
The voltage profiles of the LTO/GF and LFP/GF electrodes
cycles under a bent state (a bend radius of 5 mm) (Fig. 4D).
were investigated before assembling a full battery
The high-rate performance of the flexible battery was further
and no significant overpotential was observed. The
investigated. Fig. 5 shows the insertion/extraction capacity of
LTO/GF and LFP/GF electrodes showed initial discharge ca-
a flexible battery tested at different charge/discharge rates. It
pacities of 170 mAh/g and 164 mAh/g at 0.2 C, respectively.
should be noted that the rate capability of a LTO/LFP full bat-
These results indicate that the LTO/GF is a good match with the
tery is limited by the cathode material, and it is lower than that of
LFP/GF for assembling a full battery. Using the flexible LFP/GF
a half cell ). This flexible full battery can
cathode and LTO/GF anode, we then built a thin, lightweight,
be operated at a 10-C rate with a capacity of 117 mAh/g (Fig.
and flexible LTO/GF//LFP/GF full battery. The free-standing
5A), 88% of the capacity at a 1-C rate, which surpasses most full
LTO/GF and LFP/GF electrodes with a thickness of ∼100 μm
batteries reported (30–32) despite the fact that they are all based
were first laminated onto both sides of a polypropylene separator
on a conventional, nonflexible electrode package integrated with
and then sealed with ∼250-μm-thick poly (dimethyl siloxane)
metal foil current collectors, carbon black additive, and binder,
(PDMS) in an Ar-filled glove box using LiPF6 in ethylene car-
because the fast charge/discharge performance of a flexible full
bonate/dimethyl carbonate as the electrolyte. The total thickness
battery has never been reported (6, 11, 13). Furthermore, our
of this flexible full battery is less than 800 μm. Due to the small
flexible full battery can be cycled over 100 cycles at a high rate of
thickness and great flexibility of the GF-based electrodes (Fig.
10 C with only 4% capacity loss (Fig. 5B). Such a high-rate, long-
2A), the full battery shows excellent flexibility, and no structural
life performance for this flexible LTO/GF//LFP/GF battery, to
failure was observed after repeatedly bending to a radius of <5 mm
our knowledge, has never been reached before.
(Fig. 4A). This flexible battery is able to power a red light-emittingdiode (LED) when bent, as shown in Fig. 4B. As expected from
the operating voltages of the LTO/GF and LFP/GF, their com-
In this work, we have demonstrated a thin, lightweight, and
bination produces a battery with an operating voltage of 1.9 V, and
flexible LIB using a 3D flexible and conductive interconnected
the initial discharge capacity of the battery is ∼143 mAh/g with a
GF network as both a highly conductive pathway for electrons/
Coulombic efficiency of 98% at a 0.2-C rate (Fig. 4C). In this full
lithium ions and light current collector. By using the flexible
battery, all of the inactive components (metal current collectors,
LTO/GF and LFP/GF as anode and cathode, respectively, a
conducting additives, and binders) are replaced by lightweight GF
flexible full battery was assembled. This battery has shown good
(nearly two orders of magnitude lighter in areal density and three
flexibility, high capacity, high rate, and long-life cyclic perfor-
orders of magnitude lighter in volume density than copper); our
mance even under repeated bending to a small radius of 5 mm.
flexible battery shows an energy density of ∼110 Wh/kg based
Our strategy is versatile and can be used to fabricate a broad
on the total mass of the LTO/GF anode and LFP/GF cathode. A
class of anode and cathode materials. Both the fabrication of GF
higher energy density can be obtained by using materials with
and subsequent filling and loading of active materials can be
a wider voltage window. Although the volume energy density of
easily scaled up, which opens up the possibility for large-scale
the LTO/GF//LFP/GF battery is not very high at low discharge
fabrication of flexible batteries with high capacity to power
rates, it becomes very good at high discharge rates compared with
flexible electronic devices that can be operated at a high power
the batteries not using GF, and it is possible to increase its energy
rate and fully charged in a very short time.
density. For example, the volume energy density of the battery canbe increased by increasing the thickness of active materials, im-
proving the assembly process, selecting better packaging materials,
Synthesis of LTO/GF. The GF was prepared as previously reported (19). LTO/GF
and controlling the thickness of the GF used. To further increase
was prepared as follows. Typically, 1.7 mL of 30% (wt/wt) hydrogen peroxide
the volume energy density of a flexible battery, one can deposit
was dispersed in 40 mL of 0.4 M LiOH, followed by the addition of 3 mmol oftitanium tetraisopropoxide [Ti-(OC
electrochemically active materials with extremely high energy
3H7)4]. After stirring for 1 h, a piece of GF
was soaked in the solution, which was then transferred to an 80-mL Teflon-
density, such as metal oxides and silicon.
lined stainless autoclave and held at 130 °C for 3–12 h before cooling to
We also investigated the effect of bending on the performance
room temperature. The GF loaded with LTO nanosheets was washed with
of the flexible battery. After 20 bends to a radius of 5 mm, only
deionized water and dried in an oven at 80 °C. Finally, the as-prepared
a negligible overpotential was observed, and the capacity of the
sample was heated in a muffle furnace at 550 °C for 6 h in argon. Reference
LTO powder was prepared under the same conditions but without the ad-
as the counter electrode, 1 M LiPF6 in ethylene carbonate and dimethyl
dition of GF to the reaction solution.
carbonate (1:1, vol/vol) as electrolyte, and Celgard 2400 polypropylene asseparator. The charge/discharge cycles were performed at different rates at
Synthesis of LFP/GF. In a typical synthesis process (33), 0.01 mol of lithium
room temperature. All tests on the free-standing LTO/GF and LFP/GF were
acetate hydrate (CH3COOLi·2H2O), iron(III) nitrate hydrate (Fe(NO3)30·9H2O),
performed without conventional metal current collectors, carbon black and
and ammonium dihydrogen phosphate (NH4H2PO4) were dissolved in 35 mL
binder. The reference LTO electrode was prepared by mixing the pure LTO
of distilled water; 2.5 mL of ethylene glycol was then added to the solution,
powder, carbon black (TIMCAL Super-P), and poly(vinyl difluoride) at
and a yellow suspension was obtained. A piece of GF was soaked in this
a weight ratio of 80:10:10. The mixture was pasted onto a pure aluminum
solution before being transferred to an 80-mL Teflon-lined autoclave. The
foil and then pressed and dried under vacuum at 120 °C for 12 h. Batteries
autoclave was sealed, kept at 180 °C for 6 h, and then cooled to room tem-perature. The GF covered with LFP nanoparticles was washed with deionized
were assembled in an argon-filled glove box with oxygen and water con-
water and dried in an oven at 80 °C. Finally, the as-prepared sample was
tents below 1 and 0.1 ppm, respectively. All of the capacities and C-rate
heated at 720 °C for 12 h under a hydrogen and argon (5:95 vol/vol) atmo-
currents in this work were calculated based on LTO and LFP active materials
(1 C corresponding to 175 mA/g and 170 mA/g for LTO and LFP, respectively).
The graphene content in LTO/GF and LFP/GF hybrid materials was esti-
For the full battery, the capacities and C-rate currents were calculated based
mated to be ∼12 wt%.
on the cathode active material (1 C corresponding to 145 mA/g).
PDMS gel was fabricated by vigorously mixing base/curing agents (Sylgard
Characterization. XRD patterns of samples were recorded on a Rigaku dif-
184; Dow Corning), followed by degassing in a vacuum oven for 30 min and
fractometer using Cu Kα irradiation. SEM and TEM images were obtained on
thermally curing at 80 °C for 4 h.
a FEI Nova NanoSEM 430 and Tecnai F20, respectively. Raman measurementswere performed on Jobin-Yvon LabRam HR 800 excited by a 632.8-nm laser.
ACKNOWLEDGMENTS. This work was supported by Ministry of Science andTechnology of China Grant 2012AA030303, National Natural Science Foun-
Electrochemical Measurements. For half cell tests of free-standing LTO/GF and
dation of China Grants 51172240, 50921004, and 50972147, and Chinese
LFP/GF, coin cells were fabricated. In both cases, a lithium metal foil was used
Academy of Sciences Grant KGZD-EW-303.
1. Rogers JA, Someya T, Huang YG (2010) Materials and mechanics for stretchable
18. Feckl JM, Fominykh K, Döblinger M, Fattakhova-Rohlfing D, Bein T (2012) Nanoscale
electronics. Science 327(5973):1603–1607.
porous framework of lithium titanate for ultrafast lithium insertion. Angew Chem Int
2. Nishide H, Oyaizu K (2008) Materials science. Toward flexible batteries. Science 319
Ed Engl 51(30):7459–7463.
19. Chen ZP, et al. (2011) Three-dimensional flexible and conductive interconnected
3. Tarascon JM, Armand M (2001) Issues and challenges facing rechargeable lithium
graphene networks grown by chemical vapour deposition. Nat Mater 10(6):424–428.
batteries. Nature 414(6861):359–367.
20. Nelson PA, Owen JR (2003) A high-performance supercapacitor/battery hybrid in-
4. Kang B, Ceder G (2009) Battery materials for ultrafast charging and discharging.
corporating templated mesoporous electrodes. J Electrochem Soc 150:A1313–A1317.
21. Aldon L, et al. (2004) Chemical and electrochemical Li-insertion into the Li4Ti5O12
5. Zhang HG, Yu XD, Braun PV (2011) Three-dimensional bicontinuous ultrafast-charge
spinel. Chem Mater 16:5721–5725.
and -discharge bulk battery electrodes. Nat Nanotechnol 6(5):277–281.
22. Lee YJ, et al. (2009) Fabricating genetically engineered high-power lithium-ion bat-
6. Pushparaj VL, et al. (2007) Flexible energy storage devices based on nanocomposite
teries using multiple virus genes. Science 324(5930):1051–1055.
paper. Proc Natl Acad Sci USA 104(34):13574–13577.
23. Luo JY, Xia YY (2007) Aqueous lithium-ion battery LiTi2(PO4)3/LiMn2O4 with high
7. Amatucci GG, Badway F, Du Pasquier A, Zheng T (2001) An asymmetric hybrid non-
power and energy densities as well as superior cycling stability. Adv Funct Mater 17:
aqueous energy storage cell. J Electrochem Soc 148:A930–A939.
8. Nam KT, et al. (2006) Virus-enabled synthesis and assembly of nanowires for lithium
24. Lee SW, et al. (2010) High-power lithium batteries from functionalized carbon-
ion battery electrodes. Science 312(5775):885–888.
nanotube electrodes. Nat Nanotechnol 5(7):531–537.
9. Liu B, et al. (2012) Hierarchical three-dimensional ZnCo₂O₄ nanowire arrays/carbon
25. Shin JY, Samuelis D, Maier J (2011) Sustained lithium-storage performance of hier-
cloth anodes for a novel class of high-performance flexible lithium-ion batteries.
archical, nanoporous anatase TiO
Nano Lett 12(6):3005–3011.
2 at high rates: emphasis on interfacial storage
phenomena. Adv Funct Mater 21:3464–3472.
10. Jia XL, et al. (2011) Direct growth of flexible LiMn2O4/CNT lithium-ion cathodes. Chem
26. Ergang NS, et al. (2006) Photonic crystal structures as a basis for a three-dimensionally
interpenetrating electrochemical-cell system. Adv Mater 18:1750–1753.
11. Hu LB, Wu H, La Mantia F, Yang Y, Cui Y (2010) Thin, flexible secondary Li-ion paper
27. Ding Y, et al. (2010) Preparation of nano-structured LiFePO
batteries. ACS Nano 4(10):5843–5848.
4/graphene composites by
co-precipitation method. Electrochem Commun 12:10–13.
12. Lima MD, et al. (2011) Biscrolling nanotube sheets and functional guests into yarns.
28. Zhou XF, Wang F, Zhu YM, Liu ZP (2011) Graphene modified LiFePO
13. Gwon H, et al. (2011) Flexible energy storage devices based on graphene paper.
terials for high power lithium ion batteries. J Mater Chem 21:3353–3358.
Energy Environ Sci 4:1277–1283.
29. Tang Y, Huang F, Bi H, Liu Z, Wan D (2012) Highly conductive three-dimensional
14. Taberna PL, Mitra S, Poizot P, Simon P, Tarascon JM (2006) High rate capabilities
graphene for enhancing the rate performance of LiFePO4 cathode. J Power Sources
3O4-based Cu nano-architectured electrodes for lithium-ion battery applications.
Nat Mater 5(7):567–573.
30. Jung HG, Jang MW, Hassoun J, Sun YK, Scrosati B (2011) A high-rate long-life Li4Ti5O12/
15. Kang KS, Meng YS, Bréger J, Grey CP, Ceder G (2006) Electrodes with high power and
Li[Ni0.45Co0.1Mn1.45]O4 lithium-ion battery. Nat Commun 2:516–520.
high capacity for rechargeable lithium batteries. Science 311(5763):977–980.
31. Hassoun J, Lee KS, Sun YK, Scrosati B (2011) An advanced lithium ion battery based on
16. Aricò AS, Bruce P, Scrosati B, Tarascon JM, van Schalkwijk W (2005) Nanostructured
high performance electrode materials. J Am Chem Soc 133(9):3139–3143.
materials for advanced energy conversion and storage devices. Nat Mater 4(5):
32. Zhu GN, et al. (2011) Carbon-coated nano-sized Li4Ti5O12 nanoporous micro-sphere as
anode material for high-rate lithium-ion batteries. Energy Environ Sci 4:4016–4022.
17. Lee S, Cho Y, Song H-K, Lee KT, Cho J (2012) Carbon-coated single-crystal LiMn
33. Sun CW, Rajasekhara S, Goodenough JB, Zhou F (2011) Monodisperse porous LiFePO
nanoparticle clusters as cathode material for high-energy and high-power lithium-ion
microspheres for a high power Li-ion battery cathode. J Am Chem Soc 133(7):
batteries. Angew Chem Int Ed 124:8878–8882.
PNAS October 23, 2012 vol. 109 no. 43 17365
Source: http://carbon.imr.ac.cn/file/Journal/2012/1369619910960.pdf
GUIDELINES FOR BERMUDA2011 GOVERNMENT OF BERMUDAMinistry of HealthDepartment of Health HYPERTENSION GUIDELINES FOR BERMUDA Government of Bermuda Ministry of Health Department of Health P.O. Box HM 1195, Hamilton HM EX Bermuda Hypertension Task Group Hypertension Task Group (2011) Hypertension Guidelines for Bermuda
AUTORESDepartamento de Control del Comité Aragonés de Agricultura Ecológica (CAAE).Departamento de Agricultura, Ganadería y Medio Ambiente Dirección General de Alimentación y Fomento Agroalimentario (SSA). LGM. FOTOGRAFíASDepartamento de Control del CAAE. Comisión Europea (nº 9, 18, 20, 21 y 23) DIRECCIÓN EDITORIALComité Aragonés de Agricultura Ecológica