Fullseguridad.net
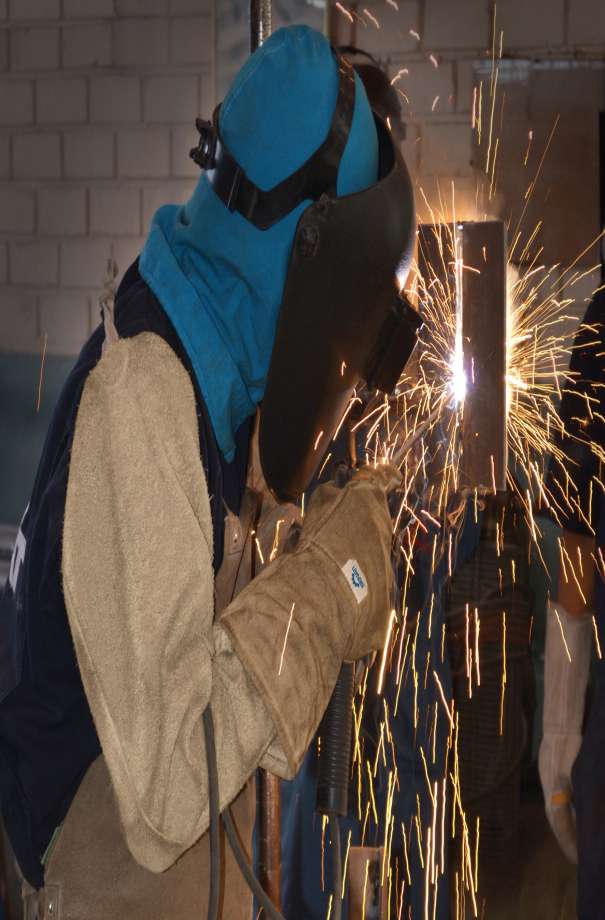
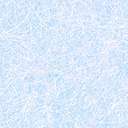
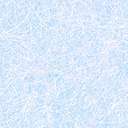
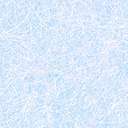
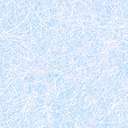
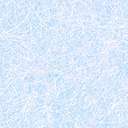
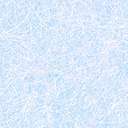
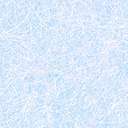
Seguridad e Higiene Industrial
SEGURIDAD INDUSTRIAL
[Guía del participante]
Técnico Nivel Operativo
Senati virtu@l
Seguridad e Higiene Industrial
Tabla de Contenido
Seguridad e Higiene Industrial
Seguridad e Higiene Industrial
La promulgación del Reglamento de la Ley Nº 29783, Ley de Seguridad y Salud en el Trabajo, en
el mes de Abril del presente año 2012, ha traído como consecuencia profundos cambios dentro del
campo de la Seguridad y la Salud en el Trabajo de las empresas, articulando un amplio abanico de
obligaciones y responsabilidades para el empresario en cuanto a la implementación de un sistema
de gestión orientado el desarrollo de una cultura preventiva en materia de seguridad.
El Reglamento de la Ley plantea en su artículo 27, garantizar que los trabajadores sean capaci-
tados en materia de prevención en relación con las capacidades o competencias necesarias para
el desarrollo de las actividades laborales en forma segura, y es en este sentido que el SENATI
consciente de su rol en el marco de la formación profesional, busca que reforzar la capacitación en
temas de SEGURIDAD en el semestre de su formación Básica.
El curso que presentamos, ha sido diseñado y elaborado tomando como fuente de información
diferentes instituciones y consultoras en materia de SEGURIDAD tratando de incluir conceptos y
experiencias de fácil entendimiento y aplicación por parte de nuestros aprendices. Igualmente se
a ordenado el contenido buscando una secuencia lógica y pedagógica que asegure el logro de los
objetivos previstos.
A través de este curso se pretenden cubrir los conocimientos básicos de SEGURIDAD de nues-
tros jóvenes aprendices antes de iniciar su formación práctica en la empresa. Contiene temas
orientados tanto a la acción preventiva, como a los aspectos técnicos básicos sobre gestión de la
prevención de riesgos laborales a los cuales estará expuesto el Aprendiz durante su permanencia
Para finalizar solo queremos recordar el carácter dinámico que tiene el presente curso. Su conte-
nido y estructura, están sujetos a todas aquellas aportaciones y sugerencias que nos hagan llegar
fruto de la aplicación en la práctica, lo que, sin duda, servirá para mejorar la calidad del mismo.
Esperamos que el curso sea una herramienta útil para todos ustedes estimados colegas y aprendi-
ces, en busca de difundir y alcanzar una cultura de prevención que redunde en beneficio de todos
los trabajadores y ayude a fortalecer la presencia y la intervención de ustedes en el campo de la
Seguridad y Salud en el Trabajo.
Seguridad e Higiene Industrial
LEGISLACIÓN SOBRE SEGURIDAD EN EL PERÚ
Recientemente en el mes de Abril del presente año se ha promulgado el Reglamento de la Ley
Nº 29783, Ley de Seguridad y Salud en el Trabajo, Decreto Supremo Nº 005 -2012 – TR donde
contiene todos los dispositivos legales vigentes en materia de Seguridad teniendo como principal
objetivo promover una cultura de prevención de riesgos laborales en nuestro país sobre la base de
la observancia del deber de prevención de las empresas, el rol de fiscalización y control del Estado
y la participación activa de los trabajadores.
Cuando la presente norma haga mención a la Ley, se entiende referida a la Ley Nº 29783, Ley de
Seguridad y Salud en el Trabajo.
Articulo 2.- En aplicación del principio de prevención, se entienden incluidos dentro del ámbito de
aplicación, a toda persona bajo modalidad formativa y a los trabajadores autónomos. También se
incluye a todo aquel que, sin prestar servicios se encuentre dentro del lugar de trabajo, en lo que
les resulte aplicable.
CONCEPTO DE LA SEGURIDAD INDUSTRIAL.
«Se entiende por Seguridad Industrial, al conjunto de normas y medidas técnicas destinadas a
preservar tanto la vida como la integridad física de los trabajadores y a mantener los materiales,
maquinarias, equipos e instalaciones en las mejores condiciones de operatividad y productividad».
La seguridad supone un proceso, por medio del cual se ejecutan actividades laborales en un am-
biente de trabajo con riesgos controlados, evitando causar lesión física o mental a la persona y sin
dañar las instalaciones donde se realizan.
La prevención de accidentes es tarea y esfuerzo común del Estado, la
Empresa y los Trabajadores.
La seguridad debe ser aplicada no sólo en la Empresa, sino en otros
lugares como e! hogar, las diversiones, actividades sociales etc.
Seguridad e Higiene Industrial
Implementación del sistema de gestión de seguridad y salud en el trabajo
ALCANCES DE LA SEGURIDAD INDUSTRIAL.
Los alcances de la Seguridad Industrial son mucho más amplios que los que hasta el momento
hemos relacionado con el trabajo.
Si en el trabajo nos habituamos a prevenir los riesgos, a acatar las normas y disposiciones que
reglamentan nuestra seguridad y sobre todo, a detectar condiciones peligrosas, estas mismas
actitudes y aptitudes, cultivadas y desarrolladas, pueden ser útiles en cualquier lugar donde nos
En el lugar que habitemos y en la actividad que realicemos, se pueden presentar oportunidades
en las que podemos aplicar los principios de seguridad industrial. Por ejemplo:
a. En el hogar.- Aplicando las normas de seguridad que se imparten en el trabajo o taller, y
haciéndolas extensivas a los miembros de la familia.
b. En la calle.- Respetando las reglas de tránsito e instruyendo a los nuestros para prevenirles
de los riesgos que se suscitan en la calle.
c. En las diversiones.- Observando prudencia y control ante cualquier acontecimiento
imprevisto que se presente.
EL TRABAJADOR Y LA SEGURIDAD INDUSTRIAL.
Cuanto más se sabe acerca de la seguridad, tanto más segura es la forma de actuar. Los métodos y
técnicas de seguridad se han creado para alcanzar resultados positivos. Se dispone de conocimien-
tos respecto a cómo alcanzar y mantener una actuación máxima en seguridad. El entrenamiento
en prácticas seguras de trabajo es factor esencial para una perfecta conducción del trabajador en
Seguridad e Higiene Industrial
La responsabilidad de! trabajador para evitar accidentes, no termina en el taller. Esta
responsabilidad se protege fuera del trabajo, en la calle, en e! hogar y en sus actividades
Observando las reglas y normas de seguridad, el trabajador evita accidentes y lesiones persona-
les, y la pérdida temporal o permanente del salario que amenaza al bienestar y la seguridad de su
Pero no solamente observando las reglas, sino también usando adecuadamente los equipos de
protección personal.
La seguridad es una parte esencial de la producción. Un trabajo hecho con seguridad es la clave
para producir con calidad.
Todo programa fructífero de seguridad exige la colaboración, es decir, el trabajo en equipo, el interés
y el entusiasmo por parte del trabajador.
En resumen la Seguridad Industrial y la prevención
de los accidentes es parte inherente al trabajo
mismo, por lo que el trabajador constituye el eje
de esta seguridad. El éxito de su trabajo
dependerá del grado como aplique las normas y
principios de la prevención de accidentes, riesgos
y peligros en la industria y en el lugar donde se
Luego de esta introducción y visión panorámica de
la Seguridad Industrial, los próximos capítulos del
curso nos darán una visión más clara del qué, el
por qué, y el para qué de la Seguridad Industrial.
En él veremos que los accidentes no son casuales,
Seguridad e Higiene Industrial
SISTEMAS DE GESTIÓN DE SEGURIDAD Y SALUD EN EL TRABAJO
PROGRAMA DE SEGURIDAD Y SALUD EN EL TRABAJO.
Mediante un Programa de Seguridad y Salud en el Trabajo se establecen las actividades y
responsabilidades con la finalidad de prevenir accidentes de trabajo, enfermedades profesionales y
proteger la salud de los trabajadores durante el desarrollo de las operaciones de la empresa. El
alcance se extiende a contratista y otros. Deberá ser revisada por lo menos una vez al año.
Aspectos que deberá comprender un programa:
OBJETIVOS DEL PROGRAMA DE SEGURIDAD Y SALUD.
• Objetivos generales y las metas a establecer anualmente. • Objetivos específicos.
ALCANCE DEL PROGRAMA.
• Establecer el alcance del Programa en cuanto al personal, procesos, instalaciones.
IDENTIFICACIÓN Y DETERMINACIÓN DE RIESGOS.
• Evaluar las operaciones, procedimientos, instalaciones y equipo para identificar riesgos. • Monitorear los niveles de exposición. • Desarrollar inspecciones periódicas de seguridad y salud. • Determinar si los controles administrativos, de ingeniería o el equipo de protección personal debe
CONTROL Y ELIMINACIÓN DE RIESGOS.
• Asegurar que las maquinas y herramientas estén funcionando de manera segura y en cumplimiento
con las normas correspondientes.
• Establecer controles de ingeniería y prácticas de trabajo para eliminar los riesgos. • Llevar a cabo trabajos de limpieza para eliminar los riesgos que pueden atribuirse a residuos,
desechos y escombros en las áreas de trabajo.
• Proporcionar equipos de protección personal adecuados cuando otros controles no son viables. • Garantizar medios de salida seguros.
PLANIFICACIÓN DE RESPUESTA A EMERGENCIAS.
• Desarrollar planes de respuestas a emergencias. • Desarrollar prácticas y simulacros de emergencia.
Seguridad e Higiene Industrial
ATENCIÓN MÉDICAS Y PRIMEROS AUXILIOS.
• Proveer servicios médicos, tratamiento de primeros auxilios y suministros. • Garantizar la disponibilidad del rescate de emergencia para los trabajadores lesionados. • Tener identificados y accesibles los números de teléfonos de emergencia de médicos, hospitales y
• Adiestrar a los trabajadores en el reconocimiento de riesgos. • Adiestrar a los trabajadores a reconocer y evitar las condiciones sub estándares. • Proporcionar adiestramiento sobre los procedimientos de trabajo. • Capacitación en relación a los riesgos específicos de los procesos.
MANTENIMIENTO DE REGISTROS.
• Mantener registro de todas las actividades del programa de seguridad y salud en el trabajo.
Seguridad e Higiene Industrial
IDENTIFICACIÓN DE PELIGROS Y EVALUACIÓN DE RIESGOS LABORALES.
IDENTIFICACIÓN DEL PELIGRO.
Constituye una herramienta importante del sistema de gestión, la cual permite conocer en los
diferentes procesos, las condiciones o situaciones que pueden causar lesiones y enfermedades a
las personas; así como otros daños.
EVALUACIÓN DEL RIESGO.
Es una herramienta de planificación del sistema de gestión, debido a que priorizar los riesgos de
acuerdo a un nivel de criticidad establecido. Las acciones preventivas se desarrollan en función de
los riesgos priorizados.
El riesgo se evalúa en función de la Probabilidad de que ocurra el daño y las Consecuencias del
Para establecer el Nivel de Probabilidad (NP) del daño se debe tener en cuenta el nivel de deficien-
cia detectado y si las medidas de control son adecuadas según la escala.
El daño ocurrirá raras veces.
El daño ocurrirá en algunas ocasiones.
El daño ocurrirá siempre o casi siempre.
Para determinar el Nivel de las Consecuencias previsibles (NC) deben considerarse la naturaleza
del daño y las partes del cuerpo afectadas según:
• Lesión sin incapacidad: pequeños cortes o magulladuras,
LIGERAMENTE DAÑINO
irritación de los ojos por polvo.
• Molestias e incomodidades: dolor de cabeza disconfort.
• Lesión con incapacidad temporal: fracturas menores.
• Daño a la salud reversible; sordera, dermatitis, asma,
trastornos músculo-esqueléticos.
• Lesión con incapacidad permanente: amputación,
fracturas mayores. Muerte.
• Daño a la salud irreversible: intoxicaciones, lesiones
múltiples, lesiones fetales.
El Nivel de Exposición (NE), es una medida de frecuencia con la que se da la exposición al riesgo.
Habitualmente vendrá dado por el tiempo de permanencia en áreas de trabajo, tiempo de
operaciones o tareas, de contacto con quinas, herramientas, etc. Este nivel de exposición se
presentará según:
Seguridad e Higiene Industrial
• Alguna vez en su jornada laboral y con periodo corto de
• Al menos una vez al año.
• Varias veces en su jornada laboral aunque sea con tiem-
• Al menos una vez al mes.
• Continuamente o varias veces en su jornada con tiempo
• Al menos una vez al día.
El Nivel de Riesgo se determinara combinando la probabilidad con la consecuencia del daño, según
LIGERAMENTE
VALORACIÓN DEL RIESGO, con el valor del riesgo obtenido y comparándolo con el valor
tolerable, se emite un juicio sobre la tolerabilidad del riesgo en cuestión.
INTERPRETACIÓN / SIGNIFICADO
Intolerable
No se debe comenzar, ni continuar el trabajo hasta que se
reduzca el riesgo.
• Si no es posible reducir el riesgo, incluso con recursos
ilimitados, debe producirse el trabajo.
• No debe comenzarse el trabajo hasta que se haya reducido
Importante
el riesgo. Puede que se precisen recursos considerables para
controlar el riesgo. Cuando el riesgo corresponda a un trabajo que se está realizando, debe remediarse el problema en un tiempo inferior al de los riesgos moderados.
Seguridad e Higiene Industrial
• Se deben hacer esfuerzos para reducir el riesgo, determinado
las inversiones precisas. Las medidas para reducir el riesgo
Moderado
deben implantarse en un periodo determinado.
• Cuando el riesgo moderado está asociado con consecuencias
extremadamente dañinas (mortal o muy graves), se precisará una acción posterior para establecer, con más precisión, la probabilidad de daño como base determinar la necesidad de mejora de las medidas de control.
• No se necesita mejorar la acción preventiva. Sin embargo se
Tolerable
deben considerar soluciones más rentables o mejoras que no
supongan una carga económica importante.
• Se requieren comprobaciones periódicas para asegurar que se
mantiene la eficacia de las medidas de control.
• No se necesita adoptar ninguna acción.
Seguridad e Higiene Industrial
Seguridad e Higiene Industrial
TABLA DE ACCIONES CORRECTIVAS
Acción Correctiva
Desarrollar / mejorar / corregir un programa: inspecciones
planeadas, orden y limpieza, observaciones planeadas, de
emergencia, equipos de protección personal, control de salud, otros.
Establecer / revisar el procedimiento de trabajo / tarea estándar.
Adecuarse a la normativa legal: nacional o internacional.
Capacitación / entrenamiento / reentrenamiento individual.
Capacitación / entrenamiento / reentrenamiento grupal.
Establecer sistema de señalización / señales de: advertencia,
obligatoriedad, información, prohibición, señales de tránsito, carteles, otros.
Mejorar selección / asignación de personal.
Entregar / seleccionar / utilizar equipos de protección personal
adecuados a la tarea.
Cambiar de puesto / sancionar personal.
Mejorar el diseño de equipos / maquinarias / lugar de trabajo.
Instalar / adecuar guardas o accesorios de seguridad.
Entrenamiento en primeros auxilios.
Mejorar el orden y la limpieza en el lugar de trabajo.
Eliminar / reducir / controlar las condiciones ambientales peligrosas:
ruido, radiación, alta-baja temperatura, gases, polvos, humos, vapores.
Eliminar / reducir / controlar condiciones ergonómicas deficientes:
cargas, posturas, movimiento repetitivo, espacio de trabajo reducido, iluminación deficiente, mobiliario inadecuado, otras.
Eliminar / reducir / controlar defectos físicos peligrosos: filoso,
puntiagudo, carcomido, roto, agrietado, otros.
Eliminar / reducir / controlar condiciones de almacenamiento
Seguridad e Higiene Industrial
Acción Correctiva
Eliminar / reducir / controlar peligros eléctricos (sin línea a tierra,
sin aislamiento, conexiones no cubiertas, etc).
Eliminar / cambiar / reforzar herramientas manuales o eléctricas
Eliminar / cambiar material, equipo inadecuado.
Eliminar / reducir / controlar condiciones que podrían generar
explosión o incendio.
Seleccionar / utilizar herramienta, equipo, material adecuado.
Establecer / cumplir con el Programa de Mantenimiento Preventivo
a equipos, máquinas, instalaciones, herramientas.
Otras medidas correctivas.
Seguridad e Higiene Industrial
IMPLEMENTACIÓN DEL MAPA DE RIESGOS
CONTENIDO
El proceso de implementación
III.1. Elaboración de la Matriz de riesgos III.2. Elaboración del Mapa de Riesgos
IV. Bibliografía V.
El termino Mapa de riesgos tiene su origen en Italia, entre 1960 y 1970, como parte de la estrategia
adoptada por los sindicatos italianos, en defensa de la salud laboral de la población trabajadora.
El Mapa de Riesgos es una herramienta necesaria para localizar, controlar, seguir y representar
en forma gráfica, los agentes generadores de riesgos que ocasionan accidentes o enfermedades
profesionales en el trabajo.
Así esta herramienta nos permite sistematizar y adecuar los riesgos existentes para crear y
mantener ambientes y condiciones de trabajo, que contribuyan a la preservación de la salud de
los trabajadores, y al mejor desenvolvimiento de ellos en su correspondiente labor.
Este documento ha sido elaborado como un resumen ejecutivo de ayuda rápida o guía para
implementación de este requisito y no reemplaza las recomendaciones que un experto puede
ofrecer en este tema.
Cualquier condición o práctica en cualquier lugar de empleo cuya naturaleza representa un peligro
inmediato que se espera pueda causar la muerte o una lesión física grave o donde la posibilidad
inminente de dicho peligro puede eliminarse mediante los procedimientos de aplicación que de otra
manera brinda esta Ley.
Seguridad e Higiene Industrial
RELACIÓN CAUSA EFECTO
Los peligros pueden clasificar según la fuente:
Es la combinación entre la probabilidad y consecuencias de la ocurrencia de un determinado
evento peligroso.
Si decimos expresiones como: el riesgo es mínimo, es porque lo asociamos al hecho de que la
posibilidad o probabilidad de ocurrencia de un accidente es también mínimo.
Es la posibilidad de que la exposición al factor de riesgo, genere en el tiempo consecuencias no
deseadas dichas probabilidad está directamente relacionada con los controles que la empresa
haya establecido para minimizar o eliminar el riesgo.
El daño puede ocurrir rara vez.
El daño puede ocurrir algunas veces.
El baño puede ocurrir siempre.
Severidad
Lesiones superficiales de poca gravedad, no incapacitantes o con incapacidad menores.
Seguridad e Higiene Industrial
Todas las enfermedades no mortales,
torceduras, quemaduras de segundo
golpes severos, fracturas menores.
Enfermedad profesional grave, progresiva, y/o mental,
amputaciones, etc.
MARCO LEGAL.
La base legal para la implementación del Mapa de Riesgos para las empresas no incluidas en el
grupo de alto riesgo, está en la promulgación del Decreto Supremo 009-2005-TR, publicado el 30
de septiembre del 2005 vigente a partir del 30 de Marzo del 2007.
Es obligación del empleador elaborar el Mapa de Riesgos, como medida de identificación y control
de la seguridad y la salud y publicado en un lugar visible de forma que sea visible a todos los
Artículo 25°: Para mejorar el conocimiento sobre la seguridad y salud en el trabajo, el empleador
deberá:
Elaborar un Mapa de Riesgos del centro de trabajo y exhibirlo en un lugar visible.
Artículo 28°: Los objetos de la seguridad y salud en el trabajo deben centrarse en el logro de
resultados realistas y posibles de aplicar por la empresa. La gestión de los riesgos debe
comprender:
Medidas de identificación, prevención y control.
Artículo 35°: Las disposiciones adoptadas para la mejora continua del Sistema de Gestión de
SST, deben tener en cuenta:
Los resultados de las actividades de identificación de los peligros y evaluación de los
Artículo 47°: El empleador debe actualizar la evaluación de riesgos una vez al año como mínimo
o cuando cambien las condiciones de trabajo o se hayan producido daños a la salud y a la
Seguridad e Higiene Industrial
EL PROCESO DE IMPLEMENTACIÓN - ELABORACIÓN DE LA MATRIZ DE RIESGOS.
La Matriz de Riesgos es una herramienta para gestión de la salud y seguridad de nuestra empresa.
Brinda información básica para el análisis de salud y seguridad laboral y para la elaboración de
planes preventivos.
Debe consolidar la evaluación de riesgos y peligros y será la base para la confección del Mapa de
ELABORACIÓN DE LA MATRIZ DE RIESGOS.
La Matriz de Riesgos es una tabla que consigna una serie de variables que permiten evaluar áreas
y determinar de forma sencilla la criticidad de los riesgos, dentro de la empresa.
Existen muchos modelos de Matriz de Riesgos disponibles en textos o en la web que pueden ser
En este instructivo usaremos un formato de matriz de Riesgos muy sencillo, fácil de entender (ver
Anexo N°1) y que puede adaptarse a las necesidades o exigencias de la empresa.
Paso 1: Seleccionar el área a evaluar. Ejemplo: El taller.
Paso 2: Consignar los datos de referencia (Empresa, evaluador, fecha, etc.) de la evaluación en
la matriz.
Paso 3: Inspeccionar el área física seleccionada e identificar los riesgos.
Paso 4: Llenar los 5 primeros campos en la matriz tomando un riesgo a la vez por cada fila del
formato. (ver Anexo N°2)
• Riesgos: Es el daño potencial que puede ocurrir por la realización de una tarea o labor. Ejemplo:
Disminución de la capacidad auditiva.
• Fuente de riesgo: Origen de los agentes físicos, químicos, biológicos y psicológicos o
condiciones que pueden ser causa de daño para la salud.
• Número de personas expuestas: Se refiere al número de trabajadores afectados o sujetos al
riesgo específico. Ejemplo: El taller tiene un total de 8 trabajadores y 5 laboran en la prensa. Por lo tanto el número de trabajadores expuesto a ruido es 5.
• Causa de la exposición:
Un Acto subestándar se refiere a un acto anormal que genera un riesgo innecesario y afecta
en forma directa la seguridad del sistema o proceso. Ejemplo: No usar casco en una área con
riesgo de caída de objetos.
Una Condición subestándar se refiere a la variación de las características físicas o al
Seguridad e Higiene Industrial
funcionamiento de los equipos, los materiales y/o el ambiente de trabajo y que causan anormalidades, constituyen condiciones de riesgo que pueden ser causa directa de accidentes operacionales. Ejemplo: Falta de guardas en un equipo con partes móviles que pueden causar atrapamientos.
TABLAS DE ACTOS Y CONDICIONES SUBESTÁNDARES
TABLA DE ACTOS SUBESTÁNDARES
Acto Subestándar
Realizar una tarea u operar equipos sin autorización.
No señalar o advertir.
Fallas en asegurar adecuadamente.
Operar a velocidad inadecuada.
Poner fuera de servicio / eliminar los dispositivos de seguridad.
No seguir el procedimiento de trabajo establecido.
Usar equipo / herramienta/ material inadecuado o defectuoso.
Usar los equipos / herramientas / material de manera incorrecta.
Emplear en forma inadecuada o no usar el equipo de protección
Instalar carga / almacenar de manera incorrecta.
Levantar objetos en forma incorrecta.
Adoptar una posición inadecuada para hacer la tarea.
Realizar mantenimiento de los equipos mientras se encuentran
Hacer bromas pesadas o jugar durante la ejecución de una tarea.
Trabajar bajo la influencia del alcohol y/o drogas.
Trabajar con condiciones físicas o fisiológicas inadecuadas y no
Otros actos subestándares .
TABLA DE CONDICIONES SUBESTANDARES
Condición Subestandar
No contar con protecciones y resguardos o que éstos sean
inadecuados o insuficientes.
No contar con equipos de protección personal / ropa o que éstos
sean inadecuados o insuficientes.
Seguridad e Higiene Industrial
No contar con herramientas, equipos o materiales o que estos sean
inadecuados / defectuosos.
Espacio limitado para desenvolverse.
No contar con sistemas de advertencia / señalización, o que estos
sean inadecuados o insuficientes.
Peligro de explosión o incendio.
Orden y limpieza deficientes en el lugar de trabajo
Condiciones ambientales peligrosas: gases, polvos, humos,
emanaciones metálicas, vapores, ruido, radiaciones, temperaturas
altas o bajas, iluminación excesiva o insuficiente, ventilación insuficiente, otros.
Falta de supervisión o que esta sea inadecuada / defectuosa.
Construcción / lugar de trabajo inadecuado.
Material / equipo, ubicado / apilado inadecuadamente.
Seguridad eléctrica inadecuada / insuficiente (sin línea a tierra, sin
aislamiento, conexiones no cubiertas, etc).
Inadecuados equipos de izaje.
Falta de equipos / implementos de emergencia / rescate.
Unidades de transporte en mal estado.
Terreno defectuoso.
Tráfico peligroso.
Peligros naturales
Otras condiciones subestándares.
Paso 5: Ponderar la Probabilidad y la Severidad de la potencial lesión o daño para la salud.
La ponderación de estas variables debe realizarse en base a una categorización de 3 niveles: B =
Bajo, M = Media o A = Alta, (ver Anexo N°3) la elección de la categoría para cada riesgo no es difícil,
aunque en algunos casos implica cierta experiencia y conocimiento.
Paso 6: Determinar la Criticidad, es calcular los niveles de riesgo a partir de la Probabilidad y
Severidad (consecuencia) asignada al riesgo.
Seguridad e Higiene Industrial
Se obtiene cruzando las coordenadas de las categorías asignadas a las variables probabilidad y
Severidad en la Matriz de criticidad de Riesgos (ver Anexo N°3). Esto permite determinar el nivel de
riesgo y la necesidad de intervención.
Paso 7: Implementar Medidas de Control. Una vez evaluados todos los riesgos debemos selec-
cionar los de mayor relevancia y plantear propuestas de mejora reales, aplicables y congruentes
con la realidad y la política de la empresa de forma que puedan realizarse y medirse en el tiempo.
ELABORACIÓN DEL MAPA DE RIESGOS.
Consiste plasmar la información compilada en la Matriz de Riesgos sobre un plano del ambiente
físicos de la empresa y ponerlo en un lugar que permita que los trabajadores puedan verlo y tenerlo
como referencia de los riesgos existentes en la empresa.
Se recomienda el dibujo de las instalaciones se diseñe en una escala de 1 en 100 y que se prepare
al menos uno y tenerlo como referencia de los riesgos existentes en la empresa.
Paso 1: Diseñar un mapa de las instalaciones en el que se distingan las características más impor-
tantes de la estructura y los equipos más importantes o generadores de riesgo. (ver Anexo N°4).
Paso 2: Señalizar mediante ícono (ver Anexo N°5) los riesgos existentes en cada área como se
puede observar en el Anexo N°6. El riesgos El reglamento de Seguridad y Salud en el Trabajo no
especifica no especifica la forma o íconos que deben usarse, nuestra recomendación es ceñirnos
a la Norma Técnica Peruana de señales, NTP399.010-1 2004.
Paso 3: Finalmente colocar el Mapa de Riesgos en un lugar visible y al alcance de todos los
Seguridad e Higiene Industrial
LOS ACCIDENTES.
CONCEPTO DE ACCIDENTE.
Accidente es un suceso inesperado que interfiere o interrumpe el proceso normal del trabajo.
El accidente puede afectar a:
Un accidente involucra algo más que lesiones.
a. LOS ACCIDENTES AFECTAN A LOS ELEMENTOS DE LA PRODUCCIÓN.
Todo accidente causa daño, cuando menos, a uno o más de los siguientes elementos de la
producción:
b. CUERPO DE TRABAJADORES.
Incluye a empleados, desde el peón hasta el ingeniero, así como a los empleados de oficina. Las
lesiones de cualesquiera de estas personas dan como resultado: costos médicos, indemnizacio-
nes, pérdidas de tiempo y de producción.
c. MAQUINARIA Y HERRAMIENTA.
Incluye la maquinaria para la producción, máquinas herramienta y maquinaria auxiliar, así como
cualquier otro implemento que se utilice en la instalación fabril. Los accidentes ocasionan daños
en la maquinaria y la herramienta, que elije reparación o sustitución inmediata. Entorpecen, a su
vez, el proceso de producción.
d. MATERIALES
Incluye materias primas, artículos en elaboración y productos acabados. Los accidentes inacti-
van temporalmente el desenvolvimiento de la producción.
Seguridad e Higiene Industrial
e. EQUIPO.
Incluye patios, edificios, instalación de energía eléctrica, ventilación, alumbrado, escaleras de
mano, recipientes para materiales en elaboración, mesas, sillas, material distinto de la maqui-
naria y herramientas de uso.
Los daños que se derivan de estos accidentes tienen como resultado mayores costos, así como entorpecimiento de la producción.
f. TIEMPO.
La pérdida de tiempo de producción es el resultado del daño ocasionado a maquinarias, herra-
mientas, materiales y equipos: también incluye la pérdida de tiempo de producción del empleado
accidentado.
El aumento de accidentes, disminuyen el volumen de producción
CAUSAS DE ACCIDENTES.
Rara vez un accidente obedece a una sola causa. Deben investigarse todos los accidentes de que se tenga noticia, y anotar las causas.
El accidente no implica necesariamente una lesión; pero toda lesión es producto de un accidente.
a. LESIÓN.
Es todo daño de orden físico que el accidente causa a las personas.
Ningún accidente es casual; los accidentes son causados.
Todo accidente tiene dos causas principales: la condición peligrosa y los actos inseguros.
CONDICIÓN SUBESTANDAR O PELIGROSA.-
Una de las causas de accidentes es ia condición o circunstancia física. Ejemplos: maquinaria con guardas inadecuadas y a veces sin ellas; herramientas o equipos defectuosos, su- perficies de trabajo desiguales, ventilación o alumbrado inadecuados.
ACTO SUBESTANDAR O INSEGURO.-
Otra causa de accidentes es la acción insegura, producida por una persona que puede ocasio- nar accidente o ser causa del mismo. Ejemplo: cargar, colocar o mezclar en postura o posición
Seguridad e Higiene Industrial
contraria a lo establecido por la seguridad; trabajar con equipos en movimiento; descuido al usar ropas inseguras o dispositivos de protección persona; hacer funcionar equipos a velocida- des contrarias a la seguridad; distracción, azuzamiento, etc.
b. LOS ACCIDENTES DE TRABAJO IMPLICAN DAÑOS A LOS SIGUIENTES
ELEMENTOS.
PERSONAL. Los accidentes de trabajo son el resultado de lesiones a los trabajadores son el
resultado de lesiones trabajadores. Algunos son por incapacidad; pero muchas son menores y
sin incapacidad. Generalmente se dispone de registros acerca de lesiones que reclamaron el
tratamiento debido.
MATERIALES. Por lo general los accidentes producen da-
ños materiales que no se denuncian. Son difíciles de descu-
brir, porque los trabajadores (y supervisores) tienden a no
dar mayor importancia o a "ocultar" sus resultados.
MAQUINARIA Y HERRAMIENTAS. A menos que el daño
de la maquinaría sea considerable, se pasa por alto el de-
nunciar este hecho.
EQUIPO. Los accidentes que afectan piezas de equipos no
se dan a conocer mayormente a salvo daños considerables
TIEMPO. Si lo afectado es el tiempo, se puede acumular
enormes cantidades de artículos en proceso de elaboración
o, de lo contrario, producir el estancamiento en la produc-
ción Se comprueba en la pila de desechos, el registro de
tiempo no activo y la pérdida de producción.
FACTORES DEL ACCIDENTE.
La investigación de los accidentes se lleva a cabo para determinar cuáles son los motivos y las condiciones que los originaron. Por lo general, las causas son una combinación de con- diciones y de actos peligrosos. Es muy raro que una condición peligrosa o un acto inseguro, solos, causen un accidente, pues bien, cuando se trata de localizar y corregir las causas de los accidentes, es necesario tener en cuenta los factores que han intervenido.
Las "Normas Norteamericanas" agrupan estos factores dentro de seis clasificaciones principales. 1. Agente 2. Parte del agente 3. Condición peligrosa 4. Tipo de accidente 5. Acto inseguro 6. Factor personal inseguro
Seguridad e Higiene Industrial
a. EL AGENTE es el objeto o sustancia relacionada directamente con la lesión.
Ejemplo:
• Máquinas
• Caídas de personas
• Motores y bombas
• Aparatos de transmisión y fuerza mecánica
• Aparatos de izar
• Herramientas
• Transportadores
• Vehículos
• Ascensores
• Sustancias explosivas e inflamables
• Sustancias tóxicas
• Polvillo
• Radiaciones
• Derrumbes
• Causas diversas
b. PARTE DEL AGENTE.
Es la parte especifica más relacionada directamente con la lesión, que debe corregirse y resguardarse apropiadamente. Por ejemplo, en un taladro, como parte del agente se consi- deran el mandril, la broca, el árbol, los engranajes, etc.
c. CONDICIÓN PELIGROSA.
Es la condición del agente seleccionado que pudo o debe protegerse, o, en su defecto, corregirse. Por ejemplo: • Agentes protegidos deficientemente. • Agentes defectuosos. • Arreglos o procedimiento peligroso en el agente, sobre, o cerca de él. • Iluminación inadecuada. • Ventilación deficiente. • Ropa insegura.
d. TIPO DE ACCIDENTE.
Es la forma de contacto de la persona lesionada con un objeto o sustancia.
• Golpeado contra. • Golpeado por. • Cogido en con o entre. • Caída a un mismo nivel. • Caída a diferente nivel. • Resbalón o sobresfuerzo. • Contacto con temperatura extrema. • Inhalación, absorción, ingestión. • Contacto con la corriente eléctrica.
ACTO INSEGURO.
• Si violentamos un procedimiento seguro, comúnmente aceptado, cuyo acto fue causa del
tipo de accidente, estamos frente a un acto peligroso. Ejemplo:
• Operar sin autorización.
Seguridad e Higiene Industrial
• Operar a velocidad insegura. • Anular los dispositivos de seguridad. • Uso de equipo inseguro. • Carga, colocación, mezcla, combinación u otras formas inseguras. • Trabajar en equipo o en movimiento peligrosos. • Distracción, juego, riñas, etc. • No usar equipo de segundad y/o dispositivos de seguridad personal.
e. FACTOR PERSONAL INSEGURO.
Es la acción mental o física que permite u ocasiona un acto inseguro. Existen 3 tipos de factores personales: a) Actitud impropia.- Desobediencia o no acatamiento, descuido, temperamento agresivo
nerviosidad, lesiones premeditadas, falta de comprensión de las instrucciones.
b) Falta de conocimiento o habilidad.- Ignorancia (inadvertencia o desconocimiento de las
prácticas de seguridad)
c) Impedimento físico.- Como dificultades en la visión u oído, debilidad muscular, fatiga, etc. d) Determinar las causas de los accidentes.es de importancia capital.
EJEMPLOS ILUSTRATIVOS
Reconozcamos, a través de los ejemplos, los factores que han inter- venido, para poder preveer accidentes, iguales o parecidos.
1. Un pintor de una compañía constructora cayó de una escalera, que
tenía un travesaño rajado. La escalera fue usada a pesar de las disposiciones. Al caer, el trabajador se fracturó una pierna y tuvo contusiones múltiples. Los factores seleccionados del accidente son:
2. Un pintor, como en el caso anterior, al precipitarse, cayó contra un
joven - aceitador novato que estaba lubricando el engranaje descubierto de un torno en funcionamiento.
El pintor, en este caso, no tuvo lesión alguna. En cambio, los dedos del aceitador fueron cogidos por el engranaje. En este supuesto accidente, hay dos agentes defectuosos: la escalera con el travesaño rajado y el tomo sin protección. Por tanto, los factores del accidente son:
De caerse el hombre de la escalera, hubiera resultado lesionado. Por consiguiente, debe tomarse en cuenta los factores contra accidentes.
Seguridad e Higiene Industrial
Tabla de Factores Personales y del Trabajo.
TABLA DE FACTORES PERSONALES.
Factores Personales
Factores Personales
Capacidad Física /
Estrés Mental o Psicológico
Fisiológica Inadecuada
Altura, peso, talla, fuerza,
Sobrecarga emocional.
alcance, etc. Inadecuados.
Fatiga debida a la carga o las
Capacidad de movimiento
limitaciones de tiempo de la
corporal limitada.
Capacidad limitada para
Obligaciones que exigen un
mantener en determinadas
juicio o toma de decisiones
posiciones corporales.
Rutina, monotonía,
Sensibilidad a ciertas
exigencias para un cargo sin
substancias o alergias.
Sensibilidad a determinados
Exigencia de una
extremos sensoriales
concentración / percepción
(temperatura sonido, etc.)
Actividades "insignificantes" o
Visión defectuosa.
Audición defectuosa.
Ordenes confusas.
Otras deficiencias
sensoriales (tacto, gusto,
Solicitudes conflictivas.
olfato, equilibrio).
Seguridad e Higiene Industrial
Factores Personales
Factores Personales
Preocupación debido a
Incapacidad respiratoria.
Otras incapacidades físicas
Incapacidades temporales.
Enfermedad mental.
Capacidad Mental /
Falta de Conocimiento
Psicológica Inadecuada
Temores y fobias.
Falta de experiencia.
Problemas emocionales.
Orientación deficiente.
Entrenamiento inicial
Enfermedad mental.
Nivel de inteligencia.
Reentrenamiento insuficiente.
Ordenes mal interpretadas.
Falta de juicio.
Falta de Habilidad
Escasa coordinación.
Instrucción inicial insuficiente.
Bajo tiempo de reacción.
Práctica insuficiente.
Aptitud mecánica deficiente.
Operación esporádica.
Baja aptitud de aprendizaje.
Falta de preparación.
Problemas de memoria.
Motivación Deficiente
Estrés Físico o
El desempeño Subestandar
es más gratificante.
El desempeño estándar causa
Lesión o enfermedad.
Fatiga debido a la carga o
Falta e incentivos.
duración de la tarea.
Fatiga debido a la falta de
Demasiadas frustraciones.
Fatiga debido a la
Falta de desafíos.
sobrecarga sensorial.
Seguridad e Higiene Industrial
Factores Personales
Factores Personales
Exposición a riesgos contra
No existe intención de ahorro
de tiempo y esfuerzo.
Exposición a temperaturas
No existe interés para evitar la
Insuficiencia de oxígeno.
Sin interés por sobresalir.
Variaciones en la presión
Presión indebida de los
Ejemplo deficiente por parte
Restricción de movimiento.
de la supervisión.
Retroalimentación deficiente
Azúcar en la sangre.
en relación al desempeño.
Falta de refuerzo positivo para
el comportamiento correcto.
Ingestión de drogas.
Falta de incentivos de
TABLA DE FACTORES DEL TRABAJO.
Factores Personales
Factores Personales
Supervisión y Liderazgo
Aspectos correctivos inapropiados
Deficientes
Relaciones jerárquicas poco
.comunicación de necesidades.
claras o conflictivas.
responsabilidades poco claras
.programación del trabajo.
Delegación insuficiente o
.revisión de las piezas.
Definir políticas,
procedimientos, prácticas o
.reemplazo de partes defectuosas.
línea de acción inadecuadas.
Formulación de objetivos,
metas o estándares que
Inadecuados
ocasionan conflictos.
Seguridad e Higiene Industrial
Factores Personales
Factores Personales
Programación o planificación
Evaluación deficiente de las
insuficiente del trabajo.
necesidades y los riesgos.
Preocupación deficiente en
Instrucción, orientación y/o
cuanto a los factores humanos /
entrenamiento insuficientes.
Entrega insuficiente de
Estándares o especificaciones
documentos de consulta, de
instrucciones y de guías.
Identificación y evaluación
Disponibilidad inadecuada de
deficiente de las exposiciones
equipos / herramientas / materiales.
Falta de conocimiento en
Ajustes / reparación /
el trabajo de supervisión /
mantenimiento deficientes.
administración.
Sistema deficiente de reparación /
Ubicación inadecuada del
recuperación de materiales.
trabajador, de acuerdo a sus
cualidades y a las exigencias
que demanda la tarea.
Eliminación y reemplazo
inapropiado de piezas defectuosas.
Estándares Deficientes de
deficientes del desempeño.
Retroalimentación deficiente
Desarrollo Inadecuado de normas
o incorrecta en relación al
.inventario y evaluación de las
Ingeniería Inadecuada
exposiciones y necesidades.
Evaluación insuficiente de las
.coordinación con quienes diseñan
exposiciones a pérdidas.
Preocupación deficiente en
cuanto a los factores humanos
.compromiso del trabajador.
Estándares, especificaciones
.estándares / procedimientos /
y/o criterios de diseño
reglas inconsistentes.
Seguridad e Higiene Industrial
Factores Personales
Factores Personales
Control e inspecciones
Comunicación inadecuada de las
inadecuados de las
Evaluación deficiente de la
condición conveniente para
Evaluación deficiente para el
comienzo de una operación.
Evaluación insuficiente
respecto a los cambios que se
Deficiencia en las
Especificaciones
.reforzamiento mediante afiches,
deficientes en cuanto a los
código de colores y ayudas para el
Investigación insuficiente
Mantenimiento inadecuado de las
respecto a los materiales y
Especificaciones deficientes
.seguimiento del flujo de trabajo.
para los vendedores.
Modalidad o ruta de embarque
.actualización.
Inspecciones de recepción y
.control del uso de normas /
aceptación deficientes.
procedimientos / reglamentos.
Comunicación inadecuada
de las informaciones sobre
Uso y Desgaste
aspectos de seguridad.
Manejo inadecuado de los
Planificación inadecuada del uso.
Almacenamiento inadecuado
Prolongación excesiva de la vida útil
de los materiales.
Transporte inadecuado de los
Inspección y/o control deficientes.
Identificación deficiente de los
Sobrecarga o proporción de uso
itemes que implican riesgos.
Seguridad e Higiene Industrial
Factores Personales
Factores Personales
Sistemas deficientes de
recuperación o de eliminación
Mantenimiento deficiente.
Empleo del elemento por personas
Mantenimiento Deficiente
no calificadas o sin preparación.
Aspectos preventivos
Empleo inadecuado para otros
inadecuados para:
.evaluación de necesidades.
Abuso o Maltrato
.lubricación y servicio.
intencional, no intencional.
No permitidos por la supervisión:
.ajuste / ensamblaje.
intencional, no intencional.
.limpieza o pulimiento.
CONSECUENCIA DE LOS ACCIDENTES.
a. CONSECUENCIAS PARA EL TRABAJADOR.
Según sea la gravedad del accidente, sufre las si-
guientes consecuencias:
• Pérdida parcial de su salario. Dolor físico, como
consecuencia de las lesiones
• Incapacidad parcial o permanente. • Reducción o nulidad de su potencial como trabajador. • Traumas psíquicos, derivados de las lesiones.
b. CONSECUENCIAS PARA LA FAMILIA
La familia queda afectada y perjudicada por:
Angustia al recibir la noticia Futuro incierto, por limitaciones económicas. Gastos extras, du-
rante recuperación del trabajador.
c. CONSECUENCIAS PARA LA EMPRESA
Pérdida económica, por costos derivados del accidente.
d. CONSECUENCIA PARA LA NACIÓN
Cada vez que se lesione o pierda la vida, un trabajador, por ser una persona que deja de pro-
ducir, la nación reduce sus ingresos.
Seguridad e Higiene Industrial
5. COSTO DE LOS ACCIDENTES
CONCEPTO DE COSTO DE ACCIDENTE.
Es el grado del daño a la maquinaria, materiales, equipo, tiempo y mano de obra perdidos en el proceso productivo.
SISTEMAS PARA DETERMINAR LOS COSTOS.
Entre los principales tenemos:
a) COSTOS DIRECTOS E INDIRECTOS.
Costo Directo: Incluye los costos médicos y por indemnización.
Costo Indirecto: Incluye los costos ocultos o intangibles. Son los menos aceptados. La proporción
entre costos directos e indirectos es de 4:1.
Los costos indirectos incluyen: • Costos de tiempo perdido por el trabajador. • Costos de tiempo perdido por otros trabajadores que suspenden su trabajo. • Por curiosidad. • Por compasión. • Por auxilios al trabajador lesionado. • Por averiguar la causa. • Por otros motivos, etc.
b) COSTOS ASEGURADOS Y NO ASEGURADOS
Costo asegurado: Incluye los gastos médicos, indemnización y gastos generales del seguro
(prima del seguro): equivale al costo directo.
Costo no asegurado: El número de casos con pérdida de tiempo, multiplicado por cada una de
Seguridad e Higiene Industrial
las categorías: equivale al costo indirecto.
c) COSTOS DE LOS ELEMENTOS DE LA PRODUCCIÓN
Se considera solamente los costos reales de importancia suficiente para que los acepte la Dirección. Es decir, se ocupa del costo de los accidentes por lesiones del personal trabajador, daños de maquinarias, equipo y materiales, así como la pérdida de tiempo en la producción.
Este último es el más preciso y sencillo por que proporciona exactitud para la estadística y el control. En este capítulo no utilizamos la terminología "costos directos" o "asegurados", "costos indirectos" o "no asegurados"; en lugar de ellos, empleamos cinco factores fundamentales de la producción, a saber:
• Mano de Obra.- Por mano de obra entendemos la actividad del trabajador en la instalación
fabril, incluyendo los trabajadores, oficinistas, ingenieros y demás empleados asalariados. Los accidentes que afectan a estas personas son el resultado del tiempo perdido en la pro- ducción, costos médicos e indemnizaciones.
• Maquinaria.- Incluye maquinaria para la producción, máquina-herramientas, maquinaria
auxiliar y herramientas de mano. Los accidentes que causan daño a las máquinas exigen reparación o sustitución, lo que permite, a su vez, interrumpir el avance de la producción.
• Materiales.- Son las materias primas, artículos en elaboración y productos acabados. Los
accidentes ocasionan daños materiales que reclaman pronta reparación o sustitución. Entorpecen asimismo, la producción con mayores costos.
• Equipo.- Los edificios, patios, instalación de energía eléctrica, equipo de ventilación y alum-
brado, escaleras de mano, recipientes para materiales de elaboración, mesas y sillas for- man el equipo físico distinto de la maquinaria, y constituye factor esencial para la operación de la instalación fabril. Los daños de accidentes por incendio y explosión, ocasionan may- ores costos y entorpecen la producción.
• Tiempo.- Es lo estimable en la producción y se pierde por lesiones de los tra-
bajadores, maquinarias, equipo y material dañados.
Todo accidente daña por lo menos, uno o más de los elementos de la producción. Un de- scenso del número de accidente afecta, a la postre, el costo unitario de producción.
d) DETERMINACIÓN DEL COSTO DE LOS ACCIDENTES.
1. Costos de Equipos.
Incluye:
• Costo de reparación del equipo que resultó dañado en el accidente.
• Costo de pérdida de tiempo de producción por el equipo dañado.
2. Costo Total de los accidentes.
COSTO PARA EL TRABAJADOR
Además del sufrimiento físico, el trabajador pierde dinero cuando ocurren accidentes con le- siones. La pérdida económica real del trabajador es elevado, en relación con su capacidad, para soportar la carga económica extra.
Seguridad e Higiene Industrial
Por lo general, el trabajador pierde la diferencia entre la paga por incapacidad física y su sueldo regular. Si la lesión le produce una incapacidad permanente, puede sufrir la pérdida continua de salario durante el resto de su vida. Si el trabajador se lesiona fuera del centro de labores, tendrá que pagar los gastos médicos y soportar la pérdida de su salario, si la lesión lo inhabilitara para siempre.
EFECTOS DE LOS ACCIDENTES EN LA PRODUCCIÓN
Seguridad e Higiene Industrial
Diez Reglas Básicas de Seguridad
¿POR QUE SE INSISTE T ANTO EN LA "PREVENCIÓN DE ACCIDENTES"?
• PORQUE su familia y los que dependen de usted aspiran cada día verlo llegar a la casa sano
y salvo de regreso del trabajo.
• PORQUE deseamos que usted reciba todos los beneficios que le proporcionan las medidas
de protección que adoptamos, como también los demás implementos que le demos para su salvaguarda.
• PORQUE las instrucciones de seguridad que se dan en los boletines y reuniones, son para
que usted, se proteja poniéndolas en práctica.
• PORQUE buscamos el bienestar de usted y los suyos. • PORQUE la mejor manera de trabajar es la más segura. • PORQUE u n bajo Índice de accidentes refleja un buen trabajador y un trabajo bien dirigi-
• PORQUE su ayuda es necesaria. • PORQUE deseamos que usted haga todo en forma correcta utilizando los implementos que
le proporcionamos.
• PORQUE usted debe evitar métodos inseguros, ello serán causa de accidentes tarde o tem-
• PORQUE nuestros capataces y empleados más antiguos le ayudarán gustosos en cualquier
momento, le contestarán cualquier pregunta.
• PORQUE no hay pregunta que se pueda llamar tonta" relacionada con la segundad. • PORQUE siempre recibiremos con gusto sus sugerencias sobre problemas de seguridad. • PORQUE siempre recibiremos con gusto sus sugerencias sobre problemas de seguridad. • PORQUE queremos estar orgullosos de nuestro índice de seguridad. • PORQUE usted debe ayudarnos a mantenerlo bajo o mejorar el índice de seguridad.
Seguridad e Higiene Industrial
LOS 10 MANDAMIENTOS DE SEGURIDAD.
He aquí 10 reglas para los supervisores en
la promoción de la seguridad. Las mismas
fueron preparadas por un supervisor, quien
mandamientos. No es una mala idea
tomar nota de ellas y ponerlas en práctica.
El Supervisor que nos la entregó dijo que
él probó cada una de ellas por separado,
en días especiales, sin olvidar las otras 9
mientras se concentraba en la regla
correspondiente al día.
• Entrenar al personal a trabajar con
• Vigilar y corregir inmediatamente las
condiciones inseguras de trabajo.
• Hacer que hayan equipos de segundad disponibles y que los mismos sean usados. • Conocer todos los malos hábitos de trabajo. • Mantener la disciplina esto es de extrema importancia en seguridad. • Mantener los lugares de trabajo limpios y libres de escombros. • Cerciorarse de que todas las herramientas estén en buenas condiciones. • Obtener la cooperación de todo el personal en la Prevención de Accidentes. • Dar el ejemplo personalmente. • Y nosotros nos permitimos agregar una regla más, para ser aplicada al mismo tiempo, junto
con las ya indicadas.
• Pensar. Pensar y actuar usando el sentido común.
LOS ACCIDENTES PUEDEN SER EMOCIONANTES
¿Está Usted cansado de todo? ¿Está Usted buscando nuevos horizontes? Tenga un accidente.
Los accidentes pueden abrirle un mundo nuevo e interesante. Conocerá lugares y experimentar
sensaciones nunca imaginables.
Conocerá hermosas enfermeras y médicos capaces. Tendrá oportunidad de conocer bien de cerca
como funciona el servicio de primeros auxilios, la sala de operaciones y ver como actúan los ciruja-
nos y otros especialistas.
Es probable que le quede una cicatriz que sirva como tema de conversación a donde quiera que
Seguridad e Higiene Industrial
Puede escribir un libro, que puede resultar el mejor vendido del año: "Como regresé al mundo de
los vivos" o "Como puede un lisiado aumentar sus ingresos.
Usted puede lograr que su nombre aparezca en los periódicos, incluso en primera plana. Puede
cobrar el seguro contra accidente, el cual estuvo pagando durante largo tiempo. Puede estar
acostado sentado en casa durante todo el día, leyendo los periódicos o escuchando rápido. Puede
lograr la simpatía que nunca hubiese obtenido, aún de la esposa y los niños. Su cuerpo recibirá
inyecciones de todo tipo y cuanta droga y estimulantes existan, es probable que su mujer tenga que
salir a trabajar y que su hijo mayor deba abandonar la escuela y adquirir una experiencia de la vida
Es posible que el médico deba ponerlo a régimen a fin de curarle algunos de sus viejos hábitos.
Puede que tenga que aprender un nuevo trabajo para reemplazar el antiguo que no podrá hacer
más, pero que de cualquier manera no le gustaba.
En consecuencia sea moderno. Tenga un accidente, la experiencia puede ser una buena muestra,
si sale con vida de ella.
Amigo Supervisor:
Recuerde que no basta que los trabajadores aprendan Normas de Seguridad, es necesario que és-
tas se conviertan en un hábito del trabajo diario.
Por lo tanto, no tema repetir una y otra vez de las mismas verdades, aunque si debe tratar de pre-
sentarlas cada vez de manera diferente.
Al enfocar un mismo tema desde distintos ángulos, los trabajadores lo asimilan mejor y se les graba
más en la mente.
La cuestión es machacar, para que los hábitos de seguridad formen parte de la conciencia del
PREVENCIÓN DE ACCIDENTES
La prevención de accidentes constituye un capítulo esencial en los objetivos de la Seguridad e
Higiene Industrial, en el proceso de la formación y adiestramiento. Cuando las condiciones de
seguridad se prevean, el trabajador cumple mejor las tareas y el rendimiento es mayor. La clave de
la prevención de accidentes se funda en identificar los peligros y evaluar los riesgos
oportunamente y eliminar y controlar aquello que pueda representar un riesgo en los lugares de
trabajo, mediante medidas de orden y limpieza, manejo de materiales, herramientas, protección de
máquinas, uso de equipos de protección personal, inspecciones, investigaciones, supervisiones,
A continuación, se presenta una serie de medidas, normas y reglas de prevención de accidentes.
Seguridad e Higiene Industrial
a. ORDEN Y LIMPIEZA.
El orden y cuidado incluyen, no solamente, la limpieza y el arreglo ordenado del taller y equipos,
sino la norma: "Un lugar para cada cosa y cada cosa en su lugar".
El orden y la limpieza de una fábrica son muy importantes en la prevención de accidentes, pues
• Un eficiente funcionamiento. • Una moral elevada en los trabajadores. • Buenas relaciones humanas.
¿Cuándo se dice que hay orden en un lugar?
"Cuando no hay objetos en los pasillos que obstruyen el paso, los materiales están correctamente
almacenados y las herramientas que no se usan, colocadas en estantes y ganchos".
b. USO DE SEÑALES PARA EL ORDEN Y CUIDADO
Parra lograr el orden y cuidado en el taller, en la fábrica se debe:
Pintar los pasillos. Las señales de los límites de los pasillos deben indicar claramente el espacio
que ha quedado destinado para el tránsito.
Marcar los lugares para almacenamiento. Para establecer
previamente cuales son los lugares de almacenamiento, se
les usará únicamente para este fin.
Marcar las herramientas. Pintándolas de colores. De esta
manera, podrán ser identificados por departamentos.
Identificar los botes de basura. Para indicar los diferentes
usos de los distintos recipientes, como botes de basura, por
ejemplo, puede emplearse distintos colores o diferentes
combinaciones de colores.
Usar colores claros. Para hacer más visible en las máquinas la
suciedad, el tizne, etc.
Seguridad e Higiene Industrial
IMPORTANCIA DE LA LIMPIEZA EN LA SEGURIDAD INDUSTRIAL
La limpieza de la planta es un aspecto muy importante del
plan de seguridad que toda empresa debe tener. No se trata
solamente de ofrecer a los trabajadores un lugar agradable
donde trabajar; en realidad, el propósito fundamental es pro-
teger la vida y la salud de los que allí laboran. Cuando un
área está limpia y ordenada, se puede trabajar con más se-
Los causantes principales de las caídas, son los
desperdicios que, a veces, se encuentran en todo taller,
chatarra, desperdicios y materiales en desuso, con
frecuencia llenan los pasillos y locales de trabajo y dificultan
el paso de un lu- gar a otro. También es necesario tener en
cuenta que pape- les, trapos impregnados de grasa, aserrín
o cualquier otra basura pueden producir incendios fácilmente.
No deben ignorarse la importancia de la limpieza. El personal de seguridad, por lo general, insiste
en este tema con mucha regularidad. Sin embargo, en algunos lugares todavía se tiene el concepto
de que la limpieza es algo que se hace cuando los operarios no tienen mucho trabajo. Hoy en día,
con la planificación laboral, los trabajadores siempre tienen algo que hacer y, por lo tanto, la limpie-
za debe estar incluida en el plan.
Es necesario tener en cuenta que hay una forma correcta y otra incorrecta de realizar la limpieza y
aseo del local de trabajo. Por eso, hay que poner énfasis en el hecho de que la gasolina NO es un
agente de limpieza que se deba utilizar, para quitar la grasa de las herramientas, los equipos, etc.
Una buena limpieza y un buen aseo son fundamentales para la seguridad y buena salud del traba-
PUNTOS QUE INDICAN QUE EL ORDEN Y LIMPIEZA SON DEFICIENTES
1. Objeto y materiales diseminados en el piso.-
Estos son pequeños. Por lo general son arrojados de las máquinas, de las cajas de herramientas o llevados de un lugar a otro.
2. Equipo fuera de lugar.-
Se refiere a objetos grandes como carretillas, escaleras, extintores de incendio y otros, cuya presencia se debe a la falta de un ordenamiento adecuado.
3. Mal apilamiento.-
Abarca cuestiones como:
Seguridad e Higiene Industrial
Apilamiento desordenado. Objetos depositados en los pasillos.
Rumas mal hechas o demasiado altas.
Amontonamiento de objetos que obstruyen puertas y escapes de emergencia.
4. Deficiencia eliminación de desechos.-
Se manifiesta por: Falta de recipientes para desperdicios y desechos. Falta de bandejas colectoras de escurrimientos, y eliminación de viruta y resortes.
5. Paredes, ventanas y lámparas sucias.-
El polvo acumulado en las ventanas, claraboyas y lámparas, disminuye la iluminación, aumenta el esfuerzo visual y, lógicamente, los riesgos de accidentes.
6. Riesgos de incendio.-
Los más comunes son: Basura. Trapos empapados en grasa y aceite.
Aceites y pinturas
Pilas de papel.
a. ALMACENAMIENTO DE MATERIALES.
1. ¿Están los materiales apilados propiamente y con seguridad? ¿ se guardan en lugares desig-
nados para tal fin ?¿Se usan envases resistentes y no se cargan demasiado?
2. ¿Las pilas dejan un espacio de 45 cm. por lo menos, debajo de los cabezales de los rociadores
3. ¿En lugares de trabajo, la congestión se mantienen al mínimo mediante un sistema regularizado
de entrega de materias primas y salida de productos acabados?
b. HERRAMIENTAS.
1. ¿Se tiene propiamente las herramientas y se las almacena listas para su uso?
2. ¿Se mantienen limpios y ordenados los cuartos de herramientas y arcones?
3. ¿Se conservan las herramientas manuales en gavetas, cajas de herramientas o en estantes
designados para tal fin?
c. PATIOS Y ALREDEDORES.
1. Se mantiene los patios limpios, sin desechos ni basuras?
2. ¿Está bien cuidado el césped, libre de malezas?
3. ¿Están bien marcados y se mantiene en buenas condiciones los caminos de acceso, las
4. ¿Se mantiene en buenas condiciones las cercas y el alumbrado de la propiedad?
Seguridad e Higiene Industrial
PREVENCIÓN DE CAÍDAS.
1. GENERALIDADES.
La caída de los trabajadores es una de las primeras causas de los accidentes de trabajo. Estos
riesgos implican una acción positiva en un programa de prevención, crean conciencia de necesidad
en el trabajador, de prestar atención a los riesgos que producen las caídas.
La importancia de conocer los agentes, las causas y fuentes relacionados con las caídas, nos
permiten tomar acciones de prevención.
Las investigaciones y estadísticas nos demuestran que un gran porcentaje de accidentes de trabajo
se producen por las caídas.
Los informes de accidentes indican que hay varias causas de caída, que en su mayor parte son
fáciles de descubrir: Resbalones. Tropiezos y traspiés. Pérdida de equilibrio o sostén. Falta de
2. CLASES DE CAÍDAS.
a. A UN MISMO NIVEL.
Son los más frecuentes y las menos graves; sin embargo, muchas de ellas pueden resultar accidentes graves, en especial sí la persona, al caer, se golpea sobre una esquina aguda. Entre las causas que originan estos accidentes, tenemos:
Pisos resbalosos: grasa o aceites, jabón, agua, rebabas metálicas, pisos encerados, losetas,
mármol, etc.
Obstrucciones: piezas de equipo, herramientas, repuestos, materiales fuera de lugar.
Superficies desiguales: remiendos defectuosos, desgaste, roturas o desgarramientos del piso.
Vibraciones: soportes inadecuados, maquinaria mal nivelada.
INVESTIGACIÓN DE ACCIDENTES DE TRABAJO
I. DEFINICIONES.
Accidente de Trabajo: Evento no deseado ocurrido a causa o con ocasión del trabajo que pro-
duce daño o lesión orgánica o perturbación funcional, y que es generada por acción imprevista,
fortuita u ocasional de una fuerza externa, repentina y violenta que obra súbitamente sobre la
persona o debida al esfuerzo del mismo.
Se considera igualmente accidente de trabajo: a) El que sobrevenga al trabajador durante la ejecución de órdenes de la Empresa o bajo su
autoridad, aún cuando se produzca fuera del centro y de las horas de trabajo.
Seguridad e Higiene Industrial
b) El que se produzca antes, durante o después de la jornada laboral o en las interrupciones
del trabajo; si el trabajador se hallara por razón de sus obligaciones laborales, en cualquier centro de trabajo de la Empresa, así no se encuentre realizando las actividades propias del riesgo contratado.
c) El que sobrevenga por acción de la Empresa o sus representantes o de tercera persona,
durante la ejecución del trabajo. No se consideran accidentes de trabajo:
d) El que se produce en el trayecto de ida y retorno al centro de trabajo, aunque el transporte
sea realizado por cuenta de la Empresa en vehículos propios o contratados para tal efecto;
e) El provocado intencionalmente por el propio trabajador o por su participación en riñas o pe-
leas u otra acción ilegal;
f) El que se produzca con ocasión de actividades recreativas, deportivas o culturales, aunque
se produzcan dentro de la jornada laboral o en el centro de trabajo;
g) El que sobrevenga como resultado de comer, beber o preparar comida o bebida para con-
h) El que sobrevenga durante los permisos, licencias, vacaciones o cualquier otra forma de
suspensión del contrato de trabajo estando el trabajador fuera o dentro de las instalaciones de la empresa;
i) Los que se produzcan como consecuencia del uso de sustancias alcohólicas o estupefacien-
tes por parte del trabajador;
a) Los que se produzcan en caso de guerra civil o internacional, declarada o no, dentro o fuera
del Perú, motín, conmoción contra el orden público o terrorismo;
b) Los que se produzcan por efecto de terremoto, maremoto, erupción volcánica o cualquier
otra convulsión de la naturaleza.
Accidente Grave o Incapacitante: aquel que, luego de la evaluación, el médico diagnostica y
define que el accidente no es trivial o leve y determina que continúe el tratamiento luego de las
24 horas de ocurrido el accidente.
Accidente Trivial o Leve: aquel que requiere tratamiento médico ambulatorio sin necesidad de
descanso médico o con descanso no mayor de 24 horas. Este tipo de accidente será reportado
a la autoridad en formatos especialmente preparados por la misma.
Accidente Fatal: aquel en el que el trabajador fallece como consecuencia de una lesión de
trabajo, sin tomar en cuenta el tiempo transcurrido entre la fecha del accidente y la de la muerte.
Incidente: Acontecimiento no deseado que resulta o puede resultar en daños a las personas,
propiedad y/o pérdidas en los procesos.
Horas-hombre trabajadas: Es el número total de horas trabajadas bajo ciertas condiciones
ambientales por los trabajadores incluyendo los de operación, producción, mantenimiento,
transporte, etc.
Seguridad e Higiene Industrial
CRITERIOS PARA REGISTRAR LOS ACCIDENTES / INCIDENTES DE TRABAJO
1. Criterio General: Se debe considerar que un accidente de trabajo debe ser registrado en los
formatos señalados para tal fin cuando, el accidente da como consecuencia lo siguiente: muer- te, días perdidos, trabajo restringido o transferencia a otro puesto de trabajo, tratamiento médico posterior a los primeros auxilios, o pérdida de conciencia.
2. ¿En qué formato se debe reportar un accidente de trabajo?
Se debe reportar en el formato "Aviso de Accidente" dentro de las 24 horas de ocurrido, y dentro
de 5 días útiles posteriores entregar este Formato a EsSalud.
3. ¿Cuento el día en el cual ocurrió el accidente para hacer el cálculo de días perdidos?
No, comience a contar lo días perdidos a partir del día siguiente de ocurrido el accidente.
4. ¿Cómo registro una lesión cuando un médico recomienda que el trabajador permanezca
en su casa y él viene a trabajar de todas maneras?
Se debe registrar los días recomendados por el médico como días perdidos independiente-
mente si el trabajador sigue o no los consejos dados por el médico.
5. ¿Cómo registro una lesión cuando un médico recomienda que el trabajador retorne al
trabajo pero el trabajador permanece en su casa?
En esta situación, se debe parar la cuenta de días perdidos en la fecha que el médico reco-
mendó que el trabajador retorne al trabajo.
6. ¿Cómo cuento los fines de semana, feriados, u otros días en los cuales el trabajador no
tiene que trabajar de todas maneras?
Se debe contar los días calendario que el trabajador estuvo fuera del trabajo como resultado de
la lesión, independientemente si el tenía que trabajar o no. Esto quiere decir que se deben incluir
fines de semana, feriados y otros.
7. ¿Hay un límite de días a partir del cual ya no debo contar como días perdidos?
Si, se debe contar hasta un máximo de 11 meses y 10 días calendarios.
8. ¿Debo dejar de contar los días perdidos si el trabajador que está fuera del trabajo por
lesión se retira de la empresa?
Si, sólo en el caso que el retiro del trabajador no tenga relación con la lesión, tal como un cierre
de planta, o conseguir otro trabajo. Si el trabajador deja la empresa como consecuencia de la
lesión se debe estimar los días perdidos para el registro respectivo.
9. ¿Debo registrar un accidente de trabajo que resulta en trabajo restringido o transferencia
de puesto de trabajo?
Cuando una lesión involucra trabajo restringido o transferencia a otro puesto de trabajo, pero
no tuvo como consecuencia muerte o días perdidos, se le debe registrar en el formato "Informe
Preliminar de Accidente" como accidente leve.
10. ¿Si un trabajador en mi establecimiento es un empleado del contratista, debo registrar el
accidente ocurrido a ese trabajador?
Si.
Seguridad e Higiene Industrial
GUÍA PARA LA INVESTIGACIÓN DE ACCIDENTES DE TRABAJO
EL PROCESO DE INVESTIGACIÓN.
Se entiende por investigación de accidentes a la acción de indagar y buscar con el propósito
de descubrir relaciones causas-efecto.
Una investigación no está limitada a la aplicación de una norma de tipo estadístico sino que trata
de encontrar todos los factores del accidente con el objeto de prevenir hechos similares, delimitar
responsabilidades, evaluar la naturaleza y magnitud del hecho, e informar a las autoridades y al
público. La labor del investigador o investigadores concluirá en un informe a ser elevado a aquella
autoridad que ordenó la investigación.
Los pasos a seguir en un proceso de investigación son los siguientes:
a. Reacción ante la emergencia.
b. Recolección de información.
c. Análisis de los datos.
d. Conclusiones.
e. Recomendaciones.
1. ANÁLISIS DE LOS DATOS - IDENTIFICACIÓN DE LA CAUSA DEL ACCIDENTE.
Un completo análisis de los datos recogidos es crítico para determinar con precisión los facto- res causales del accidente. El resultado de dicho análisis proporciona las bases para las correcciones y acciones correctivas. El escoger un buen método analítico es importante para proporcionar resultados que puedan ayudar a desarrollar un reporte de investigación que tenga conclusiones certeras y de utilidad.
Esta guía recomienda el uso del Análisis de Causalidad desarrollado por Frank Bird del Loss Control Institute, que ha probado ser de comprobada eficiencia en la determinación de los múl- tiples factores que causan un accidente.
La lógica que sigue el modelo se expresa a través del siguiente gráfico:
En la que se indica que el resultado de todo incidente/accidente es una pérdida; las principales pérdidas y las que más se perciben son: daño a la persona (lesión), a la propiedad o al proceso (pérdidas económicas).
El incidente/accidente es el resultado de un contacto con una fuente de energía o sustancia (forma del accidente).
Seguridad e Higiene Industrial
Para que este contacto se dé, deben haber existido circunstancias que se presentaron justa- mente antes del contacto, a esto se conoce como Causas Inmediatas y que se dividen en dos: Actos y Condiciones Subestándares, los cuales sólo son los síntomas del problema, detrás de estos se encuentran las verdaderas causas o Causas Básicas que explican el por qué ocurren los actos y condiciones subestándares, estas a su vez se dividen en dos: Factores Personales y Factores del Trabajo.
Sin embargo las causas básicas no son la causa final del accidente; lo que da inicio a la se- cuencia es la Falla o Falta de Control Administrativo, lo que como muestra el gráfico se divide en 3 factores: 1) Programas inadecuados o inexistentes 2) Estándares inadecuados de los programas y 3) Cumplimiento inadecuado de los estándares.
Basado en este modelo, se determinarán las causas del accidente que se está investigando, para lo cual en los anexos de esta guía se presentan una serie de tablas que ayudan al fiscali- zador a determinar con precisión:
a) Tipo de Lesión (pérdida: daño a la persona). b) Parte del cuerpo afectada. c) Forma del Accidente (accidente / incidente: contacto). d) Fuente del daño o lesión. e) Actos y Condiciones Subestándares. f) Factores Personales y Factores del Trabajo. g) Acciones Correctivas.
Sin embargo es importante mencionar en primer lugar que ninguna técnica analítica por si sola determina en forma total los factores causales de un accidente, y generalmente se deben com- binar con otras técnicas para validar en forma cruzada una con otra. En segundo lugar las téc- nicas analíticas no pueden ser usadas mecánicamente sin usar el razonamiento. Las mejores técnicas analíticas pueden no ser efectivas si no son aplicadas a circunstancias específicas y adecuadamente adaptadas.
A) Determinación de las Causas Inmediatas
Las causas inmediatas de los accidentes, son las circunstancias que se presentan justamente
antes del contacto. Por lo general, son observables o se hacen sentir. Son de dos tipos: Actos
Subestándares y Condiciones Subestándares.
• Actos Subestándares, son actos u omisiones del trabajador, que lo desvía de un procedimiento
o de la forma aceptada como correcta para efectuar una tarea los cuales podrían dar paso a la ocurrencia de accidentes, para determinar el(los) acto(s) subestándar(es).
• Condiciones Subestándares, Son aquellas condiciones del ambiente de trabajo que no cumplen
con los estándares establecidos, las cuales podrían dar paso a la ocurrencia de accidentes, para determinar la(s) condición(es) subestándar(es).
En las tablas correspondientes se hallará una descripción genérica; el investigador tendrá que adicionar una descripción más específica del acto o condición de acuerdo a la evidencia recogida.
Por ejemplo: condición subestándar: (2) Equipos de protección personal / ropa inadecuada o insuficiente,. no se dotó al trabajador con careta protectora contra impactos y chispas.
Seguridad e Higiene Industrial
Por ejemplo: acto subestándar: (9) Emplear en forma inadecuada o no usar el equipo de protección personal,. el trabajador no usó los guantes aislantes al momento de hacer la instalación.
B) Determinación de las Causas Básicas
Las causas básicas de los accidentes son las causas reales que se manifiestan detrás de las
causas inmediatas o síntomas; son las razones por las cuales ocurren los actos y condiciones
subestándares.
Se clasifican en dos: Factores Personales que explican los Actos Subestándares y los Factores del Trabajo que explican las Condiciones Subestándares. • Los Factores Personales, para cada acto subestándar deberá haber uno más factores perso-
nales que lo expliquen.
• Los Factores del Trabajo, para cada condición subestándar deberá haber uno o más factores
personales que lo expliquen.
En las tablas correspondientes se hallará una descripción genérica; el investigador tendrá que adi- cionar una descripción más específica del factor personal o del trabajo de acuerdo a la evidencia recogida.
Por ejemplo: para la condición subestándar: (2) No contar con equipos de protección personal / ropa o que estos sean inadecuados o insuficientes,. no se dotó al trabajador con careta protec- tora contra impactos y chispas.
Se pudo determinar que el(los) factor(es) del trabajo que explica(n) esta condición se encuentra bajo el encabezado:
Herramientas y Equipos Inadecuados, en el punto (49) Evaluación deficiente de las necesidades y los riesgos, la administración, de acuerdo a los riesgos evaluados, no consideró necesaria el uso de careta protectora para esta tarea.
Estándares deficientes de trabajo, en el punto (56) Desarrollo Inadecuado de normas para inventa- rio y evaluación de las exposiciones y necesidades, .la empresa no cuentan con procedimientos que permitan una adecuada evaluación de las exposiciones y necesidades.
Por ejemplo: para el acto subestándar: (9) Emplear en forma inadecuada o no usar el equipo de protección personal,. el trabajador no usó los guantes aislantes al momento de hacer la instalación.
Se pudo determinar que el(los) factor(es) personal(es) que explica(n) este acto se encuentra bajo el encabezado:
Falta de Conocimiento, en el punto (54) falta de experiencia, .el trabajador tenía solamente dos semanas en el puesto.
En este caso se podría agregar otro factor: (56) Entrenamiento inicial inadecuado. la inducción inicial al trabajador no incluyó temas de se- guridad.
Seguridad e Higiene Industrial
INFORME DE INVESTIGACIÓN DE ACCIDENTES / INCIDENTES
2. DEPARTAMENTO / SECCIÓN / ZONA DE
3. LUGAR EXACTO DEL
ACCIDENTE / INCIDENTE
LESIÓN PERSONAL
DAÑO A LA PROPIEDAD
CUASI ACCIDENTE
14. COSTOS ESTIMADOS
9. PARTE DEL CUERPO
15. COSTOS REALES
10. NATURALEZA DE LA
16. NATURALEZA DEL
11. OBJETO / SUSTANCIA / 17. OBJETO / SUST. QUE
23. OBJETO / EQUIP.
QUE CAUSO LA LESIÓN
12. PERSONA CON MÁS
18. PERSONA CON MÁS
CONTROL SOBRE EL
CONTROL SOBRE EL
SOBRE EL PUNTO 23
Seguridad e Higiene Industrial
25. DESCRIBIR CLARAMENTE COMO SUCEDIÓ EL ACCIDENTE (PARA TODO ACCIDENTE CON VEHÍCULO AUTOMOTOR INCLUIR UN DIAGRAMA DEL ACCIDENTE) .
26. CAUSAS INMEDIATAS Y/O ACTOS O CONDICIONES SUBESTÁNDARES QUE MÁS CONTRIBUYERON AL ACCIDENTE / INCIDENTE (ver tabla 04) HACER UNA BREVE DESCRIPCIÓN . .
ÁLISI 27. CAUSAS BÁSICAS Y/O FACTORES PERSONALES O DE TRABAJO QUE
AN JUSTIFICAN LAS CAUSAS INMEDIATAS
(ver tabla 05) HACER UNA BREV DESCRIPCIÓN . . .
28. GRAVEDAD POTENCIAL DE LAS
29. PROBABILIDAD DE
PÉRDIDAS. RECURRENCIA
EVALUACIÓN
FRECUENTE . OCASIONAL .
Seguridad e Higiene Industrial
30. MEDIDAS DE CONTROL. (ENUMERAR LAS MEDIDAS QUE SE HAN TOMADO O SE TOMARAN PARA EVITAR LA RECURRENCIA)
Seguridad e Higiene Industrial
RIESGOS ELÉCTRICOS
Riesgos eléctricos es todo aquel riesgo originado por la energía eléctrica, quedando específica-
mente incluidos los riesgos de:
• Choque eléctrico por contacto directo o indirecto. • Quemaduras por choque o arco eléctrico. • Caídas o golpes como consecuencia de choque o arco eléctrico. • Incendios o explosiones originados por la electricidad.
CONTACTOS ELECTRICOS
Los contactos eléctricos pueden ser de dos tipos:
CONTACTOS DIRECTOS: son aquellos en que las personas entra en contacto con partes activas
de la instalación o elementos habituales en tensión.
CONTACTOS INDIRECTOS: son aquellos en los que persona entra en contacto con masas pues-
tas accidentalmente en tensión por no formar parte del circuito eléctrico.
DESARROLLO DE TRABAJOS
Como norma general todo trabajo en una instalación eléctrica o en zona próxima a la misma que
lleve consigo un riesgo eléctrico deberá efectuarse sin tensión. Se exceptúan los casos siguientes,
que se llevaran a cabo en todo caso con los medios de protección personal que resulten necesarios:
Seguridad e Higiene Industrial
• Operaciones elementales de conexión y desconexión en instalaciones de baja tensión con ma-
terial eléctrico concebido para su uso por el público en general.
• Trabajos en instalaciones eléctricas con tensiones de seguridad sin riesgo de confusión y siem-
pre que las intensidades de un eventual cortocircuito no supongan riesgo de quemadura.
• Maniobras, mediciones, ensayos y verificaciones cuya naturaleza lo exija (apertura y cierre de
seccionadores, medición de intensidades, ensayos de aislamiento, etc.)
• Los trabajos en instalaciones eléctricas o en su proximidad, cuando las condiciones de explo-
tación o de continuidad del servicio así lo requieran.
La reposición de la tensión solo comenzara una vez finalizado el trabajo, después de haberse re-
tirado los trabajadores no indispensables para la ejecución de la tarea, y tras haber recogido las
herramientas y equipos utilizados.
MEDIDAS PREVENTIVAS
Toda instalación, conductor o cable eléctrico debe considerarse conectado y en tensión. Antes de
trabajar sobre los mismos deberá comprobarse la ausencia de corriente con el equipo adecuado.
• Nunca deberán manipularse elementos eléctricos con las manos majadas, en ambientes hú-
medos o mojados accidentalmente (labores de limpieza, instalaciones a la intemperie, etc.) y siempre que se carezca de los equipos de protección personal necesarios.
Cuando el trabajo en estas zonas sea inevitable, únicamente deberá hacerse uso de aparatos eléc-
tricos portátiles con tensión de seguridad.
• No se alterarán ni retirarán las puestas a tierra ni los aislamientos de las partes activas de los
diferentes equipos, instalaciones y sistemas.
• Deberá evitarse en la medida de lo posible la utilización de enchufes múltiples para evitar la
sobrecarga de la instalación eléctrica. Nunca se improvisarán empalmes ni conexiones.
• No se hará uso cables-alargaderas sin conductor de protección para la alimentación de recepto-
res con toma de tierra. En todo caso, evitarse el paso de personas o equipos por encima de los cables para evitar tropiezos, sin olvidar el riesgo que supone el deterioro del aislante.
• Con carácter previo a la desconexión de un equipo o maquina será necesario apagarlo haciendo
uso del interruptor.
• Los cables de alimentación eléctrica estarán dotados de clavija normalizada para su conexión a
una toma de corriente. Para proceder a su desconexión será necesario coger la clavija directa- mente, sin tirar nunca del cable.
• Las clavijas y bases de enchufes asegurarán que las partes en tensión sean inaccesibles cuan-
do la clavija este total o parcialmente introducida.
• Todo equipo eléctrico con tensión superior a la seguridad (24 voltios) o que carezca de doble
aislamiento estará unido o conectado a tierra y en todo caso tendrá protección con interruptor deferencial, debiendo comprobarse periódicamente el correcto funcionamiento de dichas pro- tecciones.
• Se deberá prestar especial atención a los calentamientos anormales de los equipos e instala-
ciones eléctricas (cables, motores, armarios, etc.), así como a los cosquilleos o chispazos pro- vocados por los mismos. En estos casos será necesaria su inmediata desconexión y posterior notificación, colocando el equipo en un lugar seguro y señalizando su estado hasta ser revisado.
Seguridad e Higiene Industrial
• En ningún caso se llevarán a cabo trabajos eléctricos sin estar capacitado y autorizado para ello.
La instalación, modificación y reparación de las instalaciones y equipos eléctricos, así como el acceso a los mismos, es competencia exclusiva del personal de mantenimiento, que los llevará a cabo en todo caso haciendo uso de los elementos de protección precisos.
PROTECCIÓN DE MÁQUINAS.
Las tablas o tablones deberán colocarse en hileras separadas por travesamos; y cuando se necesi-
te operar desde arriba, formar escalones con las tablas, para subir.
IMPORTANCIA DE LA PROTECCIÓN DE MÁQUINAS.
Las investigaciones en Seguridad Industrial demuestran que, entre el 10% al 15% de todas las
lesiones en accidentes de trabajo, intervienen máquinas u otros equipos impulsados por energía
eléctrica o mecánica.
Esto indica que la maquinaria es la fuente principal de accidentes que puedan ocurrir por:
Contacto directo con las partes móviles.
Trabajo en proceso (rebabas producidas por una máquina herramienta, "zapateo" de una sierra cir-
cular, proyección de partículas o piezas rotas, e*c.)
Falla mecánica o eléctrica.
Falla humana (curiosidad, fatiga, distracción y temeridad).
La protección de la maquinaria, se hace mediante dispositivos que se denominan guardas. La impor-
tancia de proteger la maquinaria por medio del uso de guardas es para:
Eliminar la fuente principal de accidentes por efecto de las máquinas.
Disminuir el Índice de alta gravedad causado por la maquinaria.
Impedir la pérdida de la producción.
Proteger al trabajador y al personal de la planta.
5 PUNTOS DE LAS MÁQUINAS QUE NECESITAN PROTECCIÓN.
Las guardas deben proteger los siguientes puntos de la máquina:
TRANSMISIÓN DE ENERGÍA.
Es la transmisión inicial de la energía del motor a la máquina.
Incluye ejes, poleas, fundas y cadenas impulsoras; trenes de engranaje, ruedas de cadena y trans-
misiones por fricción; llaves, tomillos prisioneros y otros objetos salientes; collarines y acoplamien-
Seguridad e Higiene Industrial
PIEZAS MÓVILES
Son accesorios del sistema de transmisión, ta-
les como dispositivos de mando o alimentación;
impulsores primarios, cigüeñales, bielas, contra-
vástagos, reguladores; cabezales o carros móvi-
les; levas y embragues.
En general, toda pieza auxiliar de la máquina que
produzca movimiento.
5 PUNTO DE OPERACIÓN.
Es el lugar de la máquina en que el material entra a elaborarse. Aquí, el mate- rial cambia de una
forma a otra; por ejemplo, el proceso de corte, torneado, estampado, cizallado, limado, taladrado,
5 PRINCIPALES TIPOS DE GUARDAS.
De acuerdo a las características especificas de las máquinas, las guardas pueden ser de
diferentes tipos.
Entre los más comunes tenemos;
GUARDAS DE BARRERA FIJA.
Es un área estacionaria o fija, dispuesta de tal modo que protege al trabajador de la máquina de
cualquier contacto accidental, con la transmisión, las piezas móviles o el punto de operación.
Estas guardas deben fijarse en la máquina por medio de dispositivos de sujeción.
GUARDAS AUTOMÁTICAS.
Son dispositivos de avance o alimentado que no necesita los servicios del trabajador.
Pueden ser de dos tipos:
a) De alimentación semiautomática o mecánica b) Armario de avance, movido por la máquina, sin necesidad que las manos del trabajador entren
en la zona de riesgo
c) Automáticas, movidas por el Pistón.-
Son dispositivos movidos por la propia máquina, que apartan de la zona de riesgo de las manos, los brazos o el cuerpo del trabajador, el carro o martinete al momento de descender.
GUARDA DE COMPUERTA MECÁNICA.
Aquí la compuerta desciende y tapa el frente de operación, de tal manera que no se puede dis-
parar !a prensa hasta que la guarda quede en su posición correcta. El borde de la compuerta debe
ser acojinado, para evitar daño al operario. Esta guarda puede convertirse en guarda de barra fija.
Seguridad e Higiene Industrial
GUARDAS DISYUNTORES.
a) Para rodillos.- Son varillas disyuntores horizontales, colocadas de tal modo que al entrar en
contacto con el cuerpo o la cabeza del trabajador, ponen instantáneamente en unión el meca- nismo de freno que detiene en forma rápida el rodillo.
b) Manuales.- Este tipo exige la aplicación simultánea de presión en dos palancas o botones,
utilizando las dos manos.
c) Tipo ojo eléctrico.- Se llama también célula fotoeléctrica. Se justifica el uso de este dispo-
sitivo cuando se necesita un sistema de freno que detenga instantáneamente la máquina, e impida que se te ponga en marcha, si en la zona de riesgo, protegida por el rayo de la célula fotoeléctrica, se encuentra algún objeto.
GUARDAS DE POSICIÓN.
Estas guardas hacen las veces de barrera o cerca, que impide el contacto, por accidente, entre una
persona y la máquina en movimiento, las vueltas, los resortes, etc.
El más representativo, es la guarda de barandal.
REQUISITOS DE LAS GUARDAS.
Las guardas deben ser diseñadas, construidas y usadas de manera que:
• Sean fuertes y firmemente instaladas. • Resistentes al fuego y corrosión • Faciliten la lubricación o ajuste de la máquina. • No constituyan un riesgo en sí (libres de astillas, bordes asperos y afilados). • Sean fáciles de desmontar y armar posteriormente, después de una separación. • Prevengan todo acceso a la zona de peligro durante las operaciones. • Sean lo suficientemente fuertes, para evitar que la proyección de piezas las rompan. • No ocasionen molestias al operador (visión y maniobrabilidad). • No interfieran innecesariamente en la producción.
PRÁCTICAS SEGURAS.
• Ninguna persona quitará o ajustará alguna guarda sin per-
miso del supervisor; salvo el caso de que la persona interesada esté específicamente preparada, y el ajuste de la máquina sea parte de su trabajo normal.
• Ninguna máquina debe ser puesta en marcha, a menos que
las guardas se hallen en su lugar y en buenas condiciones. • Siempre que se quiten los resguardos, para hacer reparaciones o mantenimiento, se desconectará la corriente del equipo y se pondrá candado al interruptor principal. • No debe permitirse al personal, trabajar en el equipo mecánico o cerca de él con corbata, ropa suelta y otros objetos similares.
Seguridad e Higiene Industrial
PREVENCIÓN DE ACCIDENTES
1. GENERALIDADES.
Los peligros y riesgos que encierran los accidentes, no sólo
se evitan tomando en cuenta el orden, la limpieza y la protec-
ción de caídas, sino también tomando en cuenta los peligros
que ofrecen el manejo de herramientas, materiales y máqui-
nas sin protección.
La presente unidad didáctica trata sobre los métodos y reglas
de control que deben utilizarse en él:
a. MANEJO MANUALES DE HERRAMIENTAS.
Un gran porcentaje de accidentes son causados por el ma-
nejo inadecuado de herramientas manuales e instrumentos
b. MANEJO DE MATERIALES.
La manipulación, el transporte y el almacenamiento de diferentes tipos de materiales; son fuentes
riesgosas de accidentes
c. PROTECCIÓN DE MAQUINAS.
La falta de protección o el mal uso de guardas en las máquinas, constituyen riesgos latentes de
2. MANEJO DE HERRAMIENTAS DE MANO.
Cuando el hombre primitivo comenzó a dominar el mundo que le rodeaba, buscó elementos que le
permitieran extender sus manos. Así fue como surgieron las herramientas manuales.
En el principio, tuvo que valerse de piedras, huesos, conchas, palos / carapachos, adaptados y
modificados de acuerdo a las necesidades del grupo, en nuestros días, el hombre continúa usando
herramientas manuales.
Seguridad e Higiene Industrial
Cuando uno piensa en el número de lesiones que producen estas herramientas, no deja de pregun-
tarse: ¿Cómo es que no se ha encontrado un medio para utilizarlas con más seguridad?
Por sencillas que sean estas herramientas, parece que e! hombre insiste en lesionarse con ellas.
Las usamos en la casa, en el taller o en diferentes circunstancias. Tan pequeños son el martillo, el
desentomillador, el serrucho, los alicates, que sin querer nos afectan
PRINCIPALES
ACCIDENTES
PRODUCIDOS
POR HERRAMIENTAS DE MANO.
a. HERRAMIENTAS DEFECTUOSAS.
Antes de utilizar una herramienta, debe revisarse cuida-
dosamente. Las herramientas defectuosas deben retirarse
del servicio, para ser restauradas adecuadamente.
b. USO DE HERRAMIENTAS INADECUADAS.
La herramienta sirve para determinado propósito. Esto
significa, que el empleo correcto de la herramienta para
determinada tarea, evita accidentes.
c. PROCEDIMIENTO INCORRECTO.
El uso incorrecto del empleo de una herramienta, produce
accidentes y daña la maquinaria.
d. MAL CUIDADO DE LAS HERRAMIENTAS.
El mal cuidado de las herramientas es consecuencia de no tener en cuenta el control, la conserva-
ción y la reparación oportuna de estos instrumentos.
La revisión diaria y el cuidado de las herramientas, evita accidentes
4. DEFECTOS ESPECÍFICOS DE LAS HERRAMIENTAS.
Hay que revisar cuidadosamente las herramientas, pues al presentar cualquier defecto, las vuelve
peligrosas para el fin a que están destinadas.
• Cinceles y punzones (herramientas de golpe): Puntas o cabezas mal templadas (cabezas
aplastadas o astilladas, puntas deformadas o rotas), longitud inadecuada, etc.
• Taladros, barrenos, brocas, etc.: Mal templados, embotados, gastados, Tilos mellados, con la
espiga rota, gastada o estropeada
• Limas. Carentes de mango, cola deformada o rota; picadura gastada o embotada, bordes mel-
lados; limas rotas.
• Martillos: Mangos sueltos, hendidos o ásperos, cabezas melladas, aplastadas o astilladas, uñas
58 dobladas o rotas; equilibrio defectuoso. Cuñas inadecuadas o fallantes.
Seguridad e Higiene Industrial
• Serruchos: Dientes mal ajustados, o mal afilados, hojas curvadas, mangos sueltos o rotos,
Ganchos, tenazas, etc. Forma inadecuada, flojos, puntas embotadas, deformados
• Cuchillos: Embotados, mellados, o con filos o puntas mal conformados; mango suelto, roto o
corta Mal afilados. Sin guarda para la mano (o con guarda inadecuada).
• Gatos de palanca o de tomillo: Engranes, cremalleras o fijador gastados, hilos de rosca gastados
o rotos; dispositivos de retención rotos, abombados; gastados o mal diseñados. Mango curvado, demasiado pequeño o demasiado suelto.
• Zapapicos, hachas, palancas de gancho: Mangos sueltos, hendidos o rotos; puntas o filos em-
botados, mellados o mal templados; mal equilibrados.
• Destornilladores: Mangos hendidos, sueltos o rotos; hoja mellada o deformada; cola curvada. • Palas, azadas: Mangos rotos, hendidos o sueltos, hoja deformada o mellada. • Llaves de tuerca: Mordazas gastadas o abombadas: mangos ásperos o curvados;
mecanismo gastado, atascado o roto.
5. EMPLEO DE HERRAMIENTAS INADECUADAS.
Emplear la herramienta adecuada para la tarea, significa hacer uso debido de la herramienta de mano destinada al uso específico.
A. USOS CORRECTO O INCORRECTO DE LAS HERRAMIENTAS DE MANO
HERRAMIENTA
USO CORRECTO
USO INCORRECTO
Cinceles, formones
Para cortar madera o metal.
Como destornillador, como palanca.
Barrenos, brocas, etc.
En el material adecuado.
En material inadecuado.
Como martillo o palanca.
Serruchos o sierras de
En material adecuado.
En material inadecuado. Em-
Emplear la sierra de trozar,
plear sierras al hilo para trozar.
Emplear la sierra de trozar,
transversalmente a la veta.
para aserrar el hilo.
Emplear la sierra al hilo, para aserrar en el sentido de la veta.
Seguridad e Higiene Industrial
HERRAMIENTA
USO CORRECTO
USO INCORRECTO
En trabajos de carpintería.
Emplear el martillo de uñas
En trabajos de mecánica
para trabajar acero templado.
para arrancar clavos.
Emplear el martillo de mecánico, como si fuera de carpintero. Emplear el martillo de uñas como cincel.
Exclusivamente para cortar.
Como destornillador o palanca.
Para levantar pesos dentro
de sus límites.
Como soporte después del levantamiento.
Romper suelos o pavimentos. Como palanca.
Cortar, picar o partir
Como palancas o cuñas,
material adecuado (madera,
para cortar materiales
Destornilladores
Aflojar o apretar tornillos,
Como palancas, cuña o cincel.
Mover materiales, cual si
Como azada, cuña o palanca.
fuese una cuchara.
Partir y retirar
Como cuchara o pala.
materiales adecuados (tierra, arcilla).
Llaves de tuercas
Aflojar o apretar juntas que Como martillo, o utilizar el tengan roscas como medio
tipo inadecuado de llave.
de unión, como pernos, tubos, etc.
Alicates o pinzas
Asir y retirar objetos
Apretar o aflojar tuercas
Calibradores y/o reglas
Medir datos y tolerancias.
Como abrazaderas.
para mediciones finas.
B. CUIDADO DE LAS HERRAMIENTAS
Para tener herramientas seguras, es necesario tener en cuenta lo siguiente: a) Control del almacén de herramientas
- Comprobación y verificación regulares de
- Reparación y mantenimiento de las herra-
- Conservación y compras.
b) Revisión de las herramientas
- Llevar un programa. - Política a seguir. - Instrucción del personal.
c) Buen orden y cuidado de las herramientas
- Almacenamiento clasificado y adecuado.
- En el lugar de trabajo.
Seguridad e Higiene Industrial
- Limpieza de la herramienta
- En conclusión : El buen manejo y cuidado de las herramientas manuales significa:
Prevenir accidentes y disminuir su incidencia. Menores costos de mantenimiento y conservación.
Mejor calidad del producto.
Aumento de la productividad y la producción.
Además de conocer el uso correcto de las herramientas, debemos tener algunos
cuidados. Por ejemplo:
Si trabajamos en un lugar en que la atmósfera contenga gases inflamables,
debemos emplear herramientas que no produzcan chispas.
Si trabajamos con cinceles, debemos tener cuidado con las esquirlas. Si trabajamos con destornilladores y piezas pequeñas, debemos apoyar éstas en
una mesa o sujetarlas con tomillos adecuados. Una de las heridas más dolorosas, es la producida por los destornilladores.
Cuando se trabaja con llaves de boca, debemos cuidar que las mordazas
en el sentido en que actúa la fuerza. Si hay que empujarlas, hágase con la palma de la mano, sin agarrarlas, esto es para evitar lesiones, producidas al aflojarse violentamente las tuercas o escaparse la llave.
Si trabajamos con esmeril, debemos colocamos lentes, para evitar lesiones en
Cuando transportamos herramientas, no debemos: Llevar herramientas filudas en los bolsillos.
Subir escaleras, con herramientas tomadas de la mano.
Para conservar en buen estado las herramientas de mano, debemos efectuar:
Almacenamiento adecuado.
Inspecciones periódicas.
Limpieza, lubricación y reemplazo, cuando sea necesario.
RESUMEN.- Un buen manejo y cuidado de las herramientas significa:
Prevención de accidentes.
Menores costos de mantenimiento.
Mejor calidad del producto.
Aumento de producción.
Seguridad e Higiene Industrial
Source: http://fullseguridad.net/wp-content/uploads/2016/09/Descarga-manual-de-seguridad-e-higiene-industrial.pdf
11700 • The Journal of Neuroscience, October 24, 2007 • 27(43):11700 –11711 Neurobiology of Disease Cannabinoids Elicit Antidepressant-Like Behavior andActivate Serotonergic Neurons through the MedialPrefrontal Cortex Francis Rodriguez Bambico,1 Noam Katz,1,2 Guy Debonnel,1† and Gabriella Gobbi1,21Neurobiological Psychiatry Unit, Department of Psychiatry, McGill University, Montre´al, Quebec, Canada H3A 1A1, and 2Department of Psychiatry, Centrede Recherche Fernand Seguin, Hoˆpital L.H. Lafontaine, Universite´ de Montre´al, Quebec, Canada H1N 3V2
Resúmenes de las comunicaciones orales Revista Argentina de Medicina Respiratoria 2003 - Suplemento: 1-10 ¿QUE INDICA EL PH EN EL CONDENSADO DEL AIREEXHALADO EN SUJETOS CON ASMA ESTABLE? EMPIEMA PARANEUMONICO EN NEUMONIA ADQUIRIDAEN LA COMUNIDAD. PREVALENCIA BACTERIOLOGICA Y PERFILES DE RESISTENCIA Nannini LJ, Zaietta G,Varela JA, Fernández OM, Guerrera AL, Flores DM.