Mb.uni-siegen.de
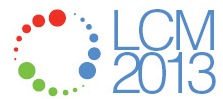
The 6th International Conference on Life Cycle Management in Gothenburg 2013
CONCEPTION OF AN AUTOMATED PLANT FOR THE
DISASSEMBLY OF LITHIUM ION BATTERIES
Prof. Dr. Michael Weyrich, Nirugaa Natkunarajah, M.Sc.*
*Paul-Bonatz-Str.9-11, 57068 Siegen, Germany
Keywords: automated disassembly; lithium ion batteries; End-of-Life Management
ABSTRACT
Due to the increasing number of electric cars and consequently lithium ion batteries, the automation of disassembly becomes vital. Therefor information on lithium ion batteries referring to components, geometries, materials and joining technologies are collected and a concept for the automated disassembly is deduced. In this context, the applications of sensors for the identification of batteries, as well as actors for the cutting are evaluated.
With the development and distribution of electric cars and the associated high quantities of lithium ion batteries, the recycling of batteries gains more importance. Lithium ion batteries comprise valuable raw materials such as lithium, cobalt and aluminum [Martens 2011]. Due to lack of raw materials their recovery is very important, especially for resource-poor EU-countries. For the recovery of these materials, the batteries should be fully dismantled and broken down into their basic components to enhance the efficiency of the down streamed material recycling [Martens 2011]. The challenges in the automation of the battery disassembly lie in their varieties, the ignorance of technical condition in the End-of-Life (EoL), hazardous materials and safety reasons.
Currently there are no approaches for the automation of disassembly processes for lithium ion batteries. This analysis defines criteria for automated disassembly and opens a new dimension to the End-of-Life management of electrical waste by the example of lithium ion batteries.
AUTOMATED DISASSEMBLY OF LITHIUM ION BATTERIES
Lithium ion batteries
The modular design of the lithium ion batteries enables an individual assembly according to the type of electric vehicles. The structure of battery packs, the battery modules and their components are depicted in figure 1a. The components of the battery pack and the battery
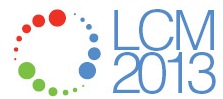
The 6th International Conference on Life Cycle Management in Gothenburg 2013
module are connected by different joining technologies such as welding, soldering, bonding and screw or snap connections. There are three different cell designs: cylindrical, prismatic and pouch cells which are especially developed for the electromobility. Furthermore the cell components anode, cathode, separator and electrolyte consist of variant materials [Daniel 2008]. The dimensions, the materials and the way of assembly lead to variant battery systems which have to be considered in the disassembly (see figure 1b).
Figure 1. Composition and variety of a lithium ion battery [A123-System Inc.]
Evaluation of sensors and actors for the disassembly
For the development of the automated disassembly plant, sensors for the identification of variant battery systems and actors for the actual cutting have been assessed. The defined criteria have been ranked from very poor to very good (see figure 2).
Figure 2. Evaluation of sensor and actors for the disassembly
1 2013 A123 Systems, LLC. All rights reserved.
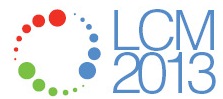
The 6th International Conference on Life Cycle Management in Gothenburg 2013
The analysis has shown that image processing is the most suitable technology for the identification of variant products. The image processing can be programmed and developed to be adaptive. Lasering and milling have been identified as the most suitable technologies for an automation, whereby the lasering is more flexible and scalable. However a fully automated system can only be realized by high standardization in combination with a disassembly database, further intelligent actors and sensors. Because of these reasons and the low quantity of lithium ion batteries today, a semi-automated disassembly plant, which can be modularly established to a fully automated system, is an appropriate solution. In the following, a semi-automated concept for the disassembly is presented.
Concept of a semi-automated disassembly plant
The automated disassembly processes today are tailored to a specific product. A modularized disassembly, consisting of separation-, detection-, control- and sub modules, increases the flexibility of the disassembly system [Kopacek 2003, Knoth et al. 2001]. In figure 3 the concept of a semi-automated disassembly of a lithium ion battery into its basis components is presented.
Figure 3. Concept of a semi-automated disassembly
The process starts with the delivery of the various battery packs to the companies that are responsible for the disassembly. There, the quality of the batteries is tested via voltage and visual control. In this concept, all damaged batteries are sorted to a special treatment where they are disassembled fully manually. The disassembly process is divided into three levels of dismantling procedures:
1. dismantling of pack to modules (white box in figure 3);
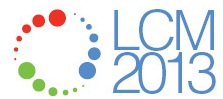
The 6th International Conference on Life Cycle Management in Gothenburg 2013
2. dismantling of module to cells (light grey box in figure 3);
3. dismantling cell into single components (dark grey box in figure 3).
The condition of the batteries is checked between every level. The undamaged batteries are discharged according to the defined safety regulations.
Due to the unknown variants of battery packs in current use, the process steps testing, discharging and sorting are executed manually. These process steps can be passed by all battery levels, as it is adjustable to different discharging parameters. The screwed and clamped elements are also manually dismounted, as the automation of these processes requires expensive intelligent image processing and complex grippers. All non-rigid components such as cables and clamping elements are manually cut. For the disassembly of the battery module, a laser combined with image processing is applied. The cells are dismounted by pyrolysis at the current state. In future this step should also be dismounted mechanically step by step in its single components.
CONCLUSIONS
In this paper a semi-automated concept for the disassembly of lithium ion batteries is presented. For the development of a flexible disassembly cell, several sensors and actors for the disassembly are evaluated and a modular approach with separation-, detection-, control- and sub modules is applied. The image processing is chosen for the identification of batteries. The most flexible and scalable disassembly technology is the lasering method, which is applied for the dismounting of battery modules. In the semi-automated disassembly plant, following modules are employed: laser cutting, manual cutting, test-, discharge- sorting- and vision modules.
For the realization of the above concept, database and data exchange systems have to be developed to handle the variants of lithium ion battery systems. Furthermore specific laser systems and laser parameters have to be deduced from experiments. The image processing has to be programmed and tested. With the selected image processing and robotics the semi-automated plant can be developed step by step to a fully automated disassembly plant.
REFERENCES
Martens, H (2011). Recycling von Elektro- und Elektronikgeräten. In H. Martens, Recyclingtechnik (pp.294-299). Heidelberg, Germany: Springer-Verlag.
Daniel, C. (2008). Materials and Processing for Lithium-ion Batteries. JOM, 60 (9), pp.43-48.
Kopacek B. (2003). Semi-automatisierte Demontage für Elektronikschrottrecycling. e&i Elektrotechnik und Informationstechnik, 5 , pp. 149-153.
Knoth R., Hoffmann M., Kopacek B. & Kopacek P. (2001). Intelligent disassembly of electr(on)ic equipment. IEEE Environmentally Conscious Design and Inverse Manufacturing. Proceedings EcoDesign 2001. Second International Symposium (pp. 557-561).
Source: https://www.mb.uni-siegen.de/lfa/informationspool/conception_of_an_automated_plant_for_the_disassembly_of_lithium_ion_batteries_nn_lcm.pdf
Private experience and observational learning in pharmaceutical demand Tanja Saxell∗† February 13, 2014 I quantify the roles of the physician's own experience and the past choices of other doctorsin pharmaceutical demand. I develop a model of medical decision-making under uncer-tainty about the quality of the match between the patient and drug treatment. Unlikeprevious demand models, I take into account both private and social learning, and allowheterogeneity in product quality across individuals. I test whether information on thepast choices of other doctors improves drug choices. Using rich data from the market forcholesterol drugs, I show that treatment patterns relying heavily on the past choices ofother doctors can lead to over-prescribing in terms of eciency. My results suggest thatcontinuity of care, where a patient is repeatedly consulting the same doctor, is an ecientpolicy to limit such behavior.
Current Research in Microbiology and Biotechnology Vol. 3, No. 4 (2015): 690-693 Research Article Open Access ISSN: 2320-2246 Prevalence and antibiotics sensitivity of Staphylococcus aureus skin infection in children in Khartoum, Sudan Salwa A. Aboud1, Abdallah El-yamani1, Mohamed A. Hussain1,* and Aimun AE. Ahmed2,3