9-15k_complete_service_manual.pdf
9,000 - 15,000 LBS. CAPACITY
OPERATION MAINTENANCE SERVICE MANUAL
TRIAL MODE − a valid license will remove this message. See the keywords property of this PDF for more information.
This manual is designed to provide information for you to understand, use, maintain, and service your trailer running gear system. Your axles are manufactured by Dexter Axle. Since 1960, Dexter's experience in the design, testing, and manufacturing of trailer axles has resulted in the most complete product line in the industry. The Dexter running gear system consists of axles, suspensions, and braking systems which are engineered to provide you the finest towing and stopping performance available today.
Two Dexter philosophies are at work to provide you the best product available and have enabled us to maintain our position of leadership. First, we operate on the theory that "there is always a better way" for a product to operate, to be manufactured, and/or to be serviced. We are constantly striving to find that better way.
Secondly, we maintain wall-to-wall production control so that all the major components of your running gear system are manufactured in Dexter facilities under our strict quality control standards. These manufactured components include axle beams, hubs, drums, spindles, and braking systems, as well as the components used in the attachment of the axle to the chassis. Dexter has the most complete, state-of-the-art manufacturing facilities which enable us to provide you, the trailer owner, with the finest product possible.
For all your running gear needs.
Visit us online at
TRIAL MODE − a valid license will remove this message. See the keywords property of this PDF for more information.
Maintenance Schedule .4Important Safety Notice .5Getting Started - Setup and Adjustment.5Answers to Commonly Asked Questions .6
Braking Systems - Electric
Electric Brakes.8Features .10
Self Adjusting Feature .11Brake Controllers .11How To Use Your Electric Brakes Properly .12Trailer Wire Size Chart.12Synchronizing Your Trailer Brakes .13
General Maintenance - Electric Brakes .14
Brake Adjustment .14Brake Cleaning and Inspection .15Brake Lubrication .15
Magnets .16Shoes and Linings .17Introduction to Troubleshooting .18Troubleshooting .18
Troubleshooting Chart - Electric .19How to Measure Voltage .21How to Measure Amperage .21Magnet Amperes Chart .22
Braking Systems - Hydraulic
Hydraulic Brakes .24Hydraulic Drum Brake Operation .25
Duo-Servo .25Uni-Servo .26Self-Adjusting Mechanism for 12¹⁄₄" Brakes .26Hydraulic Parking Brake Option .26Hydraulic Disc Brakes .28Electric/Hydraulic Actuation Systems .29Vacuum/Hydraulic .29Air/Hydraulic .30
Introduction to Troubleshooting .31
Troubleshooting Chart - Hydraulic .32Electric/Hydraulic Troubleshooting Guide .34
General Maintenance - Hydraulic Brakes .36
Drum Brake Adjustment .36Wheel Cylinders .37Brake Lines .37Shoes and Linings .37Hardware .38Instructions for 10-12K Hydraulic Disc Brakes .38
Hydraulic Disc Brake Parts .41
Braking Systems - Air
S-Cam Air Brakes .42
Air Brake Components .43
Air Chambers .43Spring Brake .43Slack Adjusters .44S-Cams .44
Table of Contents
General Maintenance/Adjustment .46
Brake Component Lubrication .46
12¹⁄₄" Quick Change Brakes - PQ .47
Recommended Disassembly .47
TRIAL MODE − a valid license will remove this message. See the keywords property of this PDF for more information.
Table of Contents
Recommended Reassembly .47Air Brake Automatic Slack Adjustment .49Air Brake Manual Slack Adjustment .50
Introduction to Troubleshooting .52
Troubleshooting Chart - Air.53
Hubs/Drums/Bearings .55
Hub Removal .55Brake Drum Inspection .55Bearing Inspection.56Bearing Lubrication - Grease .57Bearing Lubrication - Oil .58Recommended Wheel Bearing Lubrication Specs .59Seal Inspection and Replacement .61Installation/Adjustment .62
Axle & Suspension Installation .64
Suspension Systems .65
Slipper Leaf Springs .65Inspection and Replacement .66Suspension Replacement .68Torflex® Suspension .68
Heavy Duty Suspension Axle Alignment .70
Alignment/Procedure .70Measuring.71Adjusting/Precautions .72Additional Suspension Maintenance Check .72Heavy Duty Suspension Torque Requirements .73
Wheels and Tires
Wheel Selection .74Torque Requirements .75Wheel Torque Sequence .76
Tire Wear Diagnostic Chart .78
Fastener Torque Specifications .79Bearing Replacement Chart .80Seal Replacement Reference .80Electric Brake Magnets.80Brake Shoe Replacement Kits .8Air Brake Shoe & Linings .81Air Brake Repair Kits .81Disc Brake Pad Kit .81Disc Brake Caliper Repair Kit .81
Storage Preparation .82After Prolonged Storage - Inspection Procedure .83Trip Preparation Checklist .84
Dexter Axle Limited Warranty .85
Axle Identification .88
Dexter Video Gallery .90
TRIAL MODE − a valid license will remove this message. See the keywords property of this PDF for more information.
3 Months or
6 Months or
12 Months or
3,000 Miles
6,000 Miles
12,000 Miles
Test that they are
Adjust to proper operating
clearance (not required with
Inspect for wear and current
Inspect for wear or
Check for correct amperage
and modulation.
Check for leaks, sticking.
Inspect for cracks, leaks,
Check for wear and
Lubricate with approved
Lubricate with approved
Inspect wiring for bare
spots, fray, etc.
Check battery charge and
switch operation.
Inspect for abnormal wear
Inspect for corrosion or
wear. Clean and repack.
Inspect for leakage.
Replace if removed.
Inspect for wear, loss of
Inspect for bending, loose
fasteners and wear.
Inspect welds.
Tighten to specified torque
Inspect for cracks, dents, or
Inflate tires to mfg's.
Inspect for cuts, wear,
bulging, etc.
TRIAL MODE − a valid license will remove this message. See the keywords property of this PDF for more information.
Important Safety Notice
Appropriate service methods and repair procedures are essential for the safe, reliable operation of all running gear as well as the personal safety of the individual doing the work. This manual provides general directions for performing service and repair work with tested, effective techniques. Following these guidelines will help assure reliability.
There are numerous variations in procedures, techniques, tools, parts for servicing axles, as well as in the skill of the individual doing the work. This manual cannot possibly anticipate all such variations and provide advice or cautions as to each. Anyone who departs from the instructions provided in this manual must first establish that they neither compromise their personal safety nor the vehicle integrity by their choice of methods, tools, or parts.
Refer to your vehicle manufacturer's owners manual for additional procedures, techniques, and warnings prior to performing any maintenance or repairs.
!
CAUTION
This is the safety alert symbol. It is used to alert you to
potential injury hazards. Obey all safety messages that
follow this symbol to avoid possible injury or death.
Getting Started - Setup and Adjustment
For proper performance, all new axles should have the following checked at the specified intervals:
•
Wheel Nut Torque: at 10, 25, and 50 miles
•
Brake Adjustment: at 200 and 3,000 miles
•
Tire pressure: to manufacturer's requirements
•
Brake synchronization: set brake controller per controller
TRIAL MODE − a valid license will remove this message. See the keywords property of this PDF for more information.
Answers to Commonly Asked Questions
Q: Why do my brakes and hubs get so hot?
A: Braking systems use friction to slow the vehicle and the
energy used to retard the trailer is converted to heat. Dexter brakes are designed to operate up to extremely high temperatures during hard braking application. This heat is noticeable on the hub and drums and is to be normally expected on a properly functioning brake. If a brake is malfunctioning and running excessively hot, this can be noticed by smoking brakes or the paint burning off of the brake drum. If this occurs, refer to the brake troubleshooting diagram for your type of brake.
Q: Why do I have to adjust my brakes?
A: Brakes must be adjusted to compensate for the lining and
drum wear that occurs during use of the braking system. Some brakes require manual adjustment to move the linings closer to the drum. Refer to the brake adjustment section for your style of brakes. Other brakes may have an automatic brake adjuster such as the automatic slack adjusters for air brakes.
Note: Prior to 10/96 electric and hydraulic self-adjusting
brakes adjust only during hard, reverse stops. If your driving
does not include these types of stops, you will have to
manually adjust your brakes. Designs after 10/96 adjust both
in forward and in reverse. Adjustment in reverse still requires
hard stops, while adjustment in forward motion will occur
through normal driving.
Q: My brake linings are cracked, do I have to replace them?
A: Usually, light cracking of the surface of a brake lining
can be expected under normal use. This is not cause for replacement. However, if the lining is missing chunks, your brake linings or shoes will require replacement.
Q: Why do I have to torque the wheel nuts on my trailer and do
not have to do so in my car?
TRIAL MODE − a valid license will remove this message. See the keywords property of this PDF for more information.
A: The main reason is wheel capacity. Your entire car may
weigh 3,000 lbs. which is spread over four wheels, while a 6,000 lb. trailer axle has 3,000 lbs. on a single tire and wheel. This places greater stress on the wheel/tire combination. The second reason is loading. Your car is designed to have the wheels track the arc of a turn, reducing side load on the tire and wheel. Trailers are subjected to harsh side loads, especially in double and triple axle configurations. These side loads work to flex the wheel which may cause the wheel to lose torque over time. Please follow the wheel usage instructions located later in this manual.
Q: Why can't I lock and slide my electric brakes?
A: On an unloaded trailer, you may be able to lock up your
brakes if your electric brake controller is supplying full amperage to the brakes. When loaded to capacity, you may not be able to lock your brakes as electric brakes are designed to slow the trailer at a controlled rate, and not designed to lock up the wheels on a fully loaded trailer. Our brakes are designed to meet all applicable safety standards. All of our brakes will perform better after numerous burnish stops to seat the brake linings to the drums.
Q: I don't feel I have enough brakes or capacity on my axles.
Can I easily upgrade?
A: Usually depending on the trailer configuration, you can
upgrade your running gear to a higher capacity rating. We recommend consulting with the trailer manufacturer first before doing so.
Q: Can I change my brakes from electric to hydraulic or vice
A: This can be done on most axle models. We recommend
contacting the trailer manufacturer prior to changing your braking system to identify any potential problems.
TRIAL MODE − a valid license will remove this message. See the keywords property of this PDF for more information.
The electric brakes on your trailer are similar to the drum brakes on your automobile. The basic difference is that your automotive brakes are actuated by hydraulic pressure while your electric trailer brakes are actuated by an electromagnet. With all of the brake components connected into the system, the brake should operate as follows (see electric brake assembly illustration):
When the electrical current is fed into the system by the controller, it flows through the electromagnets in the brakes. The high capacity electromagnets are energized and are attracted to the rotating armature surface of the drums which moves the actuating levers in the direction that the drums are turning.
Braking Systems - Electric
TRIAL MODE − a valid license will remove this message. See the keywords property of this PDF for more information.
Braking Systems - Electric
The resulting force causes the actuating cam block at the shoe end of the lever to push the primary shoe out against the inside surface of the brake drum. The force generated by the primary shoe acting through the adjuster link then moves the secondary shoe out into contact with the brake drum.
Increasing the current flow to the electromagnet causes the magnet to grip the armature surface of the brake drum more firmly. This results in increasing the pressure against the shoes and brake drums until the desired stop is accomplished.
12V Battery for Breakaway Switch
Towing Vehicle Trailer Connection
TRIAL MODE − a valid license will remove this message. See the keywords property of this PDF for more information.
Features
Electrically actuated brakes have several advantages over other brake actuation systems.
1. They can be manually adjusted at the controller to provide
the correct braking capability for varying road and load conditions.
2. They can be modulated to provide more or less braking
force, thus easing the brake load on the towing vehicle.
3. They have very little lag time from the moment the tow
vehicle's brakes are actuated until the trailer brakes are actuated.
4. In an emergency situation, they can provide some braking
independent of the tow vehicle.
Adjuster Assembly
Left Hand or Road Side Brake Shown
Note: Actuating lever should always wrap around front side
of axle, magnet wires should exit brake backing plate on
rear side of axle.
Braking Systems - Electric
TRIAL MODE − a valid license will remove this message. See the keywords property of this PDF for more information.
Braking Systems - Electric
Self Adjusting Feature (12¼" Brake Series Only)
Forward self adjust electric brakes were introduced in October of 1996. This feature adjusts the brakes on both forward and reverse stops. Brake adjustment occurs when lining wear results in enough gap between the shoes and the brake drum surface. This added clearance will allow the adjuster mechanism to rotate the screw assembly at the bottom of the brake. That action expands the distance between the shoes and thus closes the gap to the drum surface.
Electric brake controllers provide power to the magnets to actuate the trailer brakes. Dexter Axle offers a state-of-the-art inertial controller called the Predator DX2®. This controller features an accelerometer design which senses the deceleration of the towing vehicle and sends a proportional voltage to the electric trailer brakes. Other features include a visual gain setting for quick and easy adjustment and a digital LED display to show the voltage output. A manual override sends full voltage to the trailer brakes, regardless of gain setting, for emergency conditions and also illuminates the brake lights to warn of an impending stop.
Most electric brake controllers provide a modulation function that varies the current to the electric brakes with the pressure on the brake pedal or amount of deceleration of the tow vehicle. Electronic or timing controllers do not provide proportional modulation. These controllers tend to be inexpensive but not the best choice for optimum braking. It is important that your brake controller provide approximately 2 volts to the braking system when the brake pedal is first depressed and gradually increases the voltage to 12 volts as brake pedal pressure is increased. If the controller "jumps" immediately to a high voltage output, even during a gradual stop, then the electric brakes will always be fully energized and will result in harsh brakes and potential wheel lockup.
TRIAL MODE − a valid license will remove this message. See the keywords property of this PDF for more information.
How to Use Your Electric Brakes Properly
Your trailer brakes are designed to work in synchronization with your tow vehicle brakes. Never use your tow vehicle or trailer brakes alone to stop the combined load.
Your brake controller must be set up according to the manufacturer's recommendations to ensure proper synchronization between the tow vehicle and the trailer. Additionally, you may have to make small adjustments occasionally to accommodate changing loads and driving conditions.
Proper synchronization of tow vehicle to trailer braking can only be accomplished by road testing. Brake lockup, grabbiness, or harshness is quite often due to the lack of synchronization between the tow vehicle and the trailer being towed, too high of a threshold voltage (over 2 volts), or under adjusted brakes.
Before any synchronization adjustments are made, your trailer brakes should be burnished-in by applying the brakes 20-30 times with approximately a 20 m.p.h. decrease in speed, e.g. 40 m.p.h. to 20 m.p.h. Allow ample time for brakes to cool between application. This allows the brake shoes and magnets to slightly "wear-in" to the drum surfaces.
Trailer Wire Size Chart
Recommended
Minimum Hookup
of Brakes
Distance in Feet
Wire Size (Copper)
Braking Systems - Electric
TRIAL MODE − a valid license will remove this message. See the keywords property of this PDF for more information.
Braking Systems - Electric
Synchronizing Your Trailer Brakes
To insure safe brake performance and synchronization, read the brake controller manufacturer's instructions completely before attempting any synchronization procedure.
!
CAUTION
Before road testing, make sure the area is clear of
vehicular and pedestrian traffic. Failure to brake safely
could result in an accident and personal injury to
yourself and/or others.
Make several hard stops from 20 m.p.h. on a dry paved road free of sand and gravel. If the trailer brakes lock and slide, decrease the gain setting on the controller. If they do not slide, slightly increase the gain setting. Adjust the controller just to the point of impending brake lockup and wheel skid.
Note: Not all trailer brakes are capable of wheel lockup. Loading
conditions, brake type, wheel and tire size can all affect whether
a brake can lock. It is not generally considered desirable to lock
up the brakes and slide the tires. This can cause unwanted flat
spotting of the tires and could also result in a loss of control.
If the controller is applying the trailer brakes before the tow vehicle brakes, then the controller adjustments should be made so the trailer brakes come on in synchronization with the tow vehicle brakes. For proper braking performance, it is recommended that the controller be adjusted to allow the trailer brakes to come on just slightly ahead of the tow vehicle brakes. When proper synchronization is achieved there will be no sensation of the trailer "jerking" or "pushing" the tow vehicle during braking.
TRIAL MODE − a valid license will remove this message. See the keywords property of this PDF for more information.
General Maintenance - Electric Brakes
Most Dexter 12¹⁄₄" electric brakes have a self adjusting feature. If manual adjusting is required, use the following procedure:
Brakes should be adjusted (1) after the first 200 miles of operation when the brake shoes and drums have "seated," (2) at 3,000 mile intervals, (3) or as use and performance requires. The brakes should be adjusted in the following manner:
1. Jack up trailer and secure on adequate capacity jack stands.
Follow trailer manufacturer's recommendations for lifting and supporting the unit. Make sure the wheel and drum rotates freely.
!
CAUTION
Do not lift or support the trailer on any part of the
axle or suspension system. Never go under any trailer
unless it is properly supported on jack stands which
have been rated for the load. Improperly supported
vehicles can fall unexpectedly and cause serious injury.
2. Remove the adjusting hole cover from the adjusting slot on
the bottom of the brake backing plate.
3. With a screwdriver or standard adjusting tool, rotate the star
wheel of the adjuster assembly to expand the brake shoes. Adjust the brake shoes out until the pressure of the linings against the drum makes the wheel very difficult to turn.
4. Then rotate the star wheel in the opposite direction until the
wheel turns freely with a slight lining drag.
5. Replace the adjusting hole cover and lower the wheel to the
6. Repeat the above procedure on all brakes. For best results,
the brakes should all be set at the same clearance.
Braking Systems - Electric
TRIAL MODE − a valid license will remove this message. See the keywords property of this PDF for more information.
Braking Systems - Electric
Brake Cleaning and Inspection
Your trailer brakes must be inspected and serviced immediately if a loss of performance is indicated. With normal use, servicing at one year intervals is usually adequate. With increased usage, this work should be done more frequently as required. Magnets and shoes must be changed when they become excessively worn or scored, a condition which can reduce vehicle braking.
Clean the backing plate, magnet arm, magnet, and brake shoes. Make certain that all the parts removed are replaced in the same brake and drum assembly. Inspect for any loose or worn parts, stretched or deformed springs and replace as necessary.
!
CAUTION
POTENTIAL ASBESTOS DUST HAZARD!
Some older brake linings may contain asbestos dust,
which has been linked to serious or fatal illnesses.
Certain precautions need to be taken when servicing
brakes:
1. Avoid creating or breathing dust.
2. Avoid machining, filing or grinding the brake linings.
3. Do not use compressed air or dry brushing for
cleaning (dust can be removed with a damp brush).
Before reassembling, apply a light film of grease or anti-seize compound on the brake anchor pin, the actuating arm bushing and pin, and the areas on the backing plate that are in contact with the brake shoes and magnet lever arm. Apply a light film of grease on the actuating block mounted on the actuating arm.
Do not get grease or oil on the brake linings, drums or
magnets.
TRIAL MODE − a valid license will remove this message. See the keywords property of this PDF for more information.
Your electric brakes are equipped with high quality electromagnets that are designed to provide the proper input force and friction characteristics. Your magnets should be inspected and replaced if worn unevenly or abnormally. As indicated below, a straightedge should be used to check magnet condition. For best results, the magnet should be flat.
Even if wear is normal as indicated by your straightedge, the magnets should be replaced if any part of the magnet coil has become visible through the friction material facing of the magnet. It is also recommended that the drum armature surface be refaced when replacing magnets (see section on Brake Drum Inspection). Magnets should also be replaced in pairs - both sides of an axle. Use only genuine Dexter replacement parts when replacing your magnets.
Gaps show ABNORMALWEAR (replace magnet)
Braking Systems - Electric
TRIAL MODE − a valid license will remove this message. See the keywords property of this PDF for more information.
Braking Systems - Electric
Shoes and Linings
A simple visual inspection of your brake linings will tell if they are usable. Replacement is necessary if the lining is worn to ¹⁄₁₆" or less. Shoes contaminated with grease or oil, or abnormally scored or gouged should also be replaced. Hairline heat cracks are normal in bonded linings and should not be cause for concern. When replacement is necessary, it is
Acceptable Hairline Cracks
important to replace both shoes on each brake and both brakes of the same axle. This will help retain the "balance" of your brakes.
!
CAUTION
POTENTIAL ASBESTOS DUST HAZARD!
Some older brake linings may contain asbestos dust,
which has been linked to serious or fatal illnesses.
Certain precautions need to be taken when servicing
brakes:
1. Avoid creating or breathing dust.
2. Avoid machining, filing or grinding the brake linings.
3. Do not use compressed air or dry brushing for
cleaning (dust can be removed with a damp brush).
After replacement of brake shoes and linings, the brakes must be re-burnished to seat in the new components. This should be done by applying the brakes 20 to 30 times from an initial speed of 40 m.p.h., slowing the vehicle to 20 m.p.h. Allow ample time for brakes to cool between applications. This procedure allows the brake shoes to seat in to the drum surface.
TRIAL MODE − a valid license will remove this message. See the keywords property of this PDF for more information.
Introduction to Troubleshooting
Proper brake function is critical to the safe operation of any vehicle. If problems are encountered with your trailer braking system, the following guide can be used to find the causes and remedies for some of the more common problems. If you are unsure or unable to resolve the problem, please contact your nearest repair facility for professional assistance.
Most electric brake malfunctions that cannot be corrected by either brake adjustments or synchronization adjustments, can generally be traced to electrical system failure. Voltmeters and ammeters are essential tools for proper troubleshooting of electric brakes.
Mechanical causes are ordinarily obvious, i.e. bent or broken parts, worn out linings or magnets, seized lever arms or shoes, scored drums, loose parts, etc. Replace defective parts with genuine Dexter replacements.
Please consult the following troubleshooting charts to determine the causes and solutions for common problems found in trailer braking systems.
!
CAUTION
Best braking performance is achieved with a controller
setting that is just short of wheel lock up or slide. Overly
aggressive braking which results in wheel lock up and
sliding, can cause a dangerous loss of control and
result in personal injury or death.
Braking Systems - Electric
TRIAL MODE − a valid license will remove this message. See the keywords property of this PDF for more information.
Braking Systems - Electric
Find & Correct
No Brakes
Test & Correct
Find & Correct
Grease or Oil on
Magnets or Linings
Clean or Replace
Clean & Correct
Cause of Corrosion
Worn Linings
or Magnets
Scored or Grooved
Machine or Replace
Brake Drums
Weak Brakes
Reburnish or Replace
Test & Correct
Loose, Bent or Broken
Brake Drums
Machine or Replace
Adjust System Resistor
Insufficient Wheel Load
Test & Correct
Broken Wires
Repair or Replace
Find & Repair
Find & Repair
TRIAL MODE − a valid license will remove this message. See the keywords property of this PDF for more information.
Wrong Magnet
Lead Wire Color
Grease or Oil on
Linings or Magnets
Clean or Replace
Brakes Pull to
Broken Wires
Find & Repair
Find & Repair
Harsh Brakes
Test & Correct
Lack of Lubrication
Noisy Brake
Grease or Oil on
Clean or Replace
Linings or Magnet
Machine or Replace
Cracked Brake Drums
Test & Correct
Machine or Replace
Brake Drums
Loose, Bent or Broken
Repair or Replace
Loose Wheel
Bent Spindle
Braking Systems - Electric
Replace Axle
TRIAL MODE − a valid license will remove this message. See the keywords property of this PDF for more information.
Braking Systems - Electric
How to Measure Voltage
System voltage is measured at the magnets by connecting the voltmeter to the two magnet lead wires at any brake. This may be accomplished by using a pin probe inserted through the insulation of the wires. The engine of the towing vehicle should be running when checking the voltage so that a low battery will not affect the readings.
Voltage in the system should begin at 0 volts and, as the controller bar is slowly actuated, should gradually increase to about 12 volts. If
the controller does not produce this voltage control, consult your controller manual.
The threshold voltage of a controller is the voltage applied to the brakes when the controller first turns on. Lower threshold voltage will provide for smoother braking. If the threshold voltage is too high, the brakes may feel grabby and harsh.
How to Measure Amperage
System amperage is the current flowing in the system when all the magnets are energized. The amperage will vary in proportion to the voltage. The engine of the tow vehicle should be running with the trailer connected when checking the trailer braking system.
One place to measure system amperage is at the BLUE wire of the controller, which is the output to the brakes. The BLUE wire must be disconnected and the ammeter put in series into the line. System amperage draw should be as noted in the following table. Make sure your ammeter has sufficient capacity and note polarity to prevent damaging your ammeter. With new ammeters that have inductive pickup clamps, it is not necessary to cut the blue wire.
TRIAL MODE − a valid license will remove this message. See the keywords property of this PDF for more information.
Magnet Amperes Chart
12¹⁄₄" x 3³⁄₈"
12¹⁄₄" x 4"
12¹⁄₄" x 5"
If a resistor is used in the brake system, it must be set at zero or bypassed completely to obtain the maximum amperage reading. Individual amperage draw can be measured by inserting the ammeter in the line at the magnet you want to check. Disconnect one of the magnet lead wire
connectors and attach the ammeter between the two wires. Make sure that the wires are properly reconnected and sealed after testing is completed.
The most common electrical problem is low or no voltage and amperage at the brakes. Common causes of this condition are:
1. Poor electrical connections2. Open circuits3. Insufficient wire size4. Broken wires5. Blown fuses (fusing of brakes is not recommended)6. Improperly functioning controllers or resistors
Another common electrical problem is shorted or partially shorted circuits (indicated by abnormally high system amperage). Possible causes are:
1. Shorted magnet coils2. Defective controllers3. Bare wires contacting a grounded object
Braking Systems - Electric
TRIAL MODE − a valid license will remove this message. See the keywords property of this PDF for more information.
Braking Systems - Electric
Finding the cause of a short circuit in the system is done by isolating one section at a time. If the high amperage reading drops to zero by unplugging the trailer, then the short is in the trailer. If the amperage reading remains high with all the brake magnets disconnected, the short is in the trailer wiring.
All electrical troubleshooting procedures should start at the controller. Most complaints regarding brake harshness or malfunction are traceable to improperly adjusted or non-functioning controllers. See your controller manufacturer's data for proper adjustment and testing procedures. For best results, all the connection points in the brake wiring should be sealed to prevent corrosion. Loose or corroded connectors will cause an increase in resistance which reduces the voltage available for the brake magnets.
TRIAL MODE − a valid license will remove this message. See the keywords property of this PDF for more information.
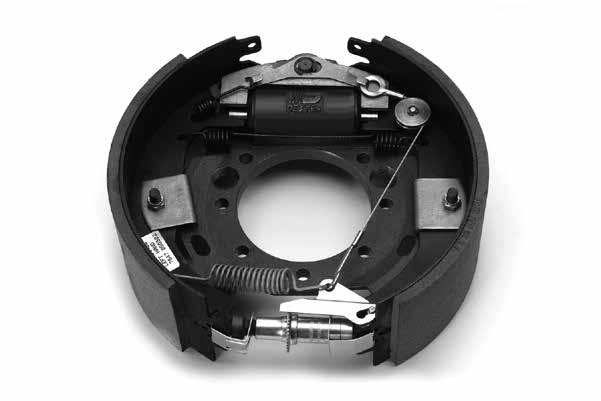
The hydraulic brakes on your trailer are much like those on your automobile or light truck. The hydraulic fluid from a master cylinder or actuation system is used to actuate the wheel cylinder, which in turn applies force against the brake shoes and drum. The main difference between automotive hydraulic brakes and hydraulic trailer brakes is the trailers' actuation system. These systems respond to the braking signal from the tow vehicle and supply the required brake fluid volume and pressure to the trailer brakes.
The maximum operating pressure for Dexter 12¹⁄₄"
hydraulic brakes is 1,000 PSI.
Braking Systems - Hydraulic
TRIAL MODE − a valid license will remove this message. See the keywords property of this PDF for more information.
Braking Systems - Hydraulic
Hydraulic Drum Brake Operation
The duo-servo brake uses a dual piston wheel cylinder to apply the brakes. This type of brake is typically used in an electric/hydraulic, vacuum/hydraulic, or air/hydraulic system. A description of operation of this brake is as follows:
When the brakes are applied, the double-acting wheel cylinder moves the primary
and secondary shoes
towards the drum. The
frictional force between
the brake drum and lining attempts to turn
the primary shoe into the secondary shoe. The secondary shoe is Secondary
forced onto the anchor
pin and from this point, the secondary and
Adjuster Assembly
primary shoes attempt to "wrap around". In essence, the brake has utilized frictional force to help the applying force on both shoes.
If the brakes are applied while the vehicle is backing, the shoes rotate in the direction of the drum rotation. This causes the secondary shoe to leave the anchor and causes the primary shoe to move against the anchor. Action of the brake is the same in reverse as forward.
TRIAL MODE − a valid license will remove this message. See the keywords property of this PDF for more information.
This type of hydraulic brake utilizes a single acting cylinder. Upon actuation, the primary shoe is pressed
against the brake
drum, which causes
the shoe to move in the direction of rotation.
This movement in turn actuates the secondary shoe through the
adjuster link assembly.
Braking in reverse is significantly less
Adjuster Assembly
effective than in the forward direction. Uni-servo brakes are normally used with surge type actuators.
Self Adjusting Mechanism
for 12¼" Hydraulic Brakes
Forward self-adjust hydraulic brakes were introduced in March, 1997. This feature adjusts the brakes on both forward and reverse stops. Brake adjustment occurs only when lining wear results in enough gap between the shoes and the drum surface. This added clearance will allow the adjuster mechanism to rotate the screw assembly at the bottom of the brake. That action expands the distance between the shoes and thus closes the gap to the drum surface.
Hydraulic Parking Brake Option
The parking feature on Dexter hydraulic brakes is cable operated. The cable end is attached to the internal parking brake lever to actuate the brake. On Dexter 12¹⁄₄" brakes manufactured before February 2002, the parking cable body mounts to a support plate which is attached to the brake mounting flange. The cable end is routed through the dust shield and the brake spider to attach to the internal parking brake lever. For 12¹⁄₄" brakes produced after
Braking Systems - Hydraulic February 2002, a short cable is installed directly into the backing
plate to provide a convenient means for the trailer manufacturer to attach an appropriate operating system.
TRIAL MODE − a valid license will remove this message. See the keywords property of this PDF for more information.
Braking Systems - Hydraulic
The internal parking brake lever of Dexter 12¹⁄₄" brakes transfers the applied cable force through a cam mechanism. The cam mechanism generates a spreading force between the primary and secondary shoes. The shoes move toward the drum until contact is made. Friction generated between the drum and lining contact surface results in parking brake capability.
TRIAL MODE − a valid license will remove this message. See the keywords property of this PDF for more information.
Hydraulic Disc Brakes
Dexter Axle manufactures two types of disc brakes, the floating caliper and the fixed caliper brake. With both styles, the disc brake uses friction pads astride a ventilated rotor which is attached to the wheel hub. When the brake is actuated, the pads are pressed against the sides of the rotor causing drag to slow the rotating disc. This action converts the kinetic energy (motion) into heat. The heat is dissipated rapidly by the ventilated disc.
The floating caliper brake uses piston(s) situated on one side of the brake rotor. Hydraulic fluid pressure pushes against the piston(s) to apply the inboard brake pad. As the inboard pad exerts force against the rotating rotor surface, the caliper moves laterally towards the trailer frame and in turn applies an equivalent force to the outboard brake pad against the rotor surface. As the lining material wears, the caliper will automatically maintain the proper lining to rotor clearance. The floating caliper design is used on Dexter 10,000 and 12,000 lb. axle models.
Disc brake effectiveness is the same going either in a forward or reverse direction. All Dexter disc brakes should be actuated with a braking system that is capable of providing a maximum hydraulic pressure of 1,600 psi.
Braking Systems - Hydraulic
TRIAL MODE − a valid license will remove this message. See the keywords property of this PDF for more information.
Braking Systems - Hydraulic
To effectively operate your hydraulic trailer brakes, we recommend the Dexter E/H electro/hydraulic actuator, controlled by the Predator DX2® electronic brake controller. These high performance hydraulic power modules will supply pressurized brake fluid to your trailer brakes in proportion to the amount of braking effort called for by the towing vehicles' deceleration rate.
It is the responsibility of the end user to ensure that
their in-cab electronic controller is compatible with the
Dexter E/H actuator. Dexter Axle attempts to provide
compatibility with most controllers available, but is
unable to anticipate design changes that might be
introduced by the various controller manufacturers.
The E/H 1000 will supply 1,000 psi for your drum brakes and the E/H 1600 will generate 1,600 psi for maximum output for your Dexter disc brakes. The sealed, weather tight housing contains the electronics necessary to control the high pressure piston pump and proportioning valve for smooth, efficient braking.
The basic actuation system consists of a vacuum booster, synchronizing valve, check valve and a plumbing kit which includes all lines and fittings. A vacuum supply from the engine manifold is routed to the front of the booster and the top chamber of the synchronizing valve through flexible hoses. The rear of the booster and the lower chamber of the synchronizing valve are connected by a separate line. The vacuum from the engine must pass through a normally closed check valve. The check valve keeps gas vapor out of the system and insures that the highest vacuum available will be kept in the system. With the engine running and with no brake pedal pressure, a vacuum exists throughout the system. The synchronizing valve is connected to the master cylinder hydraulic supply. When the brake pedal is applied, the hydraulic pressure in the synchronizing valve forces a poppet to open which allows atmospheric air to enter the bottom
TRIAL MODE − a valid license will remove this message. See the keywords property of this PDF for more information.
chamber of the valve. Since this part of the valve is connected to the rear of the vacuum booster, the vacuum on this side of the booster chamber is lost. The vacuum on the front side of the booster chamber is maintained and this atmospheric/vacuum pressure differential causes a piston to move in the booster's slave cylinder. This piston applies the hydraulic pressure to the brakes through the connecting hydraulic line. When the pedal is released, the poppet in the synchronizing valve is closed and by internal passages, the air in the rear of the booster chamber is removed. This restores a vacuum which is equal to the vacuum in the front part of the booster chamber. The pressure balance allows the slave cylinder piston to be pulled back to its original position and the hydraulic pressure to the brakes is released.
Air/hydraulic braking systems are commonly used when the tow vehicle has a diesel engine which does not develop manifold vacuum. The air/hydraulic tow vehicle has an air compressor mounted on the engine to supply compressed air for the braking system and other needs required by the tow vehicle trailer combination. This air is routed to a booster chamber attached to the trailer master cylinder. The air pressure multiplies hydraulic output pressure which then sends fluid to the wheel cylinders. The air over hydraulic systems are often controlled by a series of control valves and servos to insure proper braking under all conditions.
Braking Systems - Hydraulic
TRIAL MODE − a valid license will remove this message. See the keywords property of this PDF for more information.
Braking Systems - Hydraulic
Introduction to Troubleshooting
Proper brake function is critical to the safe operation of any vehicle. A properly installed vacuum/hydraulic, electric/hydraulic, or air/hydraulic system should not require any special attention with the exception of routine maintenance as defined by the manufacturer. If problems occur, the entire tow vehicle/trailer braking system should be analyzed by a qualified mechanic. Typical problems in a hydraulic braking system are:
• Air or vacuum leaks
• Hydraulic system leaks
• Air in brake lines
• Water or other impurity in brake fluid
• Rusted or corroded master or wheel cylinders
• Actuation system malfunction
Please consult the following troubleshooting charts to determine the causes and solutions for common problems found in trailer braking systems.
TRIAL MODE − a valid license will remove this message. See the keywords property of this PDF for more information.
Lack of Lubrication
Noisy Brakes
Broken Brake
Loose, Bent or Broken
Machine or Replace
Inflate Evenly on Both
Sides to Req. Pressures
Pulls to One Side
Match Tires on Axle
on Same Axle
Repair or Replace
Lines or Hoses
Check for Stuck
or Sluggish Pistons
Defective or Damaged
Install New Shoe and
Shoe and Lining
Replace Rubber Parts
Fill with DOT4 Fluid
Open with Compressed
Air or Replace Cylinder
Free Cable
Cable Frozen
Install New Shoes
Thickness or Location
and Linings
Braking Systems - Hydraulic
TRIAL MODE − a valid license will remove this message. See the keywords property of this PDF for more information.
Braking Systems - Hydraulic
Broken or Kinked
Repair or Replace
Brake Line
No Brakes
Not Correct
Replace Shoe
and Lining
Install Correct
Shoe and Lining
Repair Grease Seal or
Grease or Fluid
Wheel Cylinder. Install
New Shoe and Lining.
Frozen Master Cylinder
Recondition or Replace
or Wheel Cylinder Pistons
All Cylinders, Brake Fluid
Weak Brakes
Reburnish or Replace
Excessive Drum Wear
Trapped Air in Lines
Bleed System
Not Correct
Harsh Brakes
Grease or Fluid
on Linings
and Linings
Grease or Oil
Clean or Replace
on Linings
Out of Round Drums or
Machine or Replace
TRIAL MODE − a valid license will remove this message. See the keywords property of this PDF for more information.
Vehicle Controller
Note: Either an onboard or breakaway
battery may be used.
Brakes are slow to respond
1. Re-bleed the trailer brakes and actuator.
2. If the trailer is equipped with drum brakes, readjust the drum
brakes to the brake manufacture's recommended running clearance.
3. Slow response can be caused by trailer wiring that is too
4. For trailers where the E/H unit is located less than 10 feet
from the tow vehicle, 12 gage wire is recommended for the black and white wires between the tow vehicle and the E/H unit. All other wires should be a minimum of 16 gauge.
5. For trailers where the E/H unit is located more than 10 feet
from the tow vehicle, 10 gage wire is recommended for the black and white wires between the tow vehicle and the E/H unit. All other wires should be a minimum of 16 gauge.
6. Slow response can be caused by improper adjustment
of the brake controller. On inertia-based electronic brake controls, adjust the pendulum (inertia sensor) to a more
Braking Systems - Hydraulic
aggressive setting and/or increase the gain setting.
TRIAL MODE − a valid license will remove this message. See the keywords property of this PDF for more information.
Braking Systems - Hydraulic
Unit will not run when the ignition is on and the brake pedal
is depressed
1. Verify that the trailer and tow vehicle are wired as detailed
on the electrical schematic.
2. With the ignition switch on and the brakes not applied, you
should have 12-13 volts between the black and white wires on the E/H unit.
3. Clean and replace the ground between the trailer and the
4. Test operation of the unit using the breakaway test
Breakaway test procedure - do not leave the breakaway
switch pulled for more than two minutes during any of the
steps outlined below
1. Pull the breakaway switch on the trailer.
2. If the unit runs and builds pressure, that indicates the
actuator is functioning properly. The problem most likely is a defective electronic brake controller in the tow vehicle or defective wiring between the tow vehicle and the E/H unit.
3. If the unit runs but will not build pressure, the problem most
likely is a defective solenoid valve in the E/H unit and the actuator should be returned for repair.
4. If the unit still does not run after the breakaway battery is
fully charged, verify that the voltage between the white wire and yellow wire is at least 12 volts.
5. If the voltage is less than 12 volts, either the breakaway
switch or the breakaway wiring is defective.
6. If the voltage is greater than 12 volts, the E/H unit should be
returned for repair.
Trailer brakes too aggressive
1. Reduce the gain setting on the in-cab electronic brake
TRIAL MODE − a valid license will remove this message. See the keywords property of this PDF for more information.
General Maintenance - Hydraulic Brakes
Drum Brake Adjustment
Most Dexter 12¹⁄₄" hydraulic brakes have a self adjusting feature. If manual adjusting is required, use the following procedure:
Brakes should be adjusted (1) after the first 200 miles of operation when the brake shoes and drums have "seated," (2) at 3,000 mile intervals, (3) or as use and performance requires. The brakes should be adjusted in the following manner:
1. Jack up trailer and secure on adequate capacity jack stands.
Follow trailer manufacturer's recommendations for lifting and supporting the unit. Make sure the wheel and drum rotates freely.
! CAUTION
Do not lift or support the trailer on any part of the axle
or suspension system. Never go under any trailer unless
it is properly supported on jack stands which have been
rated for the load. Improperly supported vehicles can
fall unexpectedly and cause serious injury or death.
2. Remove the adjusting hole cover from the adjusting slot on
the bottom of the brake backing plate.
3. With a screwdriver or standard adjusting tool, rotate the star
wheel of the adjuster assembly to expand the brake shoes. Adjust the brake shoes out until the pressure of the linings against the drum makes the wheel very difficult to turn.
4. Then rotate the star wheel in the opposite direction until the
wheel turns freely with a slight lining drag.
5. Replace the adjusting hole cover and lower the wheel to the
6. Repeat the above procedure on all brakes. For best results,
the brakes should all be set at the same clearance.
Braking Systems - Hydraulic
TRIAL MODE − a valid license will remove this message. See the keywords property of this PDF for more information.
Braking Systems - Hydraulic
Most of the brake components are very similar to those used in electric brakes, and maintenance is comparable for the hub and drum, shoes and linings, and bearings. Specific maintenance activities are as follows:
Inspect for leaks and smooth operation. Clean with brake cleaner and flush with fresh brake fluid. Hone or replace as necessary.
Check for cracks, kinks, or blockage. Flush with fresh brake fluid. Bleed system to remove all air. Use DOT3 or DOT4 brake fluid, and replace as necessary.
Shoes and Linings
A simple visual inspection of your brake linings will tell if they are usable. Replacement is necessary if the lining is worn (to within ¹⁄₁₆" or less), contaminated with grease or oil, or abnormally scored or gouged. Hairline heat cracks are normal in bonded linings and should not be cause for concern. When replacement is necessary, it is important to replace both shoes on each brake and both brakes of the same axle. This will help retain the "balance" of your brakes.
! CAUTION
POTENTIAL ASBESTOS DUST HAZARD!
Some older brake linings may contain asbestos dust,
which has been linked to serious or fatal illnesses.
Certain precautions need to be taken when servicing
brakes:
1. Avoid creating or breathing dust.
2. Avoid machining, filing or grinding the brake linings.
3. Do not use compressed air or dry brushing for
cleaning (dust can be removed with a damp brush).
TRIAL MODE − a valid license will remove this message. See the keywords property of this PDF for more information.
After replacement of brake shoes and linings, the brakes must be re-burnished to seat in the new components. This should be done by applying the brakes 20 to 30 times from an initial speed of 40 m.p.h., slowing the vehicle to 20 m.p.h. Allow ample time for brakes to cool between applications. This procedure allows the brake shoes to seat in to the drum surface.
Check all hardware. Check shoe return spring, hold down springs, and adjuster springs for stretch or wear. Replace as required. Service kits are available.
Instructions for 10-12K
Hydraulic Disc Brakes
Notice to Buyer
It is recommended that all brakes be replaced at the same time to
insure balanced braking performance.
1. Jack up trailer and secure on adequate capacity jack stands.
Follow trailer manufacturers recommendations for lifting and supporting the unit.
! CAUTION
Do not lift or support the trailer on any part of the axle
or suspension system. Never go under any trailer unless
it is properly supported on jack stands which have been
rated for the load. Improperly supported vehicles can fall
unexpectedly and cause serious injury or death.
2. Remove the wheel from the hub, leaving the brake exposed.
Removal of Old Brake Caliper
1. With tire-wheel assembly(s) removed from hub and zero
pressure in hydraulic system, remove hex nuts from slider bolts and withdraw bolts from brake assembly. Note orientation of anti-rattle springs. Lift calipers from assembly and secure to prevent damage to brake hose. Do not allow
Braking Systems - Hydraulic
caliper to hang from the hose. Remove anti-rattle springs and brake pad.
TRIAL MODE − a valid license will remove this message. See the keywords property of this PDF for more information.
Braking Systems - Hydraulic
1. Slider bolts must be straight and free of rust pits, missing
chrome, or cracks in the chrome plating. Replace if necessary. Anchor yoke bores must be free of corrosion and excessive wear. "O" rings must be free from nicks and cuts. Replace as necessary. Caliper assembly must be free of fluid leaks and torn or deteriorated dust boots and "O" rings. Repair as required.
2. Rotor-inspect for grooves, flaking, cracks, heat checking,
excessive thickness variation, insufficient overall rotor thickness and overall width (measurement from inboard rotor face to rotor mounting surface). Machine or replace as necessary.
3. Rotor Specifications:
1.185 New, 1.12 Min. Service Limit
2.15 New, 2.09 Service Limit
Rotor Overall Width
3.655 New, 3.59 Service Limit
.003 T.I.R., .010 T.I.R. Maximum
Thickness Variation
Hub and Rotor Removal and Installation
1. With hubcap removed and oil drained, straighten locking
tabs on tang washer and remove outer locknut, tang washer, inner locknut, bearing washer, and outer bearing. Remove hub and rotor assembly.
Note: A puller may be required due to unitized seal press
fit on spindle. Remove inner bearing and seal. Service
bearings as necessary.
2. Prior to reassembly, insure that the hub bearing housing
is clean. Reinstall inner bearing. Coat the O.D. of a new seal with a bore sealant (Permatex or equivalent) prior to installation.
3. Mount hub and rotor assembly on spindle and install outer
bearing, bearing washer, and inner bearing nut.
TRIAL MODE − a valid license will remove this message. See the keywords property of this PDF for more information.
4. Tighten inner nut to 100 Ft. Lbs. while turning hub to seat
5. Loosen nut to remove pre-load torque. Hand tighten nut,
then back off ¹⁄₈ turn minimum, ¹⁄₄ turn maximum.
6. Install tab washer and outer locknut. Torque locknut to
100-175 Ft. Lbs. Insure that the inner nut does not rotate.
Bend 2 tabs over flat on outer locknut to secure.
7. Install hub cap and add oil to hub. Capacity is 2.5 oz. of SAE
90W gear oil.
1. Installation is reverse of disassembly. Use appropriate tools
and methods to retract caliper pistons sufficiently to reinstall caliper over the new pads. Caliper and anchor yoke "O" rings should be lubricated with a light film of high temperature brake lubricant prior to slider bolt installations. Slider bolts should be installed from the outboard side of the caliper. Insure the anti-rattle springs are located properly.
2. Use extreme care when installing the slider bolts to prevent
damage to the "O" rings. Installation tool #071-182-00 threaded onto the slider bolts is recommended.
3. DO NOT FORCE OR HAMMER BOLTS IN. Secure slider
bolts with new locknut. Actuate brakes numerous times to remove excess pad clearance prior to operation of vehicle.
Slider Bolts Locknuts
15-25 Ft. Lbs.
Anchor Yoke Mounting Nuts
45-55 Ft. Lbs.
9-12 Ft. Lbs.
Rotor Mounting Nuts 10K-12K
85-95 Ft. Lbs.
Rotor Mounting Bolts #14 Torflex®
90-110 Ft. Lbs.
Outer Spindle Nuts
100-175 Ft. Lbs.
20-30 Ft. Lbs.
Wheel Mounting Nuts
200 Ft. Lbs.
(with clamp ring)
Braking Systems - Hydraulic
TRIAL MODE − a valid license will remove this message. See the keywords property of this PDF for more information.
Braking Systems - Hydraulic
Hydraulic Disc Brake Parts
Anchor Yoke Assembly 10K-12K
(includes 6 of item #6)
Anchor Yoke Assembly #14 Torflex®
(includes 6 of item #6)
(includes items #6, 3, 9, 10)
Shoulder Screw ⁵⁄₈ x 5
Hex Screw ⁷⁄₁₆-20 x 1.75
Hex Nut ⁷⁄₁₆-20
Rotor Mounting Stud
ABS Sensor (straight)
ABS Sensor Retaining Clip
Caliper Repair Kit contains:
Disc Brake Replacement Pad Kit contains:
Anti-Rattle Spring
Installation Tool
Recommend hose with banjo fitting. ⁷⁄₁₆-20 threaded hole for fitting.
TRIAL MODE − a valid license will remove this message. See the keywords property of this PDF for more information.
S-Cam Air Brakes
Trailer air brakes are operated by the tractor air supply through a series of relay and check valves. When braking is desired, the air is supplied to the axle air chamber which applies a force that is multiplied by the slack adjuster lever arm length. This force is transmitted rotationally through the camshaft which, through the geometry of the S-head, spreads the brake shoes to contact the brake drum surface. The air brake systems are an effective, very durable braking system for use in high mileage or extreme operating conditions. They can be outfitted with ABS (anti-lock brake systems), automatic slack adjusters and spring brakes to comply with Federal Motor Vehicle Safety Standard Part 571.121.
Push RodLength@ Rest
Braking Systems - Air
TRIAL MODE − a valid license will remove this message. See the keywords property of this PDF for more information.
Braking Systems - Air
Air Brake Components
The air chambers convert the compressed air into a mechanical force on the slack adjuster. The force on the slack adjuster operates on the end of the lever and converts the chamber output force to a torque on the S-cam. Federal and state regulations state the maximum pushrod stroke length as an indication of brake adjustment. This stroke is shown by the maximum stroke indicator located on the air chamber pushrod. Maximum allowable stroke is achieved when the indicator is fully extended from the air chamber housing.
Note: Due to manufacturing tolerances, some brakes may not
meet the maximum stroke length in the "green" state and may
require several burnish stops to allow the brake shoes to conform
to the drum diameter.
For parking and emergency braking purposes, a spring brake chamber can be used in conjunction with the standard air chamber. The spring brake contains an additional air diaphragm and a very strong spring. When air is applied to the spring brake, the spring is held in the off position by the air diaphragm. When the air is exhausted, the spring provides the braking force to the air chamber pushrod, thus actuating the brakes.
! CAUTION
Do not disassemble the spring brake! It contains a
compressed spring that may cause injury if removed.
The spring brake must be caged before servicing and
should only be performed by qualified personnel.
TRIAL MODE − a valid license will remove this message. See the keywords property of this PDF for more information.
The air brake slack adjusters perform two functions: (1) The slack adjuster acts as a lever arm to convert the linear pushrod force to rotational camshaft torque. The length of the slack adjuster determines the amount of torque multiplication provided from the pushrod. (2) Allows a simple external adjustment of the lining to drum clearance to compensate for shoe lining wear.
There are two types of slack adjusters, manual and automatic:
Manual slack adjusters
The manual slack adjusters require manual adjustment to
compensate for the brake lining wear and the associated drum to
lining gap that results. Adjustment is usually performed by rotating
the hex adjusting nut on the slack adjuster body to set a lining to
drum clearance of about .020-.030". See instructions for manual
slack adjustment procedure.
Automatic slack adjuster
The automatic slack adjuster (ASA) maintains an optimum
clearance between the brake lining and the drum by automatically
adjusting on the return stroke during brake application. Various
brands of ASA's may work differently. The initial adjustment and
set-up of the ASA's is critical to proper function of the air brake.
See instructions for slack adjuster procedure.
Note: Automatic slack adjusters are required on some commercial
trailers over 26,000 lbs., manufactured after 10/20/94 per FMVSS
Part 571.121. DO NOT REPLACE AUTOSLACKS WITH MANUAL
SLACK ADJUSTERS ON THESE TRAILERS.
The S-cams rotate from the torque applied by the slack adjusters, resulting in spreading the brake shoes which applies the braking force to the drum. The S-cams are supported by two nylon, grease lubricated bushings. Due to the high forces exerted on the cam bushings, periodic inspection, lubrication and maintenance is required to achieve proper braking performance.
Braking Systems - Air
TRIAL MODE − a valid license will remove this message. See the keywords property of this PDF for more information.
Braking Systems - Air
The air brake shoes are the final link in the braking system. The brake shoes are supported by pins inserted into the brake spider, and rollers that contact the S-cam surface. The shoes have a replaceable lining riveted to them. The linings have two different blocks, designated Cam and Anchor side. The brake shoes on your Dexter axle are specifically designed for that axle. Only Dexter authorized parts should be used for replacement since there are small dimensional differences between air brake parts suppliers that can significantly affect the function of the brake.
! CAUTION
Improperly fitted brake parts can cause brakes to
malfunction and cause loss of braking and/or wheel
lockup. Loss of braking can cause an accident resulting
in injuries or death.
TRIAL MODE − a valid license will remove this message. See the keywords property of this PDF for more information.
Brake Component Lubrication
Camshaft bushings
Lubricate with approved grease through the grease fittings at the
spider and camshaft support bracket locations. Apply just enough
grease so grease is visible flowing past camshaft bushing seals.
During this process it is advisable to grab the camshaft and shake
the camshaft to see if there is excessive clearance in the camshaft
bushings due to wear.
Camshaft roller journals and brake anchor pins
These components are to be lubricated with a high temperature
anti-seize grease upon disassembly, maintenance and
reassembly.
Manual and automatic slack adjusters
Lubricate with Lithium base NLGI Grade 1 anti-wear grease
with rust and oxidizer additives applied at intervals of 3 to 6
months or 50,000 miles or per slack adjuster manufacturer's
recommendations.
For Manual Slack Adjusters
Lubricate with NLGI Grade 2
For Automatic Slack Adjusters
Lubricate with ASA manufacturers
recommended lubricant
Anchor Pins
and Roller Journals
Spider and
Lubricate with high
temperature anti-seize
Lubricate with NLGI
Braking Systems - Air
TRIAL MODE − a valid license will remove this message. See the keywords property of this PDF for more information.
Braking Systems - Air
12¹⁄₄" Quick Change Brakes - PQ
1. Block and secure trailer on adequate capacity jack stands.
Follow trailer manufacturers recommendations for lifting and supporting the unit. Check that the wheel and drum rotate freely.
2. Release brake and back off slack adjuster.
3. Remove wheel equipment.
4. Lift top shoe upward to disengage the shoe webs from the
anchor pin. Remove anchor pin.
5. Repeat procedure 4 for the bottom shoe.
6. Remove brake keeper springs.
7. Unwrap bottom shoe by pivoting the shoe on the camshaft
head and twisting the shoe 90° under the spindle. Remove shoe assemblies from spider.
8. Remove slack adjuster lock ring, disconnect slack clevis,
and then remove slack adjuster.
9. Remove camshaft lock ring, spacer washer(s) and camshaft.
10. Completely inspect all brake components, servicing as
1. Install new camshaft bushing. Ream bushing to 1.505/1.515
if required. Install camshaft seals into the spider.
Note: When installing camshaft seals, the seal on the slack
adjuster side is installed with seal facing into spider. This
allows grease to purge outside the brake assembly when
greasing the camshaft bushing. It also aids to avoid damage
of the seal lip when camshaft is installed.
2. Install new cam roller assemblies onto the brake shoes.
Note: The head of roller pin should face the camshaft "D"
washer once shoes are installed on spider.
TRIAL MODE − a valid license will remove this message. See the keywords property of this PDF for more information.
3. Install "D" shaped camshaft washer onto the camshaft.
4. Install the camshaft into the spider. Install 005-075-00
washer and lock ring retainer on the camshaft before sliding the camshaft through the camshaft support bracket.
5. Install the slack adjuster and 005-134-00 washer and
069-078-00 lock ring retainer for 28 spline camshafts or 005-075-00 washer and 069-020-00 lock ring retainer for 10 spline camshafts.
6. Lubricate cam roller notches with anti-seize lubricant prior to
installing cam roller assemblies onto the brake shoes. Bend roller retainer loop down so that retainer will be at same level as the shoe table and will not interfere with the brake drum during the life of the lining blocks.
7. Install "W" shaped retractor spring retainer pin into the 0.50"
diameter shoe web holes near the camshaft roller end of the shoe.
8. Install retractor spring between shoes. Place top shoe onto
spider as in service. Pivot bottom shoe on the camshaft head and twist the shoe 90° under the spindle, properly placing shoe on the spider as in service.
9. Install two (2) keeper springs on the anchor end of the
10. Lubricate anchor pin bores and shoe anchor pins with
11. Repeat procedure 10 for the bottom shoe.
12. Lift top shoe upwards to clear anchor pin hole. Install anchor
13. Connect slack adjuster to brake chamber pushrod.
Note: Always use new springs when servicing brakes.
Always use Dexter shoes when replacing shoes.
Braking Systems - Air
TRIAL MODE − a valid license will remove this message. See the keywords property of this PDF for more information.
Braking Systems - Air
Air Brake Automatic Slack Adjustment
Mounting and adjustment procedure
If available, use installation template per manufacturer's directions.
If template is not available, use the following procedure:
1. Install air chamber with proper push rod length.
2. Install the slack onto the camshaft.
3. Adjust the slack arm up to the point where the slack arm
starts to engage into the clevis slot.
4. Take the ¹⁄₂" diameter pivot pin, and place it into the clevis
slot. Hold in place (at this point, the pin is like a shim).
5. Continue adjusting the slack arm back against the pin.
6. When the slack arm touches the pin, the slack rotation will
stop. The camshaft will start to rotate as you keep adjusting the slack with the wrench.
7. Continue adjusting with the wrench, which is now bringing
the shoes into closer contact with the drum.
8. As you continue to adjust, spin the drum by hand to get a
feel for the brake drag.
9. Adjust until the drum stops.
10. Adjust an additional ¹⁄₄ to ¹⁄₂ turn of the wrench.
11. Pull slack away by hand, from the pin.
12. Remove the pin from the clevis slot.
13. Align ¹⁄₂" holes.
14. Insert ¹⁄₂" pin.
15. Make sure the drum rotates one (1) full revolution. If it
did, proceed to step sixteen (16). If it did not rotate one revolution, remove the air chamber and slack. Start over at step one (1). Do not tighten the adjuster hex nut as tight as previously done.
16. Insert the ¹⁄₄" pin.
17. Install and secure the cotter pins in the clevis and adjuster
TRIAL MODE − a valid license will remove this message. See the keywords property of this PDF for more information.
! CAUTION
To insure brakes meet Federal performance
requirements, Dexter Axle recommends that only
original equipment premium grade linings be used.
Failure to use proper linings can result in poor braking
and cause accidents and injuries.
Air Brake Manual Slack Adjustment
1. Grease cam bracket and spider fittings.
2. Adjust the slack adjuster until the brake lining comes into
contact with the brake drum.
A. For green brakes, there should be a slight amount of
wheel drag at initial adjustment to compensate for any lining irregularities such as high spots.
B. For burnished or broken-in brakes, back off the slack
adjuster to achieve .010" clearance between the drum and shoes.
3. Apply brakes using normal truck operating pressure
(80-90 psi).
Note: A "green brake" is an unground, unburnished, brake.
Normal manufacturing tolerances dictate that there is a
break-in period required after which the lining will seat into
the brake drum. During this break-in period, the user must
be aware that additional brake adjustment will be mandatory
to achieve optimum braking performance.
USE OF AIR PRESSURE IN EXCESS OF 130 PSI COULD
RESULT IN FAILURE OF THE AIR CHAMBER OR SPRING
BRAKE CHAMBER.
Braking Systems - Air
TRIAL MODE − a valid license will remove this message. See the keywords property of this PDF for more information.
Braking Systems - Air
4. Check the amount of push rod travel at the clevis pin. The
stroke should be as follows:
Chamber Type
5. With air pressure applied to brakes, check for lining to drum
contact. The contact should approach 100%. Use a .010" feeler gage if in doubt. It should not fit between the lining and drum during brake application.
6. Release air pressure from the brakes and confirm that all
brakes release to the normal relaxed position.
A. When properly adjusted, the angle between the push rod
and the slack adjuster should be approximately 90° +/- 5° when the brakes are applied.
B. Proper maximum stroke should be achieved after
adjusting the autoslack. Reference the push rod stroke length chart.
TRIAL MODE − a valid license will remove this message. See the keywords property of this PDF for more information.
Introduction to Troubleshooting
Proper brake function is critical to the safe operation of any vehicle. A properly installed air brake system should not require any special attention with the exception of routine maintenance as defined by the manufacturer. If problems occur, the entire tow vehicle/trailer braking system should be analyzed by a qualified mechanic.
To assure safe operation and maximum durability of parts such as brake linings and tires, it is necessary to position and install the axle properly. It is recommended that the axle assembly be installed so that camshafts rotate in the same direction as the wheels. Installation in which the camshaft rotation is opposite that of wheel rotation could cause noisy brakes, chatter, and wheel "hop". With this thought in mind, the axle should be ordered with placement of air chamber and slack adjuster assemblies that will insure the correct directional rotation of the camshafts when the axle is installed.
It is the responsibility of the axle installer to adjust the brakes properly. The recommended adjustment procedure is covered in the section pertaining to brakes.
Please consult the following troubleshooting charts to determine the causes and solutions for common problems found in trailer braking systems.
Braking Systems - Air
TRIAL MODE − a valid license will remove this message. See the keywords property of this PDF for more information.
Braking Systems - Air
Replace Linings
and Drum If Needed
Air System
Troubleshoot per
System Mfgr's Directions
Brakes Out of
No Brakes
Air Lines
Kinked or Broken
Repair or Replace
Air Chamber
Brakes Out of
Excessive Drum Wear
Excessive Lining Wear
Oil Soaked Linings
Weak Brakes
Use Proper Load
Air System Malfunction
Troubleshoot per
System Mfgr's Directions
Wrong Size
Use Correct Size Air
Air Chamber
Chamber for Application
Worn Anchor Pin
Bushings or
Not Correct
Harsh Brakes
Oil on Linings
Wrong Brake
Use Only Approved
TRIAL MODE − a valid license will remove this message. See the keywords property of this PDF for more information.
Cams Froze in
Wrong Size
Use Correct Size
Air Chamber
Air Chamber
Use Correct Length
Air System Timing
Malfunction
- Too Low Relay Valve
System Mfgr's
- Quick Release Valve
S-Cam Flipped Due to
Brake Lining Wear
Determine Cause of
Breakage and Replace
Grease or Oil
on Linings
Out of Round
Turn or Replace
or Cracked Drums
Linings Dragging Due to
Weak or Broken
Wrong Component in
Use Only Dexter
Air System Malfunction
Troubleshoot per
Sticky Valves, Dirt, etc.
System Mfgr's Directions
Improper Mounting of
Mount per
Air Chamber and
Recommended
Camshaft or Shoes
Braking Systems - Air
TRIAL MODE − a valid license will remove this message. See the keywords property of this PDF for more information.
Whenever the hub equipment on your axle must be removed for inspection or maintenance the following procedure should be utilized.
1. Elevate and support the trailer unit per manufacturers'
! CAUTION
Do not lift or support the trailer on any part of the axle
or suspension system. Never go under any trailer unless
it is properly supported on jack stands which have been
rated for the load. Improperly supported vehicles can
fall unexpectedly and cause serious injury or death.
2. Remove the wheel(s).
3. Remove the grease or oil cap by unscrewing it
counterclockwise while holding the hub stationary.
4. Bend the locking tang down from the outer spindle nut and
remove spindle nut.
5. Remove the tang washer and unscrew the inner spindle nut
(counterclockwise) and remove the spindle washer.
6. Remove the hub from the spindle, being careful not to allow
the outer bearing cone to fall out. The inner bearing cone will be retained by the seal.
Note: A gear puller may be necessary to remove hub from
spindle.
Brake Drum Inspection
There are two areas of the brake drum that are subject to wear and require periodic inspection. These areas are the drum surface where the brake shoes make contact during stopping and the armature surface where the magnet contacts (only in electric brakes).
TRIAL MODE − a valid license will remove this message. See the keywords property of this PDF for more information.
The drum surface should be inspected for excessive wear or heavy scoring. If worn more than .020" oversized, or the drum has worn out of round by more than .015", then the drum surface should be re-machined. If scoring or other wear is greater than .090" on the diameter, the drum must be replaced. When turning the drum surface, the maximum rebore diameter for a 12¹⁄₄" brake drum is 12.340".
For electric brakes only, the machined inner surface of the brake drum that contacts the brake magnet is called the armature surface. If the armature surface is scored or worn unevenly, it should be refaced to a 120 micro inch finish by removing not more than .030" of material. To insure proper contact between the armature face and the magnet face, the magnets should be replaced whenever the armature surface is refaced and the armature surface should be refaced whenever the magnets are replaced.
Note: It is important to protect the wheel bearing bores from
metallic chips and contamination which result from drum turning or
armature refacing operations. Make certain that the wheel bearing
cavities are clean and free of contamination before reinstalling
bearing and seals. The presence of these contaminants will cause
premature wheel bearing failure.
Wash all grease and oil from the bearing cone using a suitable solvent. Dry the bearing with a clean, lint-free cloth and inspect each roller completely. If any pitting, spalling, or corrosion is present, then the bearing must be replaced. The bearing cup inside the hub must be inspected.
IMPORTANT: Bearings must always be replaced in sets of a cone
and a cup.
! CAUTION
Be sure to wear safety glasses when removing or
installing force fitted parts. Failure to comply may result
in serious eye injury.
TRIAL MODE − a valid license will remove this message. See the keywords property of this PDF for more information.
When replacing the bearing cup proceed as follows:
1. Place the hub on a flat work surface with the cup to be
replaced on the bottom side.
2. Using a brass drift punch,
carefully tap around the small diameter end of the cup to drive out.
3. After cleaning the hub
bore area, replace the cup by tapping in with the brass drift punch. Be sure the cup is seated all the way up against the retaining shoulder in the hub.
Replace only with bearings as specified in the Bearing Replacement Chart.
Bearing Lubrication - Grease
Do not mix Lithium, calcium, sodium or barium complex
greases due to possible compatibility problems.
When changing from one type of grease to another,
it is necessary to insure all the old grease has been
removed.
Grease should be replaced every 12,000 miles or 12 months. Prior to repacking bearings, all old grease should be removed from the wheel hub cavity and bearings. Bearings should be packed by machine if possible. If a machine is unavailable, packing by hand method is acceptable. The method to pack bearing cones is as follows:
1. Place a quantity of grease onto the palm of your hand.
TRIAL MODE − a valid license will remove this message. See the keywords property of this PDF for more information.
2. Press a section of the widest end of bearing into the outer
edge of the grease pile closest to the thumb forcing grease into the interior of the bearing between two adjacent rollers.
3. Repeat this while rotating the
bearing from roller to roller.
4. Continue this process until you
have the entire bearing completely filled with grease.
5. Before reinstalling, apply a light
coat of grease onto the bearing cup mating surface.
Bearing Lubrication - Oil
If your axles are equipped with oil lubricated hubs, then your lubrication procedure is to periodically fill the hub with a high quality hypoid gear oil to the level indicated on the clear plastic oil cap. The oil can be filled through the rubber plug hole in the cap. Oil should be replaced every 12 months or 12,000 miles.
TRIAL MODE − a valid license will remove this message. See the keywords property of this PDF for more information.
Recommended Wheel Bearing
Lubrication Specifications
215°C (419°F) Minimum
EP, Corrosion & Oxidation Inhibitors
Approved Grease Sources
76 Lubricants/Kendall
L427 Super Blu Grease
Lithoplex MP #2Lithoplex CM #2Lithoplex Red MPMystik JT-6 Hi-Temp Grease #2
Exxon/Mobil Company
Ronex, MPMobilith AW 2Mobil I Synthetic Grease
Oil Center Research
Liquid-O-Ring No, 167L
Pennzoil-Quaker State
Synthetic Red Grease
Gadus S3 V220CGadus S5 V220Rotella Heavy Duty Lithium Complex #2
Royal Mfg. Company
Royal 98 Lithium Complex EP #2
Chevron Ulti-Plex Grease EP #2Texaco Starplex Moly MPGM #2
Valvoline Multi-Purpose GMValvoline Durablend
Great Plains Lubricants
Lithium Complex EP #2
TRIAL MODE − a valid license will remove this message. See the keywords property of this PDF for more information.
SAE 90, SAE 80W-90, SAE 75W-90
Approved Oil Sources
Valvoline Dura BlendValvoline Power Lube
CITGO Petroleum Co.
CITGO Premium Gear Oil MPMystik JT-7Mystik Power Lube
Universal Gear Lubricant 80W-90
Exxon Company USA
Gear Oil GX 80W-90
Industrial Oils Unlimited
Super MP Gear Oil 80W-90
Kendall Refining Co.
Kendall NS-MP Hypoid Gear Lube
Lubriplate Division/
Lubriplate APG 90
Fiske Brothers Refining
Multi-Purpose Gear Oil 80W-90
Mobil Oil Corporation
Mobilube SHCMobil 1 Synthetic Gear Lube
Phillips 66 Petroleum
Superior Multi-Purpose Gear OilPhilguard Gear OilPhilsyn Gear Oil
Pennzoil Products Co.
Gear Plus 80W-90 GL-5Gear Plus Super 75W-90Gear Plus Super EW 80W-90Multi-Purpose 4092 Gear Lube
Oil Center Research
Liquid-O-Ring 750 GX
Sun Refining and
Marketing Company
Shell Oil Company
Spirax ASpirax GSpirax HDSpirax S
Texaco Oil Company
Multigear EPMultigear SS
Multigear Select Gear Oil
Royal Manufacturing
Union Oil Company
Unocal MP Gear Lube76 Triton Syn Lube EP
TRIAL MODE − a valid license will remove this message. See the keywords property of this PDF for more information.
Seal Inspection and Replacement
Whenever the hub is removed, inspect the seal to assure that it is not nicked or torn and is still capable of properly sealing the bearing cavity. If there is any question of condition, replace the seal. Use only the seals specified in the Seal Replacement Chart.
Bad Seal: Nicks and Tears
To replace the seal:
1. Pry the seal out of the hub with a seal removal tool or a
screwdriver. Never drive the seal out with the inner bearing as you may damage the bearing.
2. Apply a sealant similar to PERMATEX® High-Temp Red
RTV Silicone Gasket to the outside of the seal. Use only enough to provide a thin coat to prevent any excess from contaminating the rubber lip(s) of the seal. It is okay to apply a slight amount of lube to the inner rubber lip(s) to aid with installing onto the spindle.
Note: No sealant should be used if the outside of the seal is
rubber coated. For these type of seals it is recommended to
apply a thin coat of oil to the outside rubber.
3. Clean the seal journal of the spindle to inspect for nicks or
roughness. Use a file to remove any burrs from the leading edge or shoulder area. Clean the journal area with very fine emery cloth. Any presence of deep gouges or scratches in this area may cause seal failure allowing lubricant to leak out of the hub.
4, Clean the seal bore in the hub and inspect for any nicks,
gouges, or scratches that may prevent the seal from retaining the bearing lubricant inside the hub.
5. Orient the seal properly. Many oil bath seals will be marked
AIR SIDE on the side of the seal to facing out of the hub after installation.
6. Install new seal into place using a seal driver or seal
installation tool of proper size. It is important that any seal
TRIAL MODE − a valid license will remove this message. See the keywords property of this PDF for more information.
installation tool contact the outer ring of the seal casing. If no seal driver is available, use a clean block of wood. It is critical that the seal be driven in evenly and straight. NEVER hammer directly on the seal.
7. The seals will be pressed flush to the back surface of the
hub in the 9K-10K General Duty axle product line. The seals in the 10K through 15K axles need to be installed so that the airside face of the seal is approximately ¹¹⁄₁₆" from the inner bearing cone. It is NEVER necessary to bottom out the seal for proper installation. Driving the seal in too deep may damage the seal and may come in contact with the inner bearing preventing it from rotating freely.
8. Proper installation will maintain the seal flatness in the hub
within .010". A seal that is cocked too much inside the hub will be more likely to leak.
For ABS installation:
1. Assure that the ABS sensor is pushed fully into its retainer
clip (sensor tip is as far outboard as possible).
2. Install hub and drum squarely to the spindle centerline so
that the exciter ring inside the drum will contact the sensor tip and push it back to the proper sensor to exciter ring running clearance (gap should not exceed ¹⁄₁₆" inch).
For non-ABS installation, begin with step 3:
3. Install the bearing and washer into the hub. Thread on the
inner nut, rotate the hub and tighten the nut to 100 Ft. Lbs.
of torque.
4. Loosen the nut to remove preload torque, do not rotate hub.
5. Hand tighten the nut, then back it off ¼ to ³⁄₈ turn.
6. Place the tang washer on the spindle and bend two tangs
inward over the nut. This will keep the inner nut from turning while torque is applied to the outer nut.
7. Install the outer nut and torque it to 100-175 Ft. Lbs. Insure
that the inner nut does not turn. Bend two tangs from the
tang washer over the outer nut flats to secure.
TRIAL MODE − a valid license will remove this message. See the keywords property of this PDF for more information.
8. Install cap with the O-ring and plug installed. Rotate the hub
and check the bearing adjustment. The allowable end play is .001"-.010".
! CAUTION
FAILURE TO BACK OFF THE INNER ADJUSTING
NUT COULD CAUSE BEARING AND AXLE SPINDLE
OVERHEATING OR DAMAGE, WHICH COULD RESULT
IN THE WHEEL LOCKING UP OR COMING OFF DURING
VEHICLE OPERATION AND LEAD TO AN ACCIDENT,
INJURIES OR DEATH.
! CAUTION
FAILURE TO TORQUE THE OUTER LOCKNUT
PROPERLY COULD CAUSE THE WHEEL END TO COME
OFF DURING VEHICLE OPERATION WHICH COULD
RESULT IN AN ACCIDENT, INJURIES OR DEATH.
TRIAL MODE − a valid license will remove this message. See the keywords property of this PDF for more information.
Axle & Suspension Installation
Responsibility for proper axle alignment lies with the axle installer. The axle must be installed so that it will be parallel to the drive axle(s) of the tractor. This will allow good vehicle control when cornering, longer tire wear, and it will eliminate dog tracking. Alignment can be determined by measuring from the center of the trailer king pin to the center of each end of the axles. The difference should not vary by more than ¹⁄₁₆". In the case of multiple axles, the axles must also be in line with each other. The difference between the centers of one axle and end centers of the other axle must not vary more than ¹⁄₈".
! CAUTION
Safety glasses should be worn at all times when
assembling or disassembling axles and their
components.
Dexter tubular axles are made of high strength steel for better fatigue life and superior welding qualities. The round tubular axles provide a uniform section modulus no matter how the beam is rotated.
Brake spiders are positioned and welded to specific requirements at our factory. Welding the spider directly to the axle beam provides a higher strength and more reliable brake attachment over bolt-on versions.
In welding suspension components to a Dexter trailer axle, extreme care must be exercised to obtain correct location and ensure the spring seat load bearing surfaces are parallel to each other. Any welding of additional attachments to the axle should be approved by Dexter Axle's engineering department.
TRIAL MODE − a valid license will remove this message. See the keywords property of this PDF for more information.
The suspension systems incorporated into Dexter axles are designed to provide the trailer owner three basic functions:
1. Attach the axle to the trailer2. Dampen the effects of road shock3. Provide stability to the trailer
All Dexter suspension systems are available in single and multiple axle configurations.
Slipper Leaf Springs
Slipper springs have an eye formed in one end only, with the other end formed into a reverse curve. The attachment of these springs is as follows:
1. The front eye is attached directly into the front hanger with a
bolt and nut.
2. The rear end of the spring is captured in the rear hanger or
equalizer with a "keeper bolt" that prevents the spring from coming out when the trailer is jacked up for service.
The articulation of this suspension occurs when the rear end of each slipper spring slides against the wear surfaces provided in the rear hangers or equalizers. This suspension is also available in single and multiple axle configurations.
TRIAL MODE − a valid license will remove this message. See the keywords property of this PDF for more information.
Inspection and Replacement
All the components of your suspension system should be visually inspected least every 6,000 miles for signs of excess wear, elongation of bolt holes, and loosening of fasteners. Whenever loose or replaced, the fasteners in your suspension system should be torqued as detailed in the charts at the end of this book (Fastener Torque Values).
Worn spring eye bushings, sagging springs, or broken springs should be replaced using the following method.
! CAUTION
Do not lift or support the trailer on any part of the axle
or suspension system. Never go under any trailer unless
it is properly supported on jack stands which have been
rated for the load. Improperly supported vehicles can
fall unexpectedly and cause serious injury or death.
1. Support the trailer with the wheels just off the ground. Follow
the trailer manufacturer's recommendations for lifting and supporting the unit. Do not lift or place supports on any part of the suspension system.
2. After the unit is properly supported, place a suitable block
under the axle tube near the end to be repaired. This block is to support the weight of the axle only so that suspension COMPONENTS can be removed.
3. Disassemble the U-bolts, nuts, and tie plates.
4. Remove the spring eye bolts and remove the spring and
place on a suitable work surface.
5. If the spring eye bushings are to be replaced, press out the
old bushing using a hydraulic shop press.
TRIAL MODE − a valid license will remove this message. See the keywords property of this PDF for more information.
! CAUTION
Be sure to wear safety glasses when removing or
installing force fitted parts. Failure to comply may result
in serious injury.
6. Lubricate the rubber bushing with liquid soap (not
petroleum.) Press the new bushing into the spring eye using a hydraulic press.
7. Reinstall repaired or replaced components in reverse order.
Note: For multiple axle units, the weight of each axle must
be supported as outlined in Step 2 before disassembly of
any component of the suspension system.
If the equalizer or equalizer bushings must be replaced, follow the instructions above for lifting and supporting the trailer unit and then proceed as follows:
1. With both axles blocked up, remove the spring eyebolt,
keeper bolt, and equalizer bolt from the equalizer to be repaired or replaced.
2. Press the old rubber bushing out of the equalizer using a
hydraulic press.
3. Lubricate the replacement bushing with liquid soap and
press into the equalizer.
4. Reassemble in reverse order.
! CAUTION
Be sure to wear safety glasses when removing or
installing force fitted parts. Failure to comply may result
in serious injury.
TRIAL MODE − a valid license will remove this message. See the keywords property of this PDF for more information.
1. Make sure springs are on straight. Align spring eyes to front
hanger. Insert spring eye bolts but do not torque at this point.
2. Assemble springs into equalizer.
3. After leveling equalizer to frame, torque equalizer nuts
to values specified in Fastener Torque Specifications (Replacement Parts/Kits section).
4. Torque spring eye bolts to values specified in Fastener
Torque Specifications (Replacement Parts/Kits section) for rubber bushed suspension. Torque bronze bushed suspension to snug fit only.
The Torflex® suspension system is a torsion arm type suspension which is completely self contained within the axle tube. It attaches directly to the trailer frame
using brackets which are
Axle Tube
an integral part of the axle assembly. The Torflex® axle provides improved
suspension characteristics relative to leaf spring axles, through the unique
Torsion Bar
arrangement of a steel
Torsion Arm
torsion bar surrounded by four natural rubber cords encased in the main structural member of the axle beam.
The spindle is attached to a lever, called the torsion arm, which is fastened to the rubber encased bar. As load is applied, the bar rotates causing a rolling/compressive resistance in the rubber cords. This action provides the same functions as conventional sprung axles with several operating advantages including independent suspension.
Except for periodic inspection of the fasteners used to attach the Torflex® axle to the vehicle frame, no other suspension
TRIAL MODE − a valid license will remove this message. See the keywords property of this PDF for more information.
maintenance is required on Torflex® axles. They are, of course, subject to the maintenance and inspection procedures regarding brakes, hubs, bearings, seals, wheels, and tires, as outlined in this manual.
DO NOT WELD ON THE TORFLEX® BEAM. It has rubber
cords inside and the heat generated by welding could
damage the cords.
TRIAL MODE − a valid license will remove this message. See the keywords property of this PDF for more information.
Heavy Duty Suspension
System Axle Alignment
For safe and efficient operation and to prevent excessive tire wear, off-tracking and hard pulling, it is recommended that after a short break-in period you have a qualified trailer mechanic check the alignment.
To align a four (4) spring suspension there is one adjustable track arm (rod) on each axle. These will typically be on the road (left) side.
Release the clamps at each end of the adjusting screw (see Figure 1). Align front axle with the king pin and adjust each axle thereafter parallel to the front axle. Be sure to secure the clamps on the adjustable track arm (rod) after alignment (see Figure 1).
Alignment Procedure (Figure 1)
Before taking axle alignment measurements, make sure the trailer is unloaded and free the suspension of any binds by pushing the trailer backwards and then pulling the trailer forward. While pulling the trailer forward on a level floor, apply the brakes and release. This will assure that an adjustable undercarriage is in its rearmost lock position. The trailer MUST be level from side to side as well as from front to rear.
Note: Neither service nor parking brakes should be applied during
the measurement procedure.
Ensure the king pin is at the correct height. Use axle end extenders (or remove outer wheels and any obstructions) to achieve a straight line for measuring from king pin to the axle ends/centers.
Proper tools for axle alignment inspection are:
• Spring loaded kingpin extender with bubble level.
• Axle end extenders.
• 50 foot steel tape.
• Adjustable tram.
• Gauge for measuring axle center to axle center.
• Track arm (rod) clamp bolts if required.
TRIAL MODE − a valid license will remove this message. See the keywords property of this PDF for more information.
Adjust Clamp Bolt / Nut
Tighten to 35 Ft. Lbs.
Adjust Clamp Bolt / Nut
Adjustable Track Tighten to 35 Ft. Lbs.
Measuring (Figure 2)
1. Lateral Centerline (E). Determine lateral centerline of trailer
body and axles by measuring distance E between trailer and axle centerlines first, and correct so that distance E is ¹⁄₄" or less for each axle.
2. Thrust Angle (A, B). Measure distances A (curbside)
then B (roadside) from the king pin to the front of the axle. These must be equal to within 0.1 degree or ¹⁄₈" of each other (A = B ± ¹⁄₈"). Ensure the lateral tension (pulling force) applied to the measuring tape is the same for both A and B measurements. Use a tensioning device scale or optical (laser) to ensure accuracy.
3. Scrub Angle (C, D). Measure distances C (curbside) then
D (roadside) between axles, measuring from front of axle extension to front of axle extension (same as center to center). These also must be equal to within ¹⁄₁₆" of each other (C = D ± ¹⁄₁₆"). This measurement should be as close to zero as possible. The smaller the offset, the lower the rolling resistance and the better the fuel economy.
TRIAL MODE − a valid license will remove this message. See the keywords property of this PDF for more information.
1. Loosen the adjustable track rod clamp bolts (Figure 1) and
turn the center rod to adjust as necessary per above.
2. After adjusting, tighten the adjustable track rod clamp nuts
to proper torque (Figure 1) and recheck measurements.
1. Always measure to the front axle ends for accurate
2. Avoid measuring to rims, suspension brackets, hub cap
vent holes, brake drums, etc. This can result in improper alignment. For accurate measurements, use extenders.
3. Always align any succeeding axles with the front axles, not
the kingpin.
Additional Suspension Maintenance Check
Track arms should be checked for clearance. If slack is found, it should be repaired immediately since this indicates that there is wear in the rubber bushing or track arm parts. Check the adjustable track arm clamps for proper torque. Loose clamps will cause wear on the adjusting threads and the suspension cannot
Suspensions be kept in alignment. On leaf spring type suspensions, have the
TRIAL MODE − a valid license will remove this message. See the keywords property of this PDF for more information.
trailer checked for axle alignment after two to three thousand miles.
Check leaf springs for broken leaves. Replace broken leaves immediately to prevent the other leaves from being overloaded. On taper leaf springs, be sure the plastic liner is serviceable and on top of the spring. The liners between leaves should be in place and serviceable.
Heavy Duty Suspension Torque Requirements
Before torquing equalizer bolts, level equalizers parallel
to main frame members. After initial break-in period (up
to 1,000 miles) and at least every 4 months thereafter;
all bolts and nuts should be checked to ensure
recommended torque is being maintained.
Minimum Torque Values for Bolts With
Clean Dry Threads
Torque Min
Torque Max
1¹⁄₈-7 UNC Nut
Spring Keeper Nut⁵⁄₈-18 UNF
Track Rod Clamp Nut⁵⁄₈-18 UNF
TRIAL MODE − a valid license will remove this message. See the keywords property of this PDF for more information.
Wheels are a very important and critical component of your running gear system. When specifying or replacing your trailer wheels it is important that the wheels, tires, and axle are properly matched. The following characteristics are extremely important and should be thoroughly checked when replacement wheels are considered.
1. Bolt Circle. Many bolt circle dimensions are available and
some vary by so little that it might be possible to attach an improper wheel that does not match the axle hub. Be sure to match your wheel to the axle hub.
2. Capacity. Make sure that the wheels have enough
load carrying capacity and pressure rating to match the maximum load of the tire and trailer.
3. Offset. This refers to the relationship of the center line of
the tire to the hub face of the axle. Care should be taken to match any replacement wheel with the same offset wheel as originally equipped. Failure to match offset can result in reducing the load carrying capacity of your axle.
4. Rim Contour.
! CAUTION
Replacement tires must meet the same specifications
as the originals. Mismatched tires and rims may come
apart with explosive force and cause personal injury to
yourself or others. Mismatched tires and rims can also
blow out and cause you to lose control and have an
accident which can result in serious injury or death.
Wheels and Tires
TRIAL MODE − a valid license will remove this message. See the keywords property of this PDF for more information.
Wheels and Tires
! CAUTION
Do not attempt to repair or modify a wheel. Even minor
modifications can have a great effect. Do not install
a tube to correct a leak through the rim. If the rim is
cracked, the air pressure in the tube may cause the
pieces of the rim to explode with great force and can
cause serious injury or death.
It is extremely important to apply and maintain proper wheel
mounting torque on your trailer axle. Torque is a measure of
the amount of tightening applied to a fastener (nut or bolt) and
is expressed as length times force. For example, a force of 90
pounds applied at the end of a wrench one foot long will yield
90 Ft. Lbs. of torque. Torque wrenches are the best method to
assure the proper amount of torque is being applied to a fastener.
! CAUTION
Wheel nuts or bolts must be tightened and maintained
at the proper torque levels to prevent loose wheels,
broken studs, and possible dangerous separation of
wheels from your axle, which can lead to an accident,
personal injuries or death.
Be sure to use only the fasteners matched to the cone angle of your wheel (usually 60° or 90°.) The proper procedure for attaching your wheels is as follows:
1. Start all bolts or nuts by hand to prevent cross threading.
2. Tighten bolts or nuts in the following sequence.
3. The tightening of the fasteners should be done in stages.
Following the recommended sequence, tighten fasteners per wheel torque requirements diagram.
TRIAL MODE − a valid license will remove this message. See the keywords property of this PDF for more information.
4. Wheel nuts/bolts should be torqued before first road use
and after each wheel removal. Check and re-torque after the first 50 miles and again at 100 miles. Check periodically thereafter.
Wheel Torque Sequence
⁵⁄₈-18 90° Cone Nut
³⁄₄-10 Hex Nut
³⁄₄-16 Spherical Nut
1¹⁄₈-16 Spherical Nut
⁵⁄₈-18 Non-Swiveling
⁵⁄₈-18 Swiveling
Wheels and Tires
TRIAL MODE − a valid license will remove this message. See the keywords property of this PDF for more information.
Wheels and Tires
Before mounting tires onto wheels, make certain that the rim size and contour is approved for the tire as shown in the Tire and Rim Association Yearbook or the tire manufacturers catalog. Also make sure the tire will carry the rated load. If the load is not equal on all tires due to trailer weight distribution, use the tire rated for the heaviest wheel position.
Use tire mounting procedures as outlined by the Rubber Manufacturers Association or the tire manufacturers.
Tire inflation pressure is the most important factor in tire life. Inflation pressure should be as recommended by the manufacturer for the load. Pressure should be checked cold before operation. Do not bleed air from tires when they are hot. Check inflation pressure weekly during use to insure the maximum tire life and tread wear. The following tire wear diagnostic chart will help you pinpoint the causes and solutions of tire wear problems.
! CAUTION
Proper matching of the tire/wheel combination is
essential to proper function of your trailer running gear.
Some tires may call for a maximum inflation pressure
above the rim or wheel capacity. DO NOT EXCEED
MAXIMUM INFLATION PRESSURES FOR RIMS OR
WHEELS. Catastrophic failure may result.
TRIAL MODE − a valid license will remove this message. See the keywords property of this PDF for more information.
Tire Wear Diagnostic Chart
Wear Pattern
Adjust pressure to
Center Wear
particular load pertire catalog
Adjust pressure to
Edge Wear
particular load pertire catalog
Make sure load doesn't
Side Wear
exceed axle rating.
Align at alignment shop.
Align at alignment shop.
Check bearing adjust-ment and balance tires.
Avoid sudden stops
Flat Spots
when possible and
adjust brakes.
Tire wear should be checked frequently. Once a wear
pattern becomes firmly established in a tire it is difficult
to stop, even if the underlying cause is corrected.
Wheels and Tires
TRIAL MODE − a valid license will remove this message. See the keywords property of this PDF for more information.
Fastener Torque Specifications
See Bearing Installation/Adjustment
³⁄₈-16 Self Locking Shoe Hold Down
⁵⁄₈-11 Hex Locknut
¹⁄₂-13 Hex Head
¹⁄₂-13 Hex Cap
⁵⁄₈-11 Hex Locknut
³⁄₄-10 Hex Locknut
10K GD Spring Eye
³⁄₄-10 Hex Locknut
Spring Eye Rubber Bushed
1¹⁄₈-7 Hex Locknut
Equalizer Rubber Bushed
⁷⁄₁₆-20 Hex Nut
TRIAL MODE − a valid license will remove this message. See the keywords property of this PDF for more information.
Bearing Replacement Chart
Industry No.
Industry No.
Seal Replacement Reference
Part Number
Kit Number
Electric Brake Magnets
Magnet Kit Number
Brake Size
(one magnet per kit)
Wire Color
12¹⁄₄" x 3³⁄₈" 9K, 10K
12¹⁄₄" x 4" 10K
12¹⁄₄" x 5" 12K
12¹⁄₄" x 5" 15K
TRIAL MODE − a valid license will remove this message. See the keywords property of this PDF for more information.
Brake Shoe Replacement Kits
Brake Size
Shoe and Lining Replacement
12¹⁄₄" x 3³⁄₈"
Electric Cast Back Plate
K71-499-00 LH; K71-498-00 RH
Electric Stamped Back Plate
K71-049-00 LH; K71-050-00 RH
K71-165-00 LH; K71-166-00 RH
12¹⁄₄" x 4"
Electric Cast Back Plate
K71-501-00 LH; K71-500-00 RH
Electric Stamped Back Plate
K71-051-00 LH; K71-052-00 RH
K71-167-00 LH; K71-168-00 RH
12¹⁄₄" x 5"
Electric Cast Back Plate
K71-503-00 LH; K71-502-00 RH
Electric Stamped Back Plate
K71-053-00 LH; K71-054-00 RH
K71-169-00 LH; K71-170-00 RH
Air Brake Shoe & Linings
Shoe & Lining No.
Axle Model
Brake Size
(2 Required per Brake)
12¹⁄₄" x 4"
12¹⁄₄" x 5"
Air Brake Repair Kits
Axle Model
Kit Number
Camshaft PQ Style Repair Kit
Brake Shoe PQ Style Hardware Kit
Disc Brake Pad Kit
Axle Model
Kit Number
Disc Brake Caliper Repair Kit
Axle Model
Kit Number
TRIAL MODE − a valid license will remove this message. See the keywords property of this PDF for more information.
If your trailer is to be stored for an extended period of time or over the winter, it is important that the trailer be prepared properly.
1. Remove the emergency breakaway battery and store inside,
out of the weather. Charge the battery at least every 90 days.
2. Jack up the trailer and place jack stands under the trailer
frame so that the weight will be off the tires. Follow trailer manufacturer's guidelines to lift and support the unit. Never jack up or place jack stands on the axle tube or on the equalizers.
! CAUTION
Do not lift or support the trailer on any part of the axle
or suspension system. Never go under any trailer unless
it is properly supported on jack stands which have been
rated for the load. Improperly supported vehicles can
fall unexpectedly and cause serious injury or death.
3. Lubricate mechanical moving parts such as the hitch, and
suspension parts, that are exposed to the weather.
4. Boat trailer axles are subject to repeated immersion. Before
storing, remove brake drums; clean, dry and re-lubricate moving brake components; inspect bearings - clean and re-lubricate.
5. On oil lubricated hubs, the upper part of the roller bearings
are not immersed in oil and are subject to potential corrosion. For maximum bearing life, it is recommended that you revolve your wheels periodically (every 2-3 weeks) during periods of prolonged storage.
TRIAL MODE − a valid license will remove this message. See the keywords property of this PDF for more information.
After Prolonged Storage
Inspection Procedure
Before removing trailer from jack stands:
1. Remove all wheels and hubs or brake drums. Note which
spindle and brake that the drum was removed from so that it can be reinstalled in the same location.
2. Inspect suspension for wear.
3. Check tightness of hanger bolt, shackle bolt, and U-bolt nuts
per recommended torque values.
4. Check brake linings, brake drums and armature faces for
excessive wear or scoring.
5. Check brake magnets with an ohmmeter. The magnets
should check 3.2 ohms. If shorted or worn excessively, they must be replaced.
6. Lubricate all brake moving parts using a high temperature
brake lubricant (LUBRIPLATE or Equivalent).
Do not get grease or oil on brake linings or magnet face.
7. Remove any rust from braking surface and armature surface
of drums with fine emery paper or crocus cloth. Protect bearings from contamination while so doing.
8. Inspect oil or grease seals for wear or nicks. Replace if
9. Lubricate hub bearings. Refer to procedure in manual.
10. Reinstall hubs and adjust bearings per instructions in
11. Mount and tighten wheels per instructions in manual.
TRIAL MODE − a valid license will remove this message. See the keywords property of this PDF for more information.
Trip Preparation Checklist
There are a number of simple rules to follow in caring for your trailer axle assembly that can add to its life and in the case of some of these rules, you may be protecting your own life as well.
Using the following checklist before starting a trip with your trailer is highly recommended. Some of these items should be checked 2-3 weeks prior to a planned trip to allow sufficient time to perform maintenance.
1. Check your maintenance schedule and be sure you are
2. Check hitch. Is it showing wear? Is it properly lubricated?
3. Fasten safety chains and breakaway switch actuating
chain securely. Make certain the breakaway battery is fully charged.
4. Inspect towing hookup for secure attachment.
5. Load your trailer so that approximately 10% of the trailer's
total weight is on the hitch. For light trailers this should be increased to 15%. Fifth wheel type trailer should have 15-25% weight on the hitch.
6. Do Not Overload. Stay within your gross vehicle rated
capacity (consult your trailer's identification plate).
7. Inflate tires according to manufacturer's specifications;
inspect tires for cuts, excessive wear, etc.
8. Check wheel mounting nuts/bolts with a torque wrench.
Torque in proper sequence, to the levels specified in this manual.
9. Make certain the brakes are synchronized and functioning
10. Check tightness of hanger bolt, shackle bolt, and U-bolt nuts
per torque values specified in manual.
11. Check operation of all lights.
12. Check that your trailer is towing in a level position and adjust
hitch height if required.
TRIAL MODE − a valid license will remove this message. See the keywords property of this PDF for more information.
Dexter Axle Limited Warranty
WHAT PRODUCTS ARE COVERED All Dexter Axle Company ("Dexter Axle") trailer axles, suspensions, and brake control systems excluding Dexter 6000 series Manufactured Housing Axles.
LIMITED 1 YEAR WARRANTY
As specified in Dexter Axle's current publication "Operation
Maintenance Service Manual", grease and oil seals FOR ALL
PRODUCTS have a one (1) year limited warranty from the date
of first sale of the trailer incorporating such components. Except
as to grease and oil seals, the following four other warranties
are available.
LIMITED 2 YEAR WARRANTY Dexter Axle warrants to the original purchaser that its axles, suspension systems, and E/H hydraulic brake actuators shall be free from defects in material and workmanship for a period of two (2) years from the date of first sale of the trailer incorporating such components.
Dexter Axle warrants to the original purchaser that its Genuine Replacement Parts shall be free from defects in material and workmanship for a period of two (2) years from the date parts were installed and serviced.
LIMITED 3 YEAR WARRANTY Dexter Axle warrants to the original purchaser of a trailer equipped with axle models D90, D100GD, D100HD, D120, or D150 and installed with properly matched Genuine Dexter Hanger and Attaching Parts Kits (HAP Kits) or Dexter Heavy Duty Suspension System (HDSS), that this combination of components shall be free from defects in material and workmanship for a period of three (3) years. The warranty period shall begin from the date of the original purchase of the trailer.
LIMITED 5 YEAR WARRANTY Dexter Axle warrants to the original purchaser that its Nev-R-Lube® bearings and the suspension components only, of its Torflex® axles shall be free from defects in material and workmanship for a period of five (5) years from the date of first sale of the trailer incorporating such components.
TRIAL MODE − a valid license will remove this message. See the keywords property of this PDF for more information.
LIMITED 7 YEAR WARRANTY Dexter Axle warrants to the original purchaser that its Predator Series® electric brake controllers shall be free from defects in material and workmanship for a period of seven (7) years from the date of purchase.
EXCLUSIVE REMEDY Dexter Axle will, at its option, repair or replace the affected components of any defective axle, repair or replace the entire defective axle, or refund the then-current list price of the axle. In all cases, a reasonable time period must be allowed for warranty repairs to be completed. Allowance will only be made for installation costs specifically approved by Dexter Axle.
WHAT YOU MUST DO In order to make a claim under these warranties:1. You must be the original purchaser of the vehicle in which
the spring suspension axles or Torflex® axles were originally installed.
2. You must promptly notify us within the warranty period of any
defect, and provide us with the axle serial number and any substantiation which may include, but is not limited to, the return of part(s) that we may reasonably request.
3. The axles or suspensions must have been installed and
maintained in accordance with good industry practice and any specific Dexter Axle recommendations, including those specified in Dexter Axle's current publication "Operation Maintenance Service Manual."
EXCLUSIONS These warranties do not extend to or do not cover defects caused by: 1. The connecting of brake wiring to the trailer wiring or trailer
wiring to the towing vehicle wiring.
2. The attachment of the running gear to the frame.
3. Hub imbalance, or any damage caused thereby. 4. Parts not supplied by Dexter Axle. 5. Any damage whatever caused by or related to any alteration of
the axle including welding supplemental brackets to the axle.
6. Use of an axle on a unit other than the unit to which it was
originally mounted.
7. Normal wear and tear. 8. Alignment.
Warranty 9. Improper installation.
TRIAL MODE − a valid license will remove this message. See the keywords property of this PDF for more information.
10. Unreasonable use (including failure to provide reasonable and
necessary maintenance as specified in Dexter Axle's current publication "Operation Maintenance Service Manual" including required maintenance after "Prolonged Storage").
11. Improper wheel nut torque. 12. Cosmetic finish or corrosion.
LIMITATIONS
1. In all cases, Dexter Axle reserves the right to fully
satisfy its obligations under the Limited Warranties by
refunding the then-current list price of the defective axle
(or, if the axle has been discontinued, of the most nearly
comparable current product).
2. Dexter Axle reserves the right to furnish a substitute or
replacement component or product in the event an axle or any component of the axle is discontinued or is otherwise unavailable.
3. These warranties are nontransferable.
GENERAL
THE FOREGOING WARRANTIES ARE EXCLUSIVE AND IN
LIEU OF ALL OTHER WARRANTIES EXCEPT THAT OF TITLE,
WHETHER WRITTEN, ORAL OR IMPLIED, IN FACT OR IN LAW
(INCLUDING ANY WARRANTY OF MERCHANTABILITY OR
FITNESS FOR A PARTICULAR PURPOSE).
These warranties give you specific legal rights, and you may also have other rights which vary from state to state.
DEXTER AXLE HEREBY EXCLUDES INCIDENTAL AND
CONSEQUENTIAL DAMAGES, INCLUDING LOSS OF TIME,
INCONVENIENCE, LOSS OF USE, TOWING FEES, TELEPHONE
CALLS OR COST OF MEALS, FOR ANY BREACH OF ANY
EXPRESS OR IMPLIED WARRANTY.
Some states do not allow limitations on how long an implied warranty lasts, or the exclusion or limitation of incidental or consequential damages, so the above exclusion or limitation may not apply to you.
Inquiries regarding these warranties should be sent to:
Dexter Axle Company P.O. Box 250 Elkhart, Indiana 46515
Note: Current publication "Operation Maintenance Service
Manual" can be found at www.dexteraxle.com.
TRIAL MODE − a valid license will remove this message. See the keywords property of this PDF for more information.
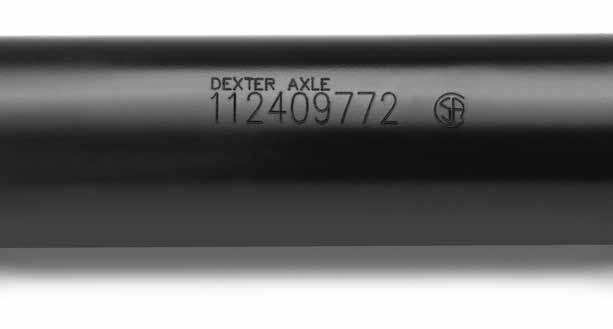
In the unlikely event that you should require service assistance from Dexter Axle, please have the lot number of the axle available when you call.
On all axles produced after April 2001, this nine digit number can be found on the rear side of the axle beam approximately 18" from the curb side of the vehicle. Look for the words DEXTER AXLE and the lot number will be located directly under the name.
TRIAL MODE − a valid license will remove this message. See the keywords property of this PDF for more information.
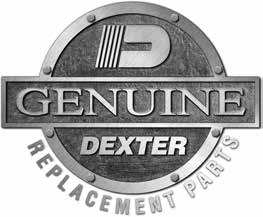
Dexter Online Parts Store
From magnets and seals to complete brake and hub kits, Dexter offers a complete line of genuine replacement parts for your trailer. Most products are available in-stock and ready to ship within 24 hours direct to you from the factory. With dedicated customer support, quick turnaround and a 30-day money back guarantee, the Dexter Online Parts Store helps keep your trailer going.
• Hub Components
• Brake Components
• Suspension Components
• Complete Hub Kits
• Brake Assemblies & Kits
• Brake Controllers & Actuators
Ready for Immediate Shipment
Direct to Your Door
Visit us online at www.dexteraxle.com
TRIAL MODE − a valid license will remove this message. See the keywords property of this PDF for more information.
Dexter Video Gallery
In keeping with our continual commitment to industry safety and the development of innovative products, please feel free to view our ongoing video gallery at "www.dexteraxle.com/video_gallery" or scan the following QR codes. We are confident these videos will help educate and promote the Dexter product line that you, as our customer, are investing in.
Bearing Maintenance
E/H Actuator Installation
E-Z Flex® Suspension
E-Z Lube® System
Genuine Replacement Parts
Leaf Spring Axles
Nev-R-Adjust® Brakes
Removable Spindle
Torflex® Suspension Axles
TRIAL MODE − a valid license will remove this message. See the keywords property of this PDF for more information.
TRIAL MODE − a valid license will remove this message. See the keywords property of this PDF for more information.
TRIAL MODE − a valid license will remove this message. See the keywords property of this PDF for more information.
Genuine Dexter axles and components are available
nationwide from our plant locations listed below or
through our network of distributors. Check our web site
for the distributor nearest you.
Visit us online at www.dexteraxle.com
301 West Pearl Street
500 South 7th Street
Fremont, IN 46737
Fax (260) 495-1701
Fax (260) 636-3030
Ph (260) 495-5100
Ph (260) 636-2195
2900 Industrial Parkway East
Elkhart, IN 46516
Fax (574) 295-8666
Ph (574) 295-7888
Dexter Axle500 Southeast 27th Street
El Reno, OK 73036
199 Perimeter Road
Fax (405) 262-9089
Monticello, GA 31064
Ph (405) 262-6700
Fax (706) 468-2966Ph (706) 468-6495
NO PART OF THIS CATALOG MAY BE REPRODUCED WITHOUT DEXTER AXLE'S PERMISSION.
ALL PART NUMBERS, DIMENSIONS AND SPECIFICATIONS IN THIS CATALOG ARE SUBJECT
TO CHANGE WITHOUT NOTICE.
TRIAL MODE − a valid license will remove this message. See the keywords property of this PDF for more information.
GEARED FOR INNOVATION SINCE 1960
2900 Industrial Parkway East n Elkhart, IN 46516
Phone: 574-295-7888 n Fax: 574-295-8666
1995-2014 Dexter Axle Company. LIT-006-00
TRIAL MODE − a valid license will remove this message. See the keywords property of this PDF for more information.
Source: http://www.plumbers.cc/images/schutt/manuals/9-15K_Complete_Service_Manual-1.pdf
YEARBOOK OF PHYSICAL ANTHROPOLOGY 36:153—178 (1993) G6PD Deficiency as Protection Against falciparumMalaria: An Epidemiologic Critique of Population andExperimental Studies LAWRENCE S. GREENEDepartment of Anthropology and the Biology of Human Populations Program, University of Massachusetts, Boston 02125, and Boston Sickle Cell Center and the Department of Pediatrics, Boston City Hospital,
Règlement intérieur au 29 mars 2016 Le règlement intérieur précise les conditions d'application des statuts. Il est adopté et modifié dans les conditions fixées par les statuts. Article 1 : Siège social Le siège social est situé 4 rue Chérubini, Paris 75002 Article 2 : L'Assemblée Générale Ordinaire Mission de l'Assemblée Générale Ordinaire